Taizhou Best Team Technology BTT-RC Remote Control Transmitter User Manual FCC ID XNS BTT RC Users manual Updated
Taizhou Best Team Technology Limited Remote Control Transmitter FCC ID XNS BTT RC Users manual Updated
FCC ID XNS BTT RC Users manual Updated
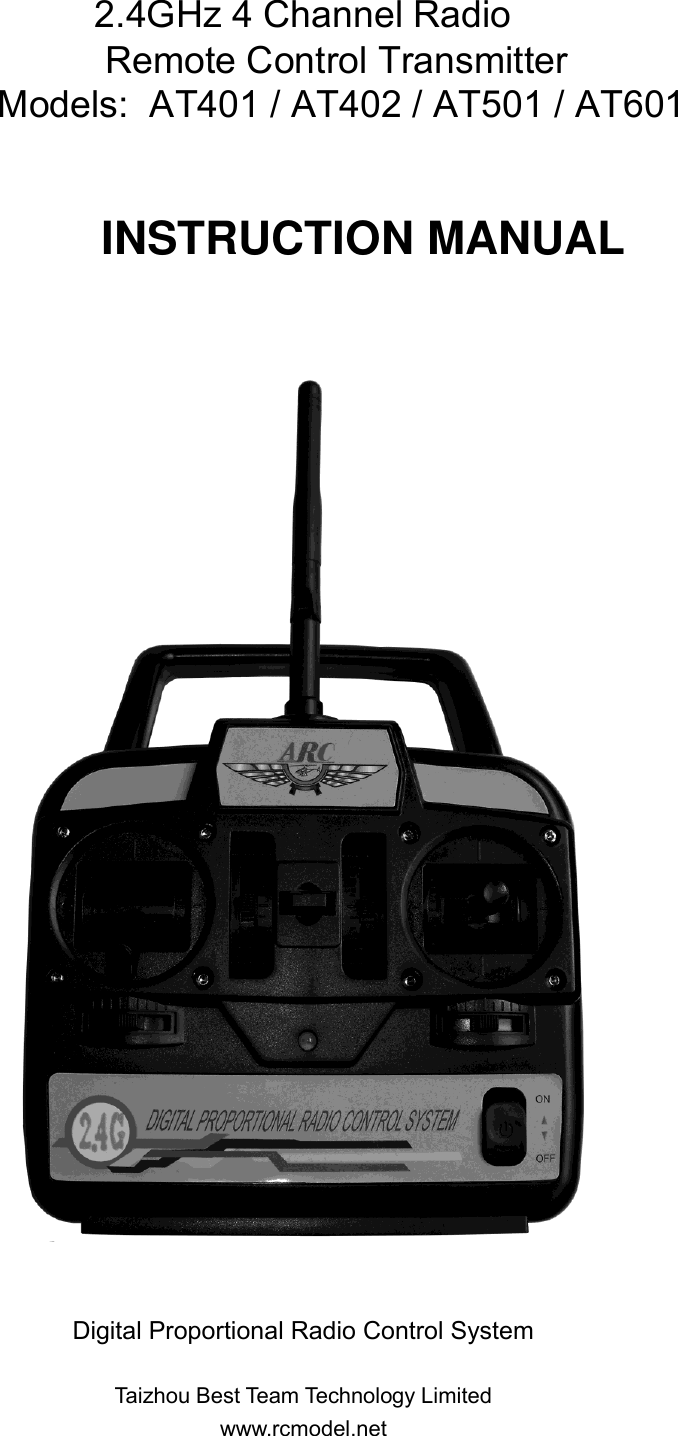
