Nokia Solutions and Networks T5BQ1 Part 22 Cellular CDMA base station User Manual IHET5BQ1 Part 2 of 3
Nokia Solutions and Networks Part 22 Cellular CDMA base station IHET5BQ1 Part 2 of 3
Contents
- 1. IHET5BQ1 User Manual Part 1 of 3
- 2. IHET5BQ1 User Manual Part 2 of 3
- 3. IHET5BQ1 User Manual Part 3 of 3
IHET5BQ1 User Manual Part 2 of 3
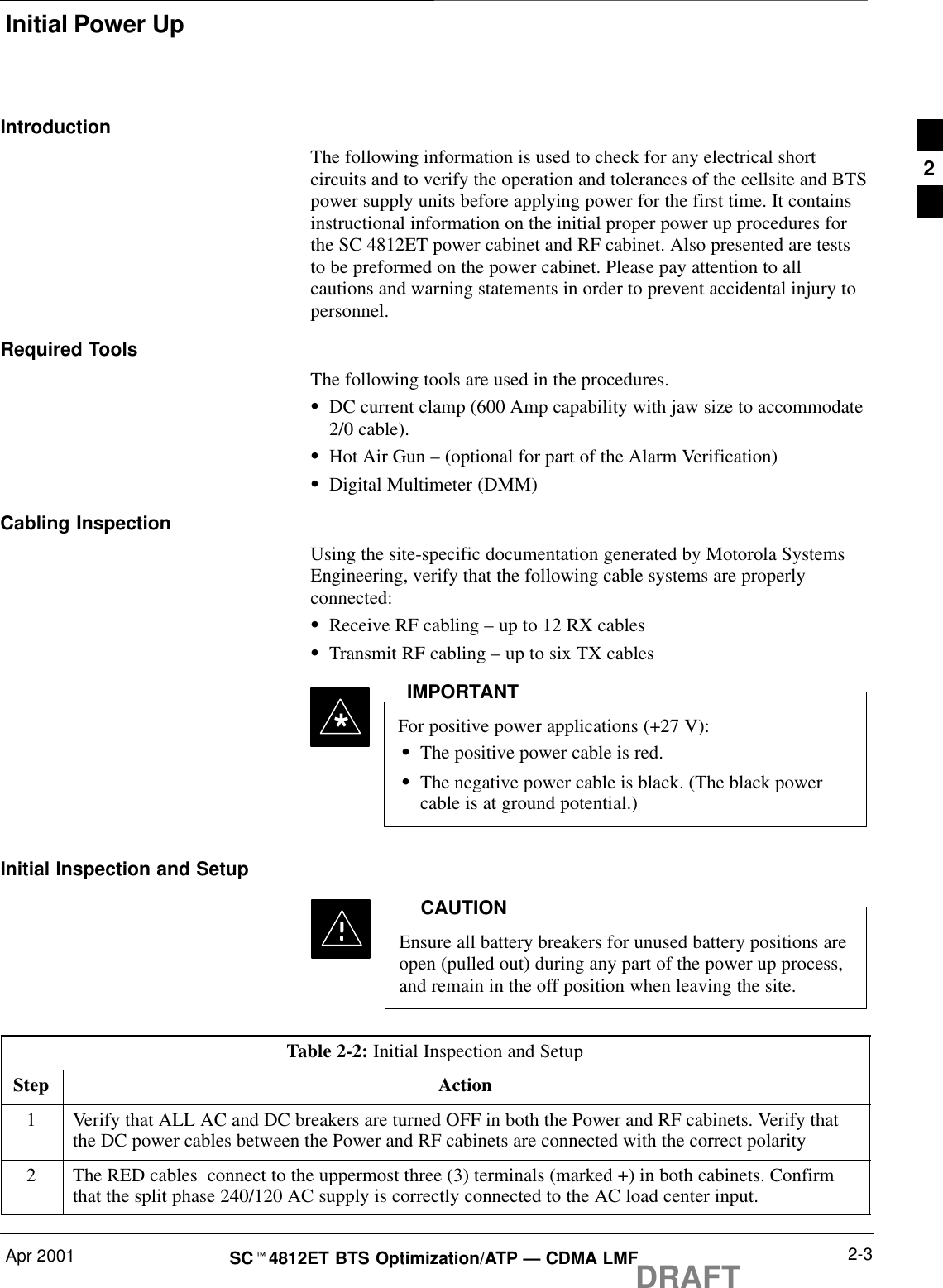