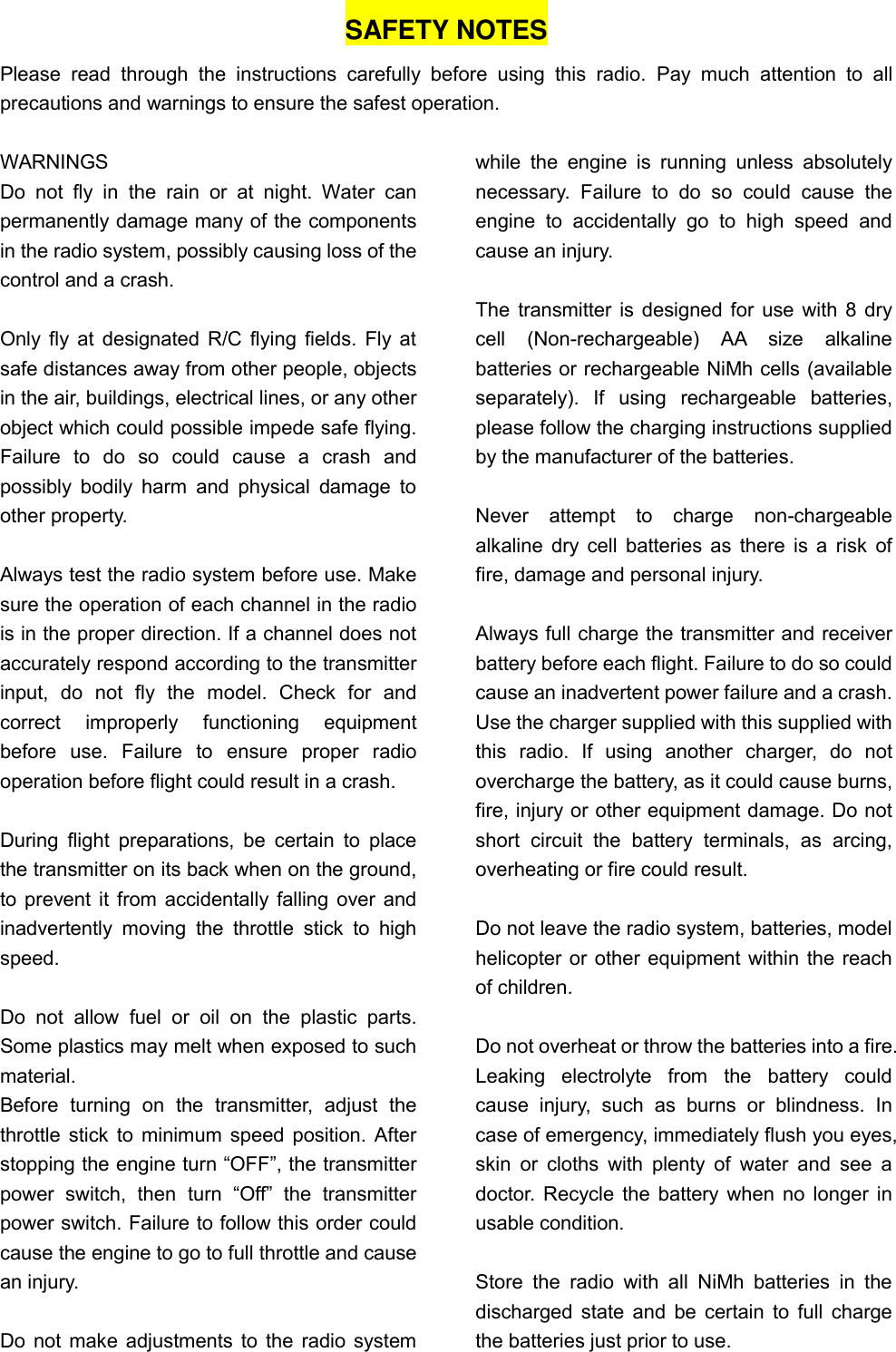
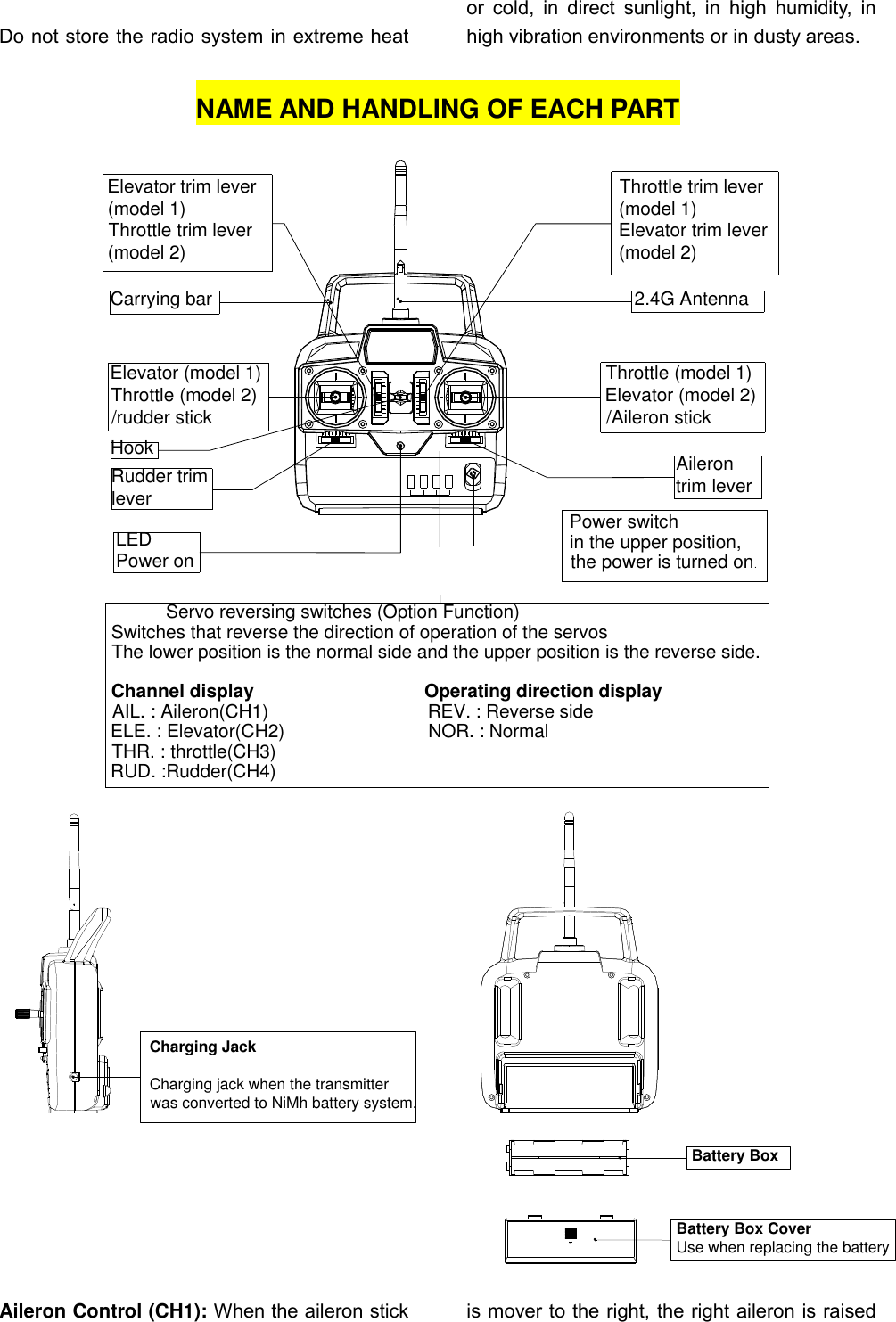

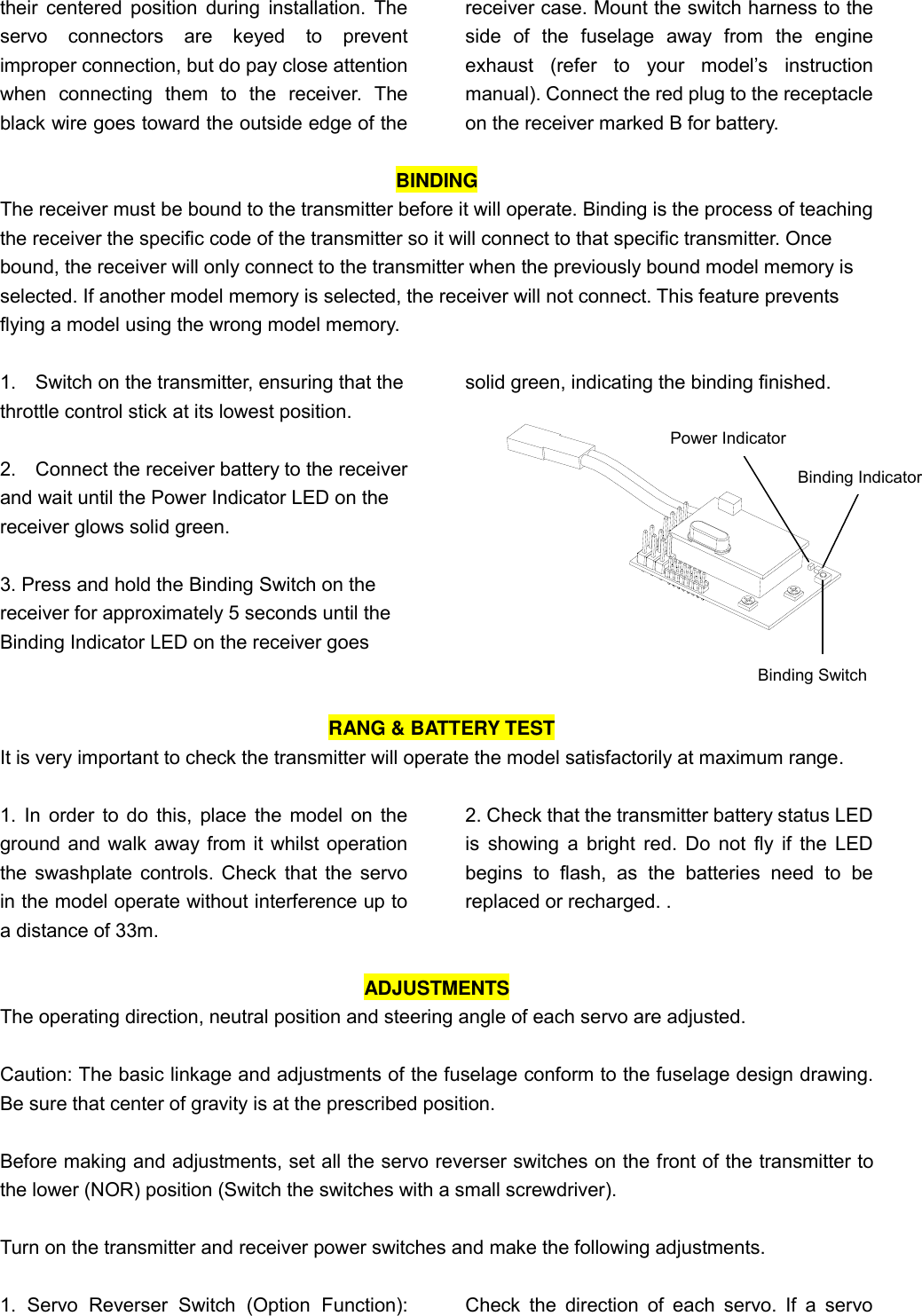