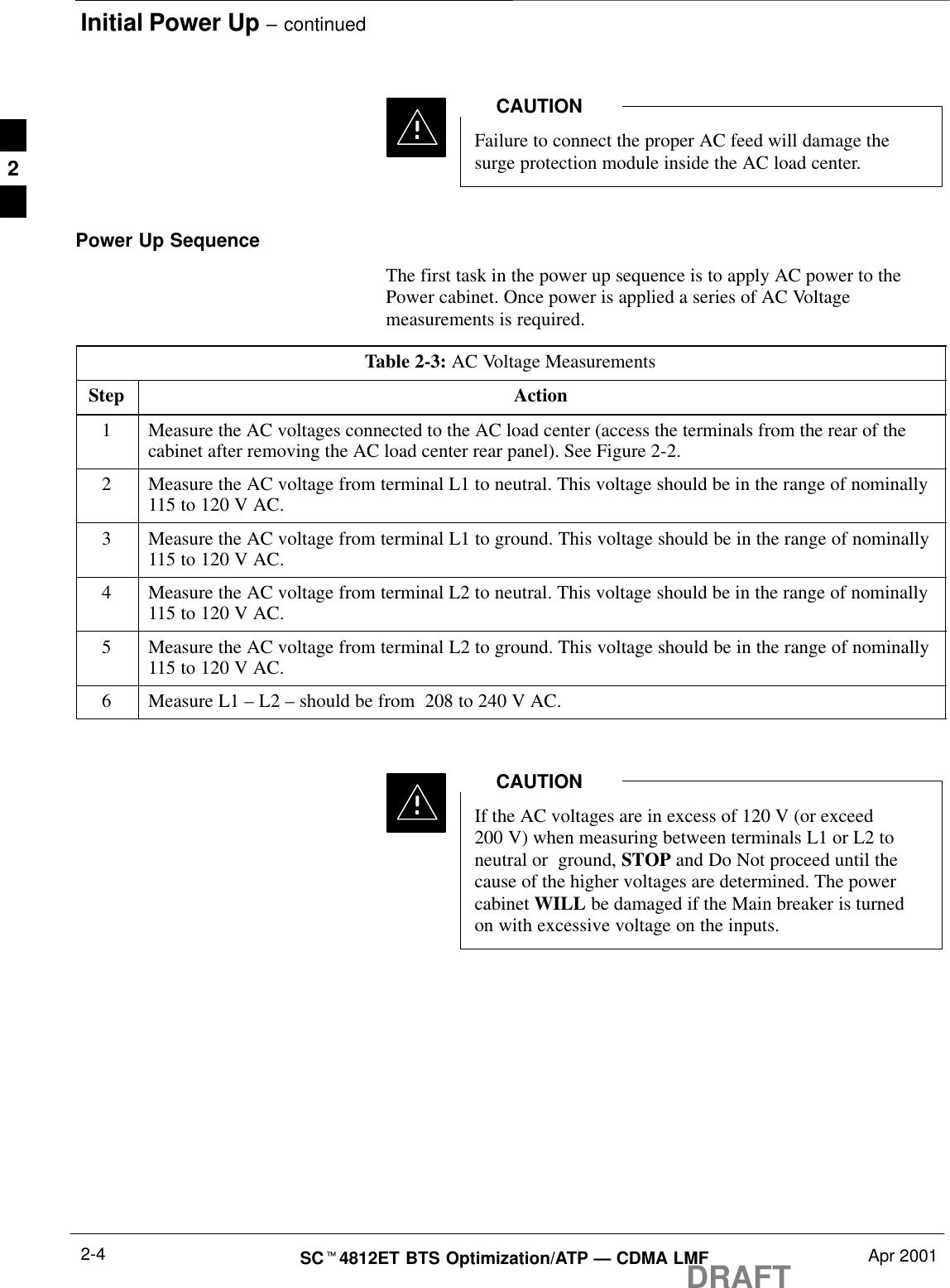
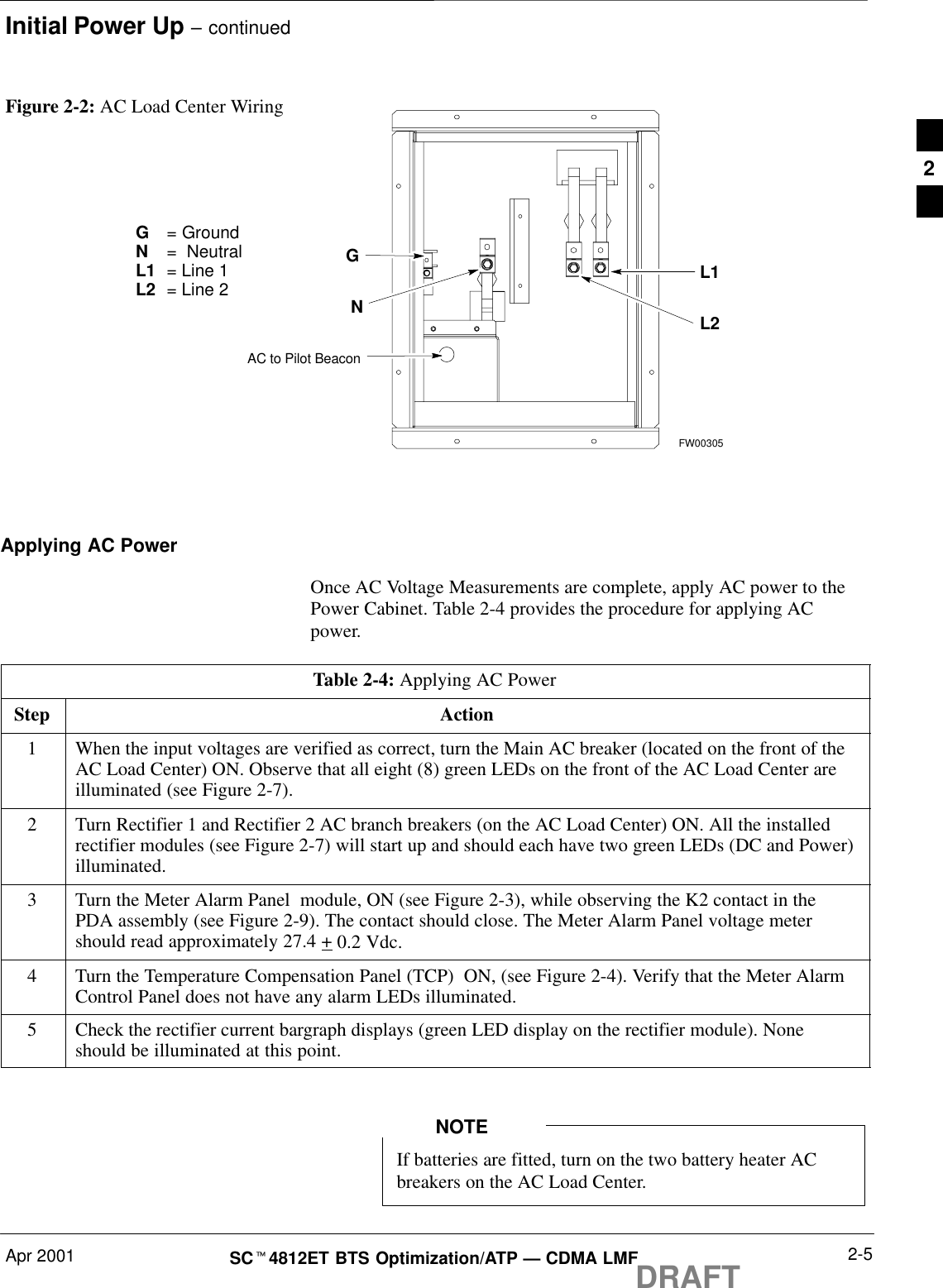

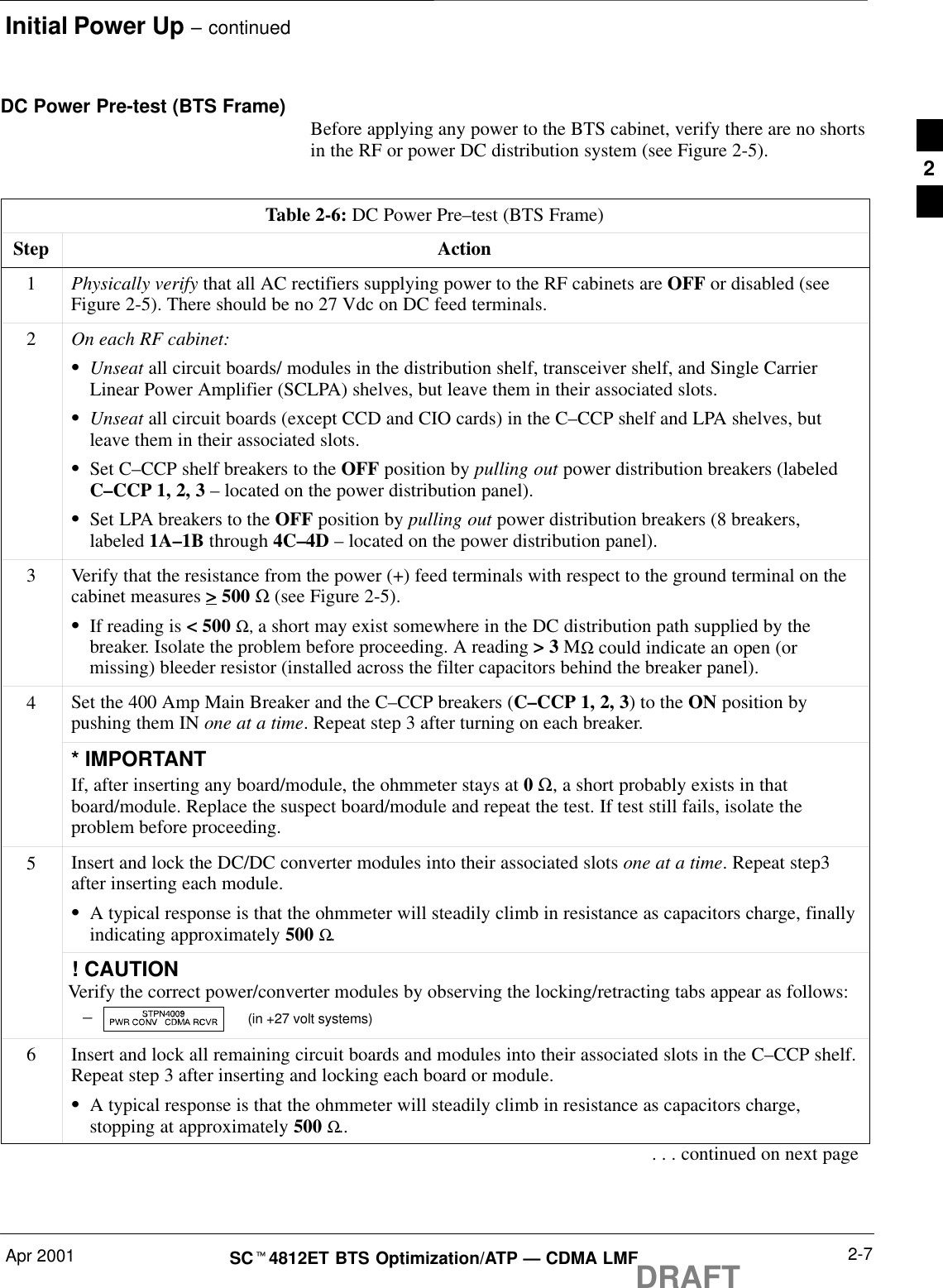
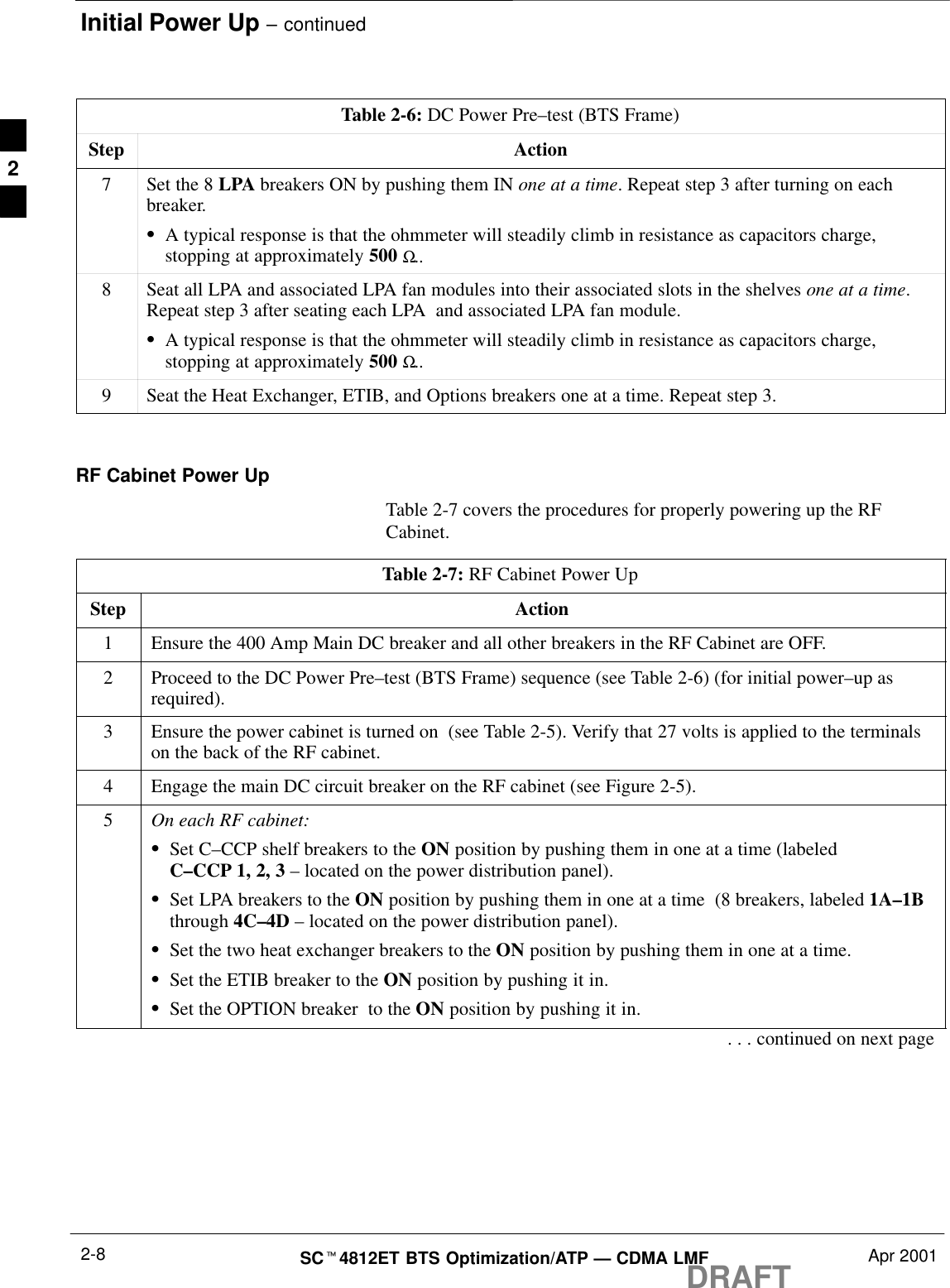
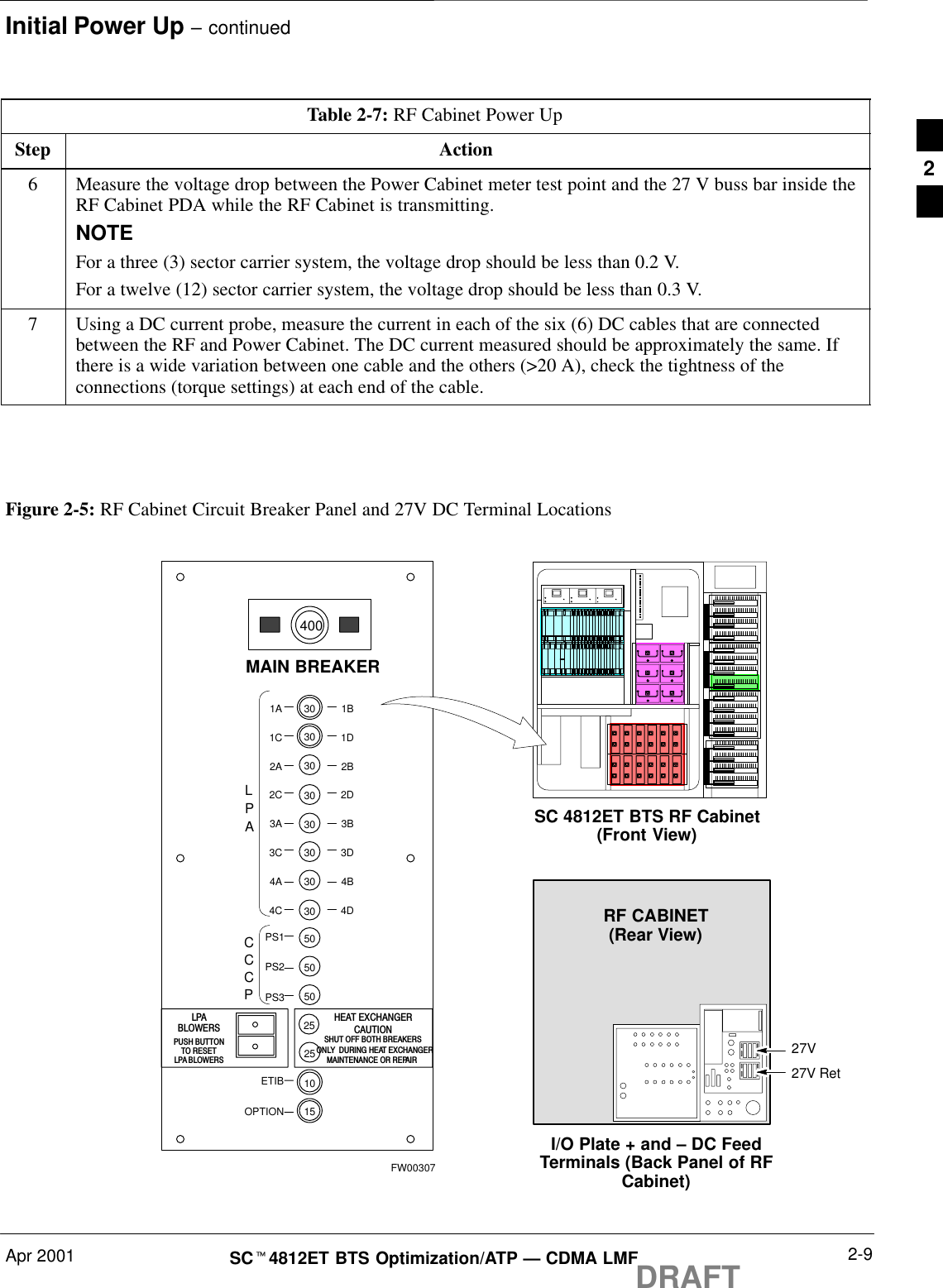
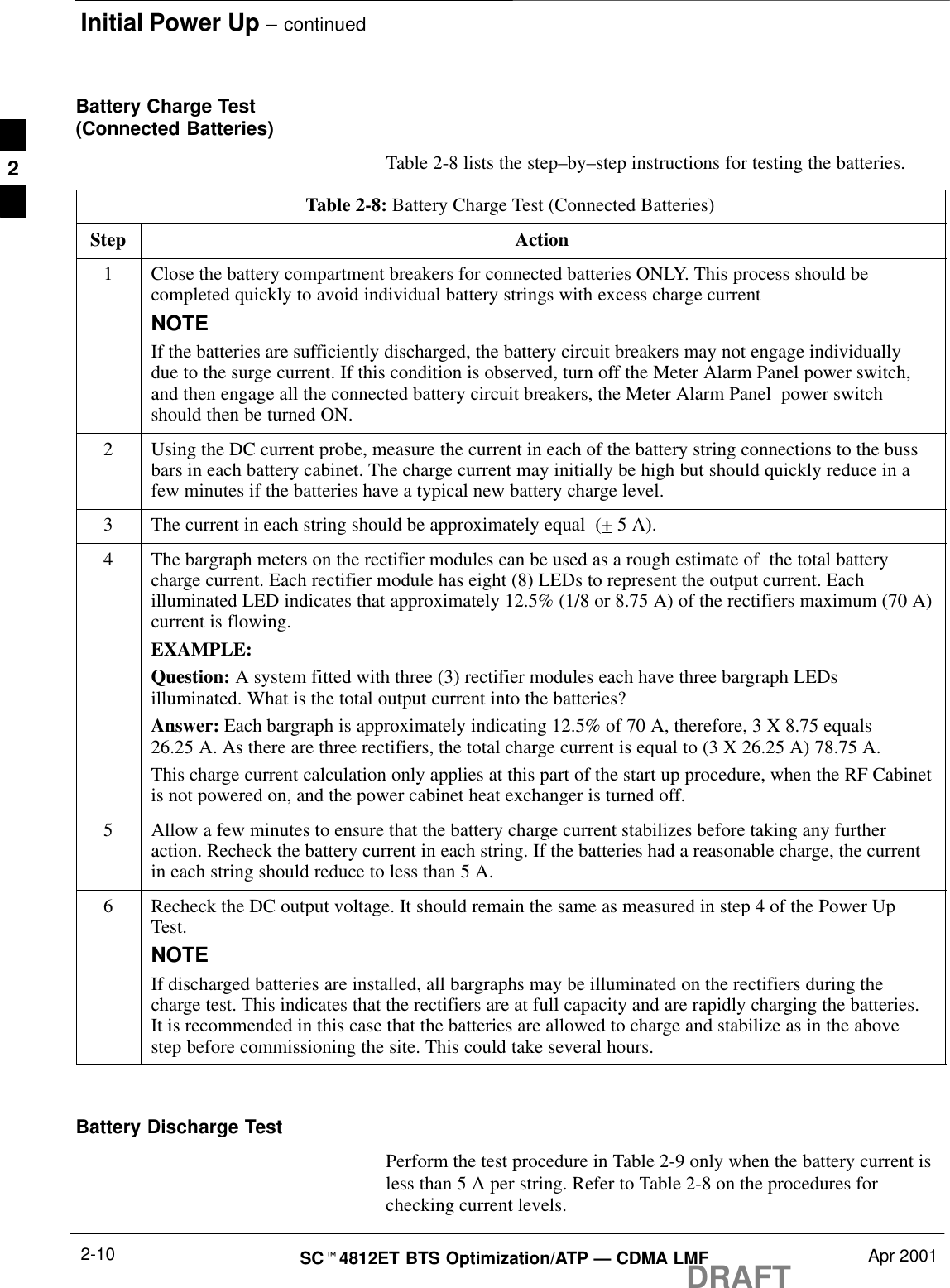
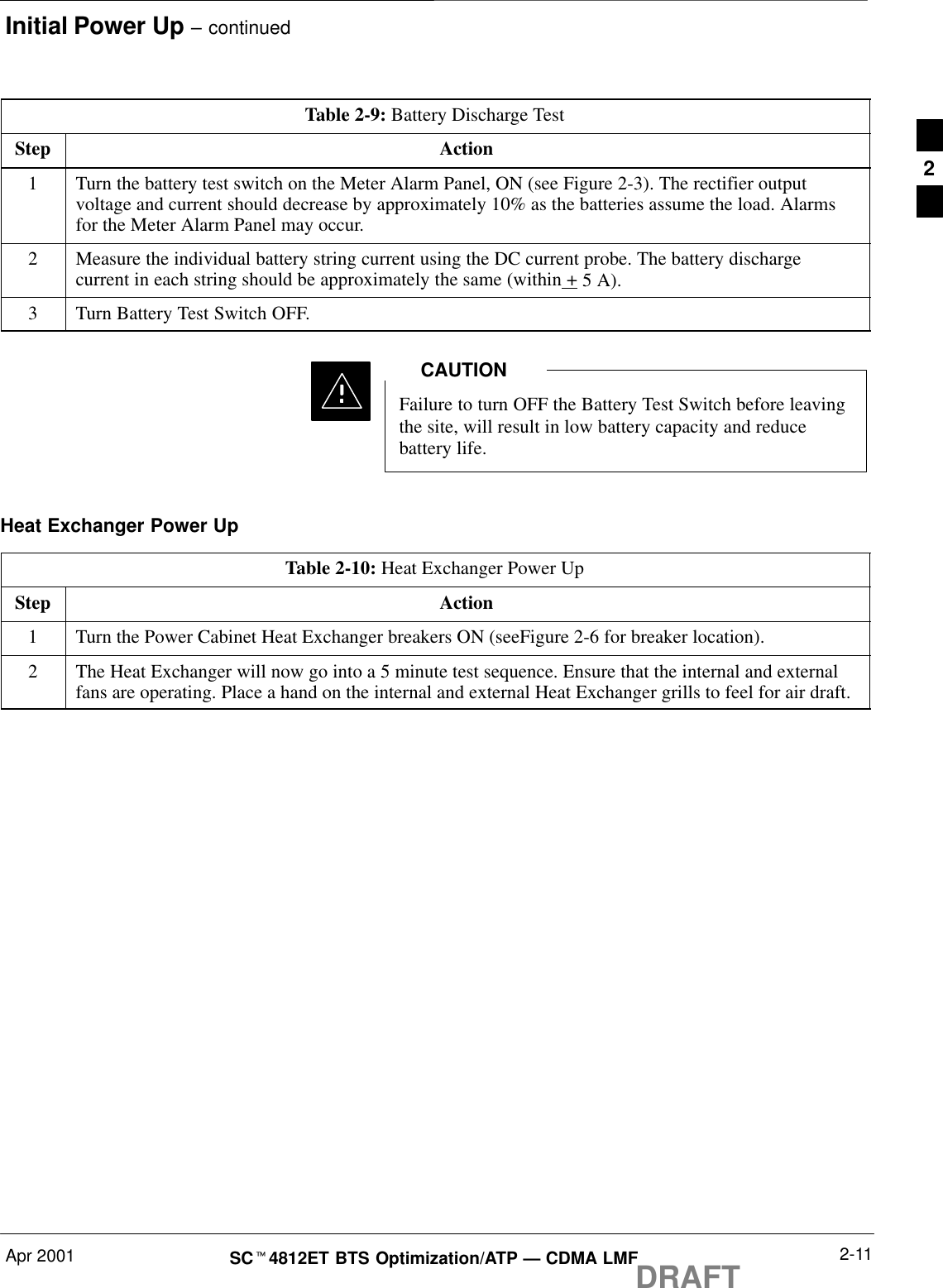
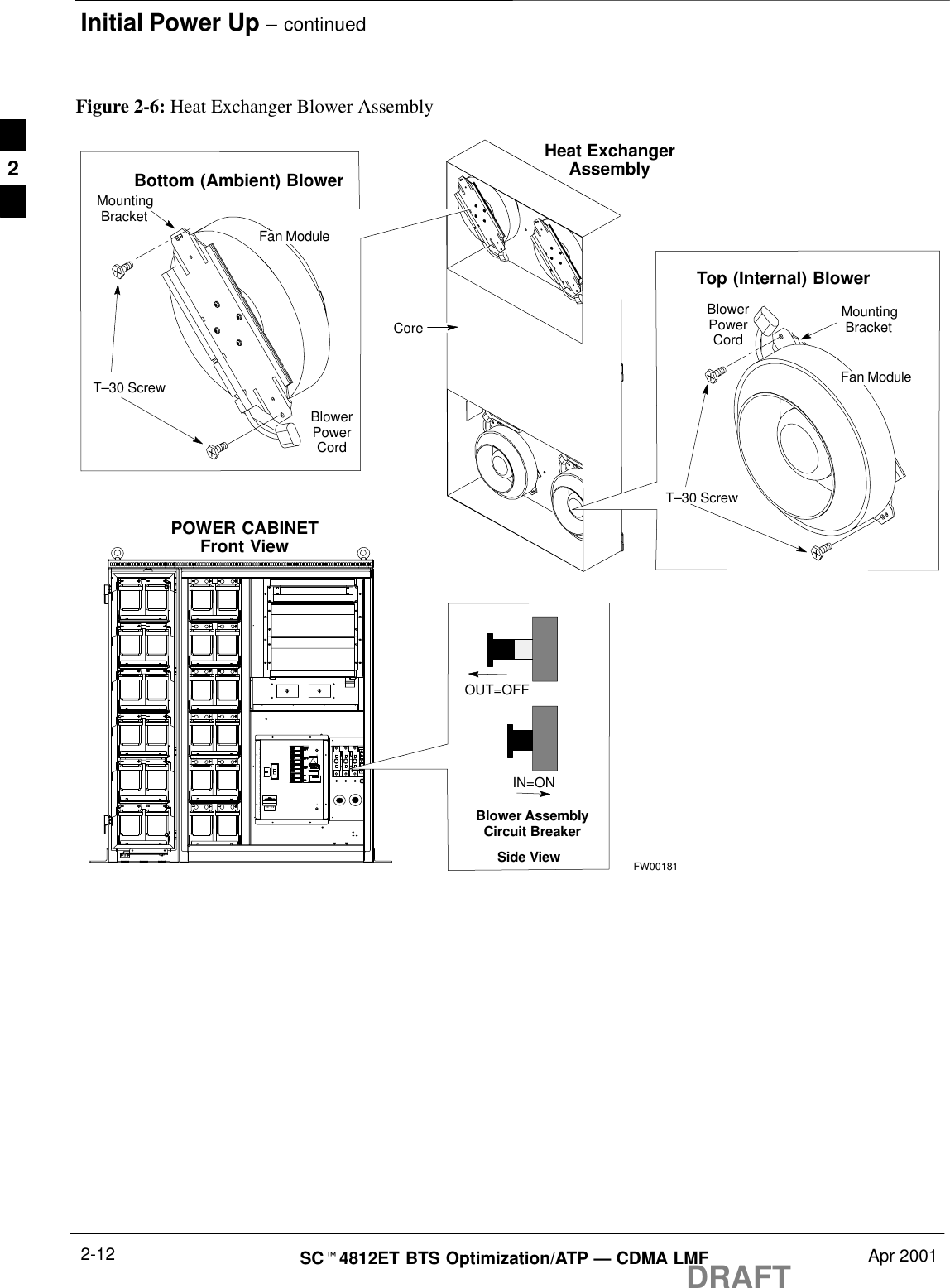
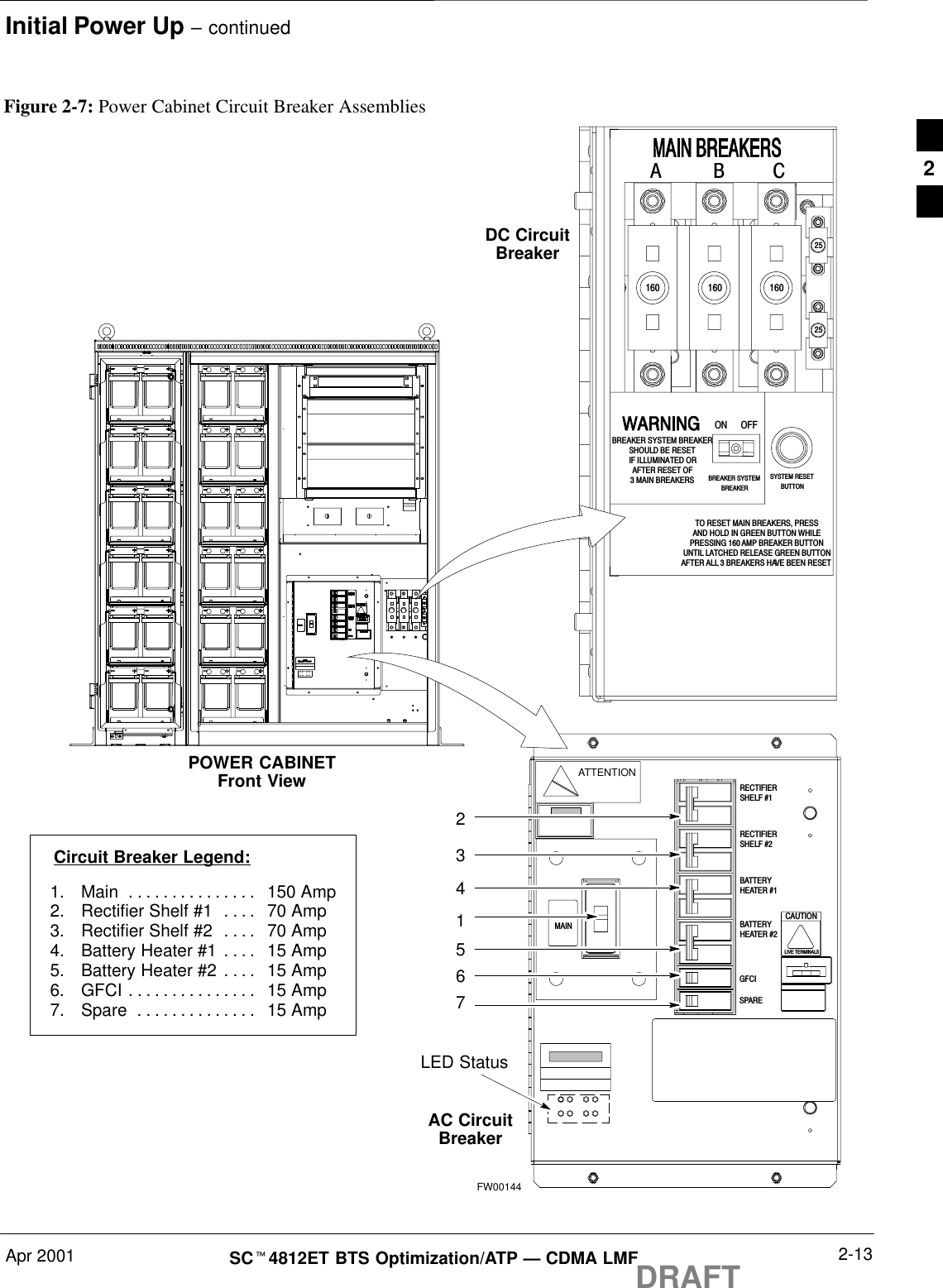
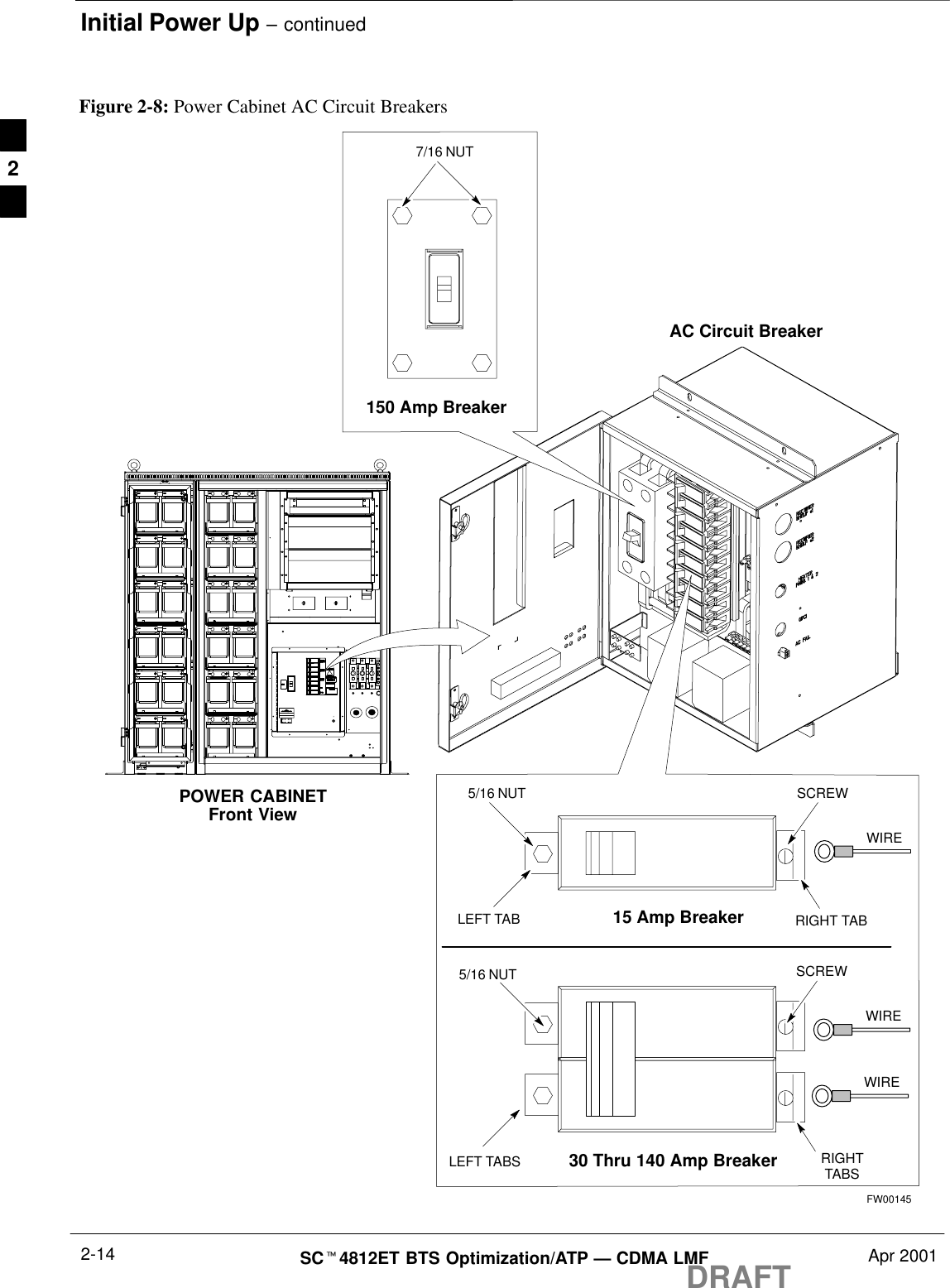
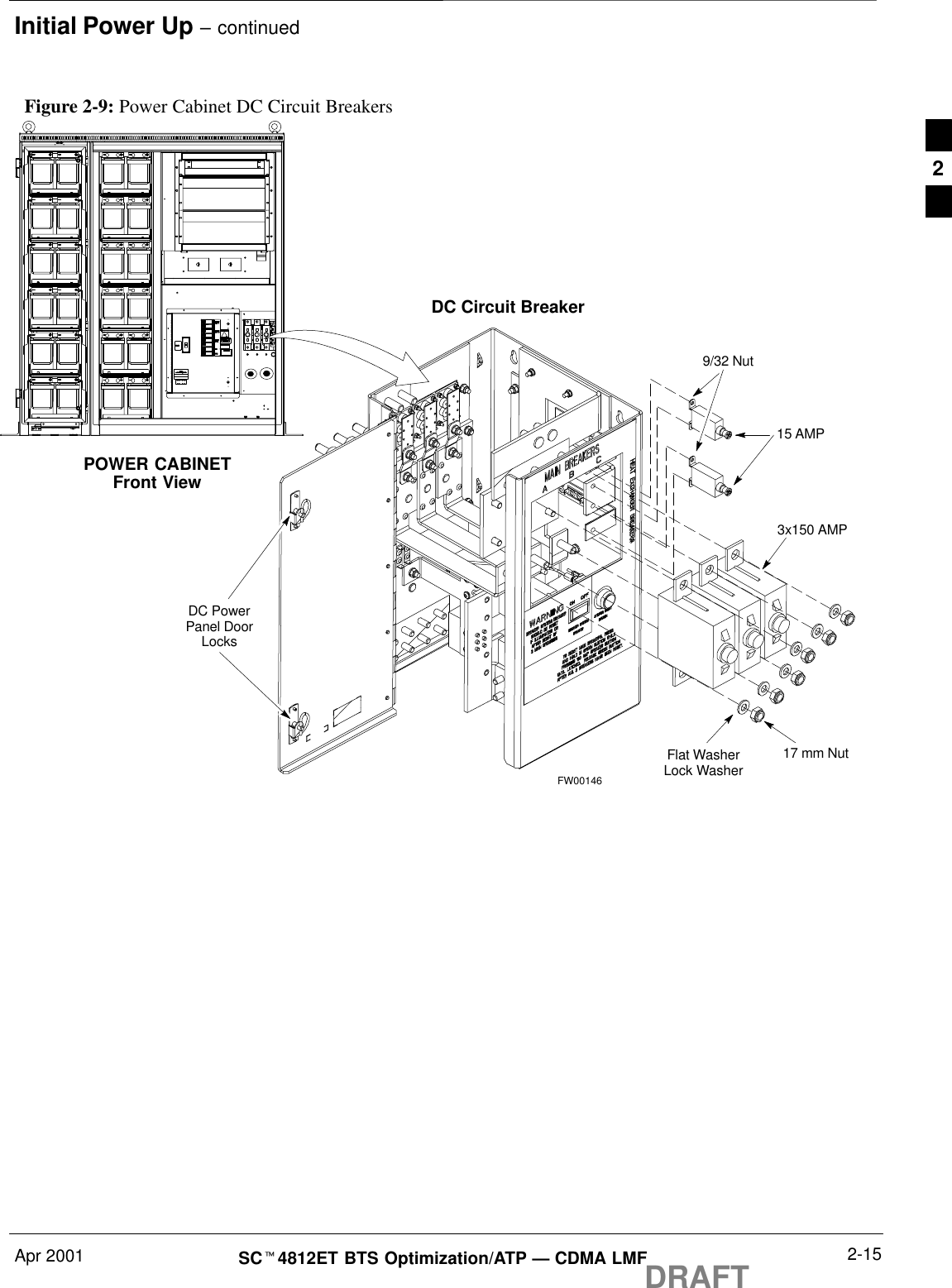
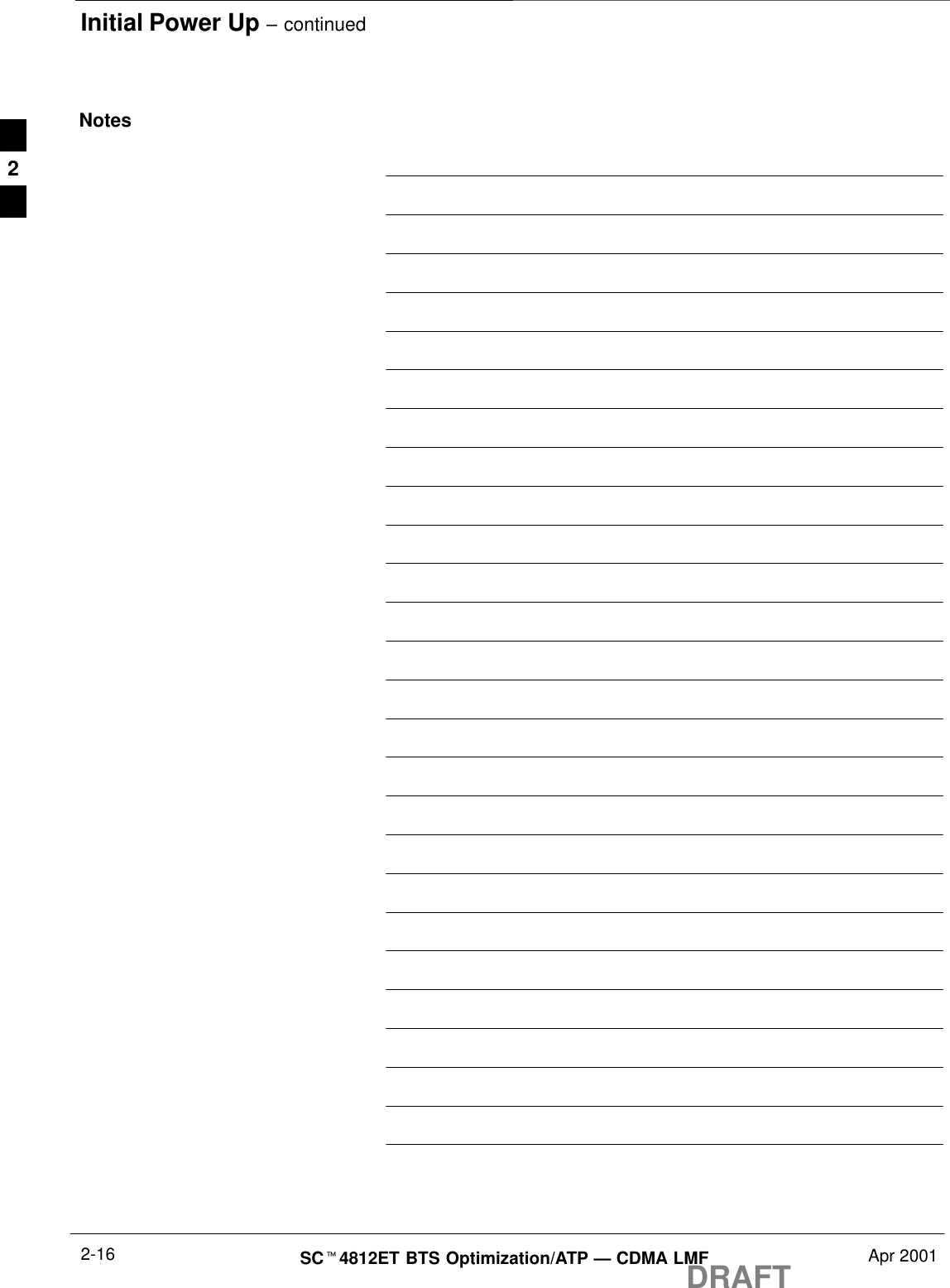
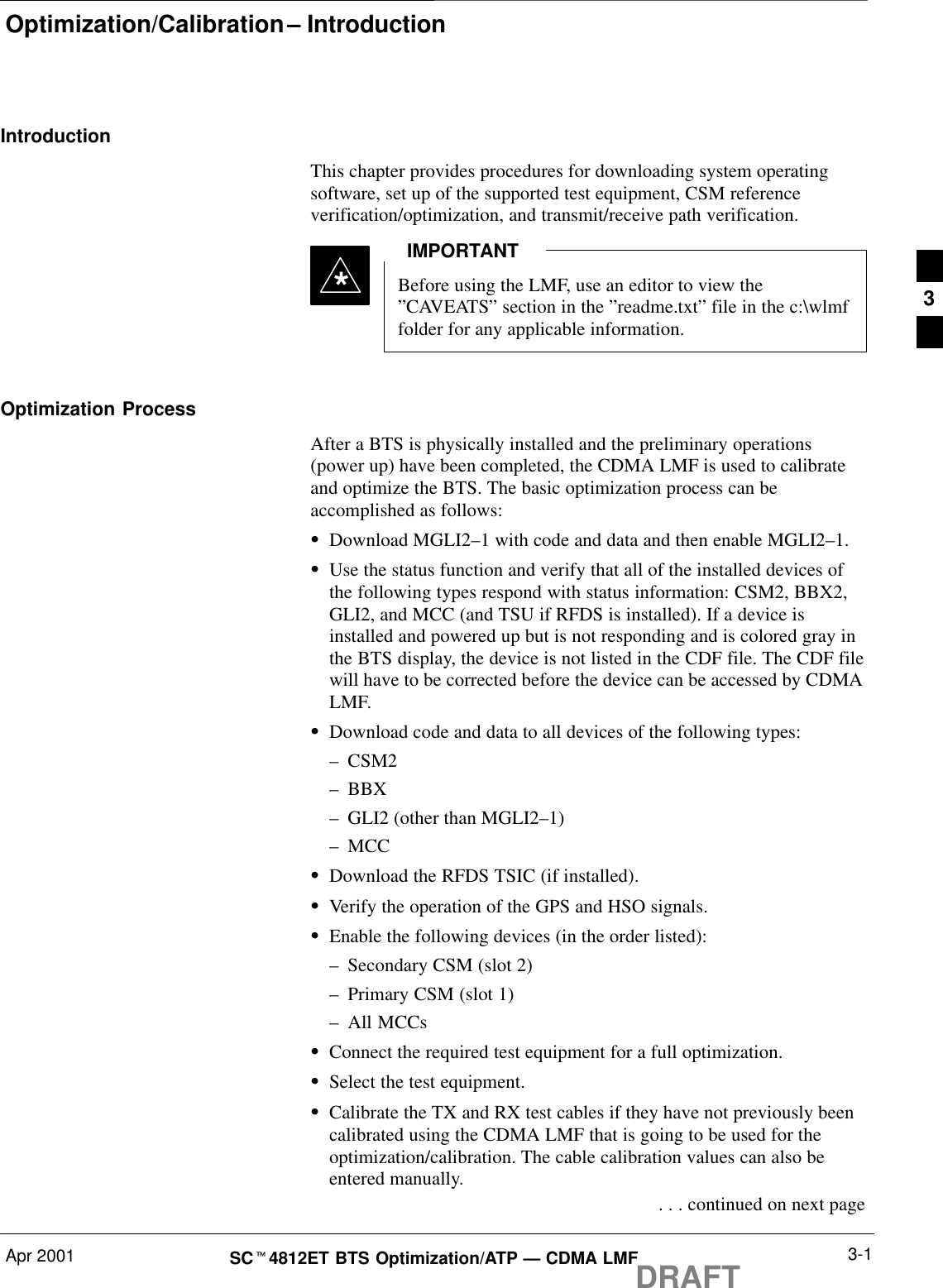
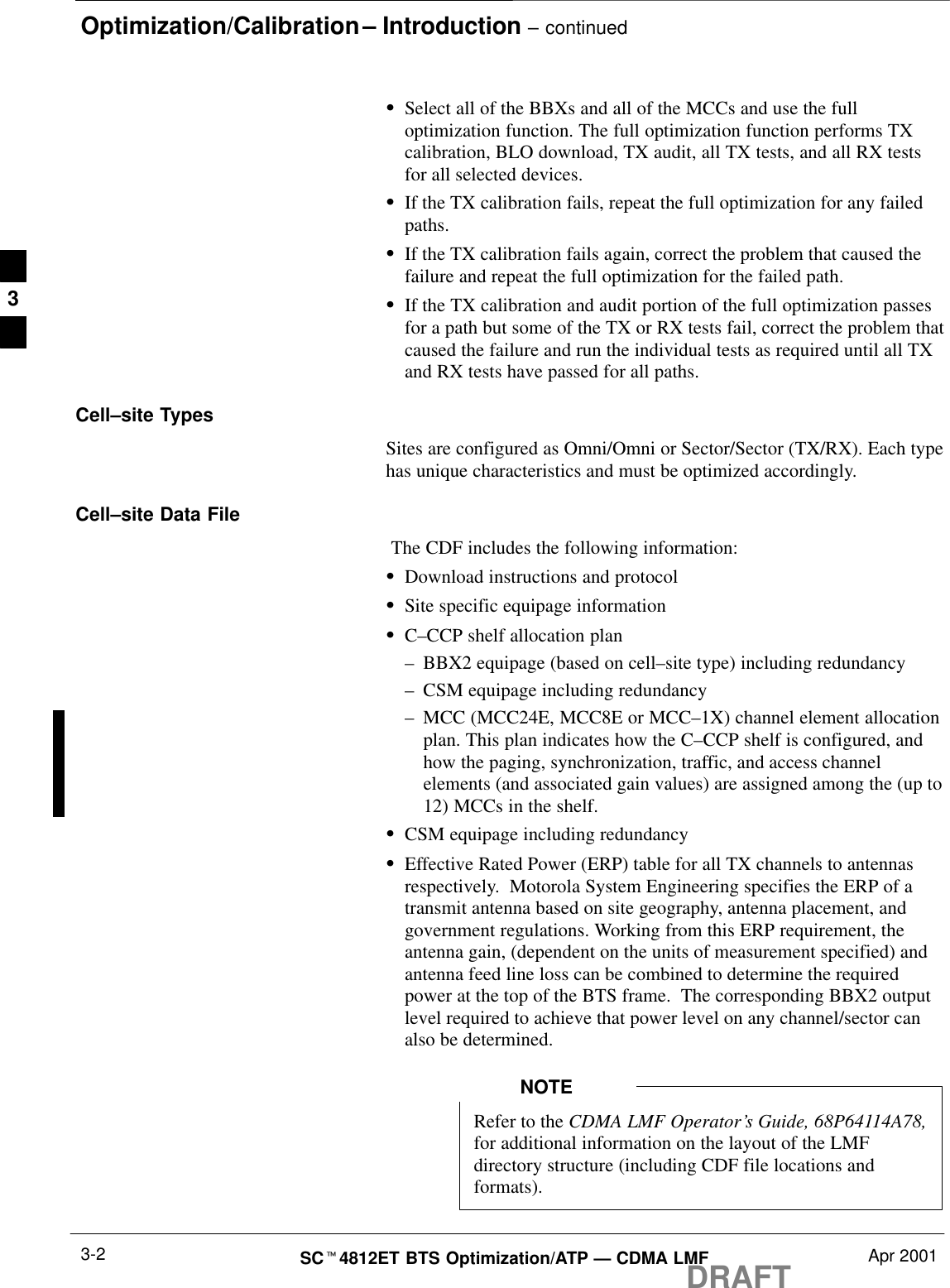
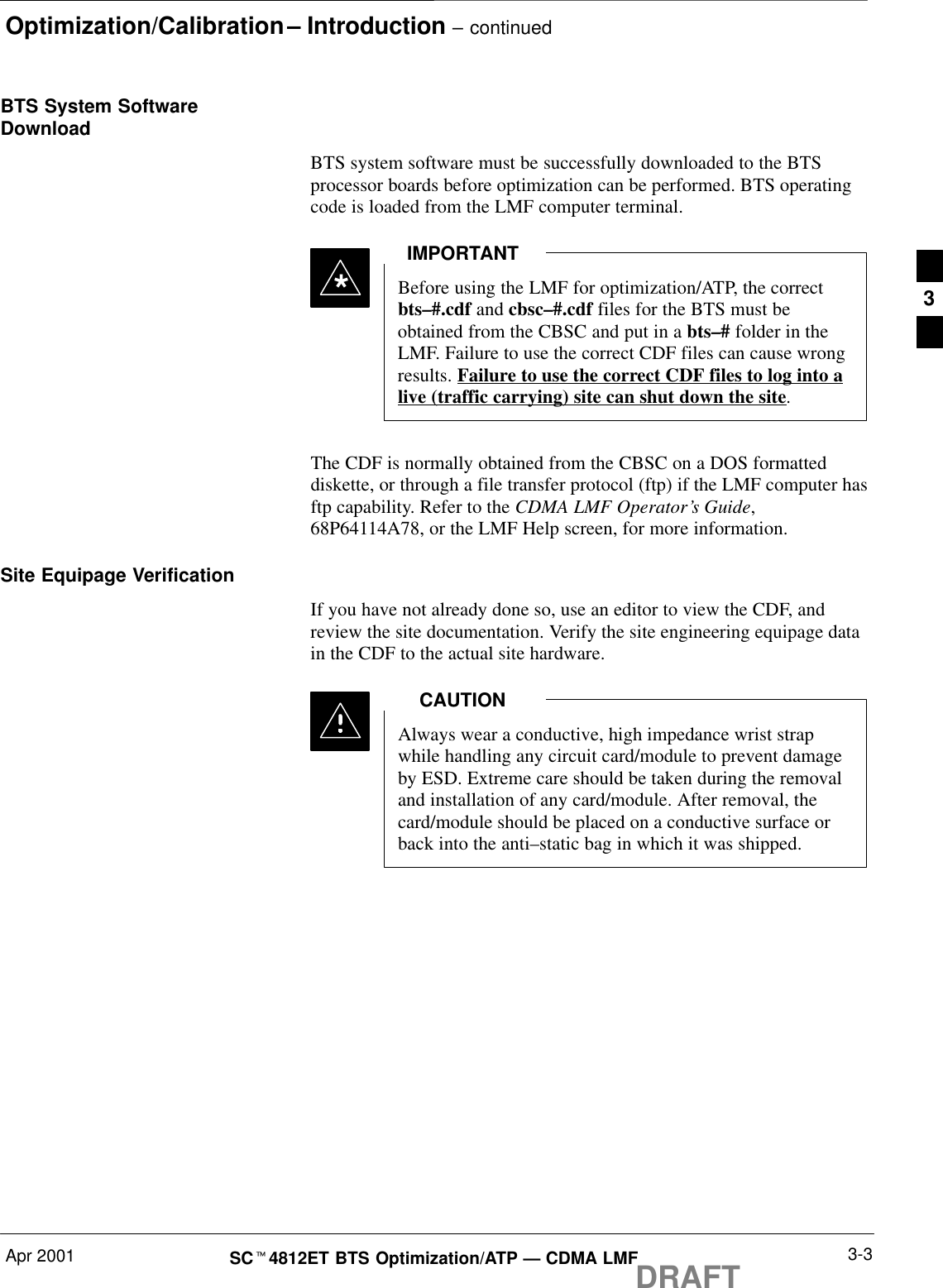
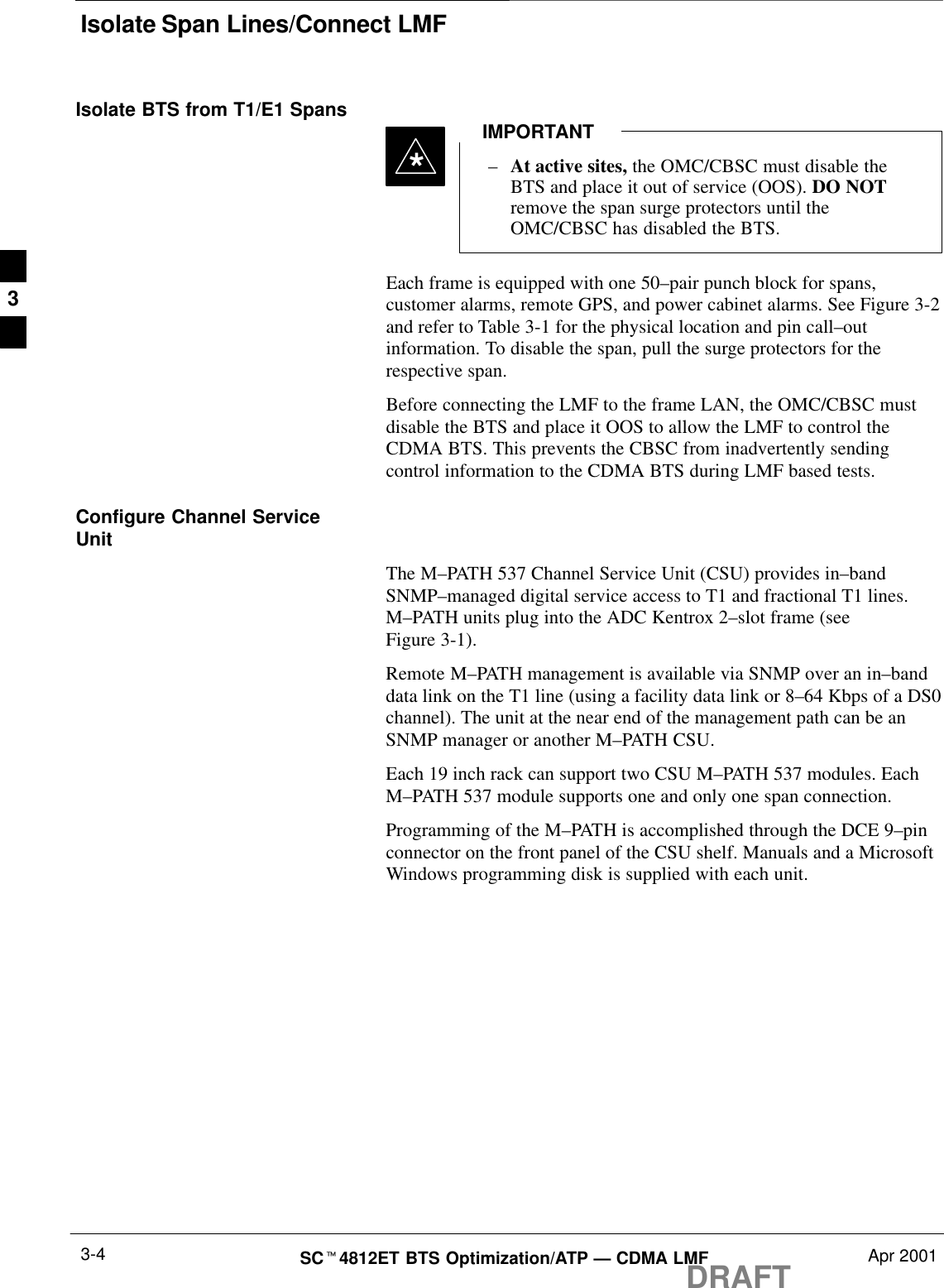