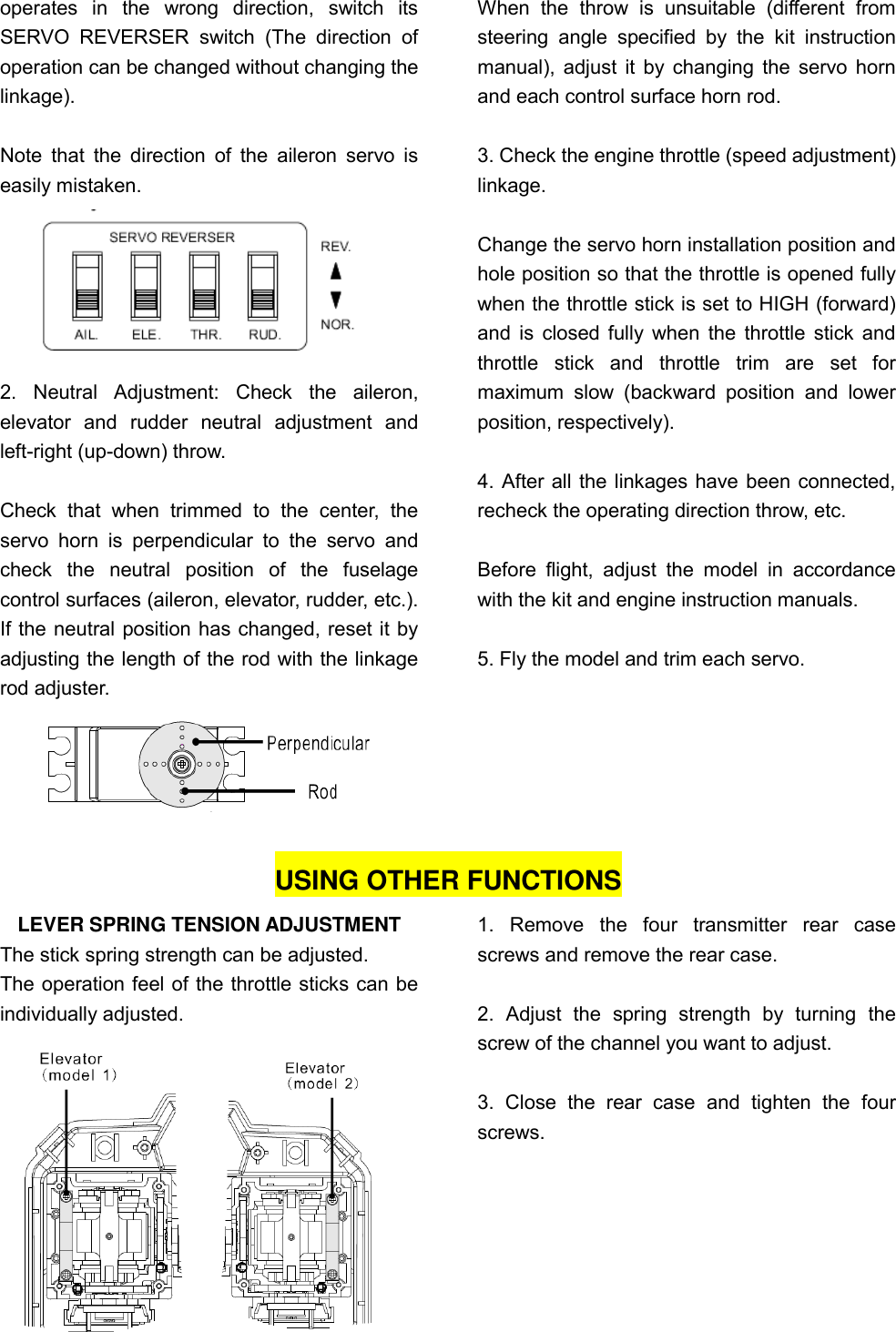
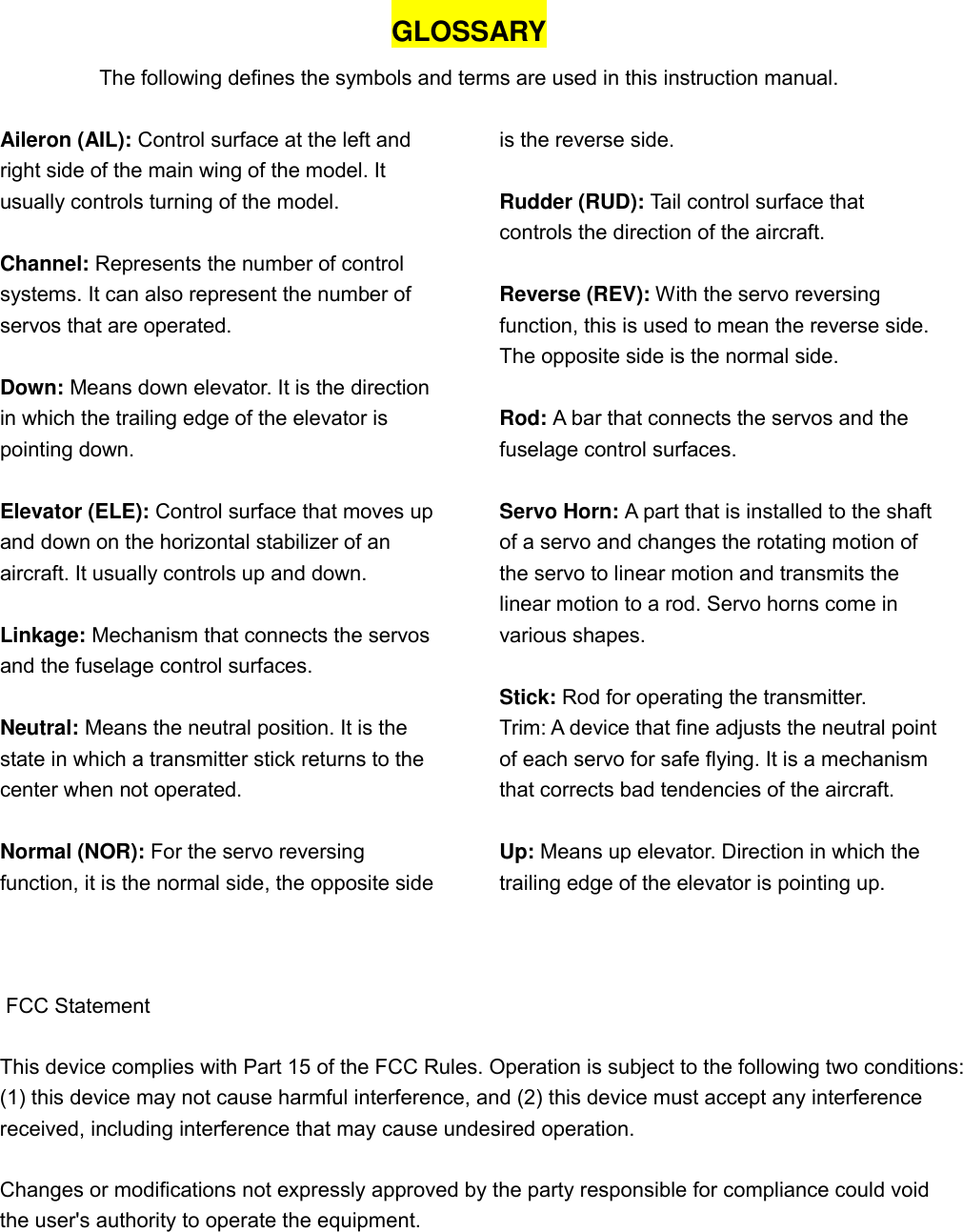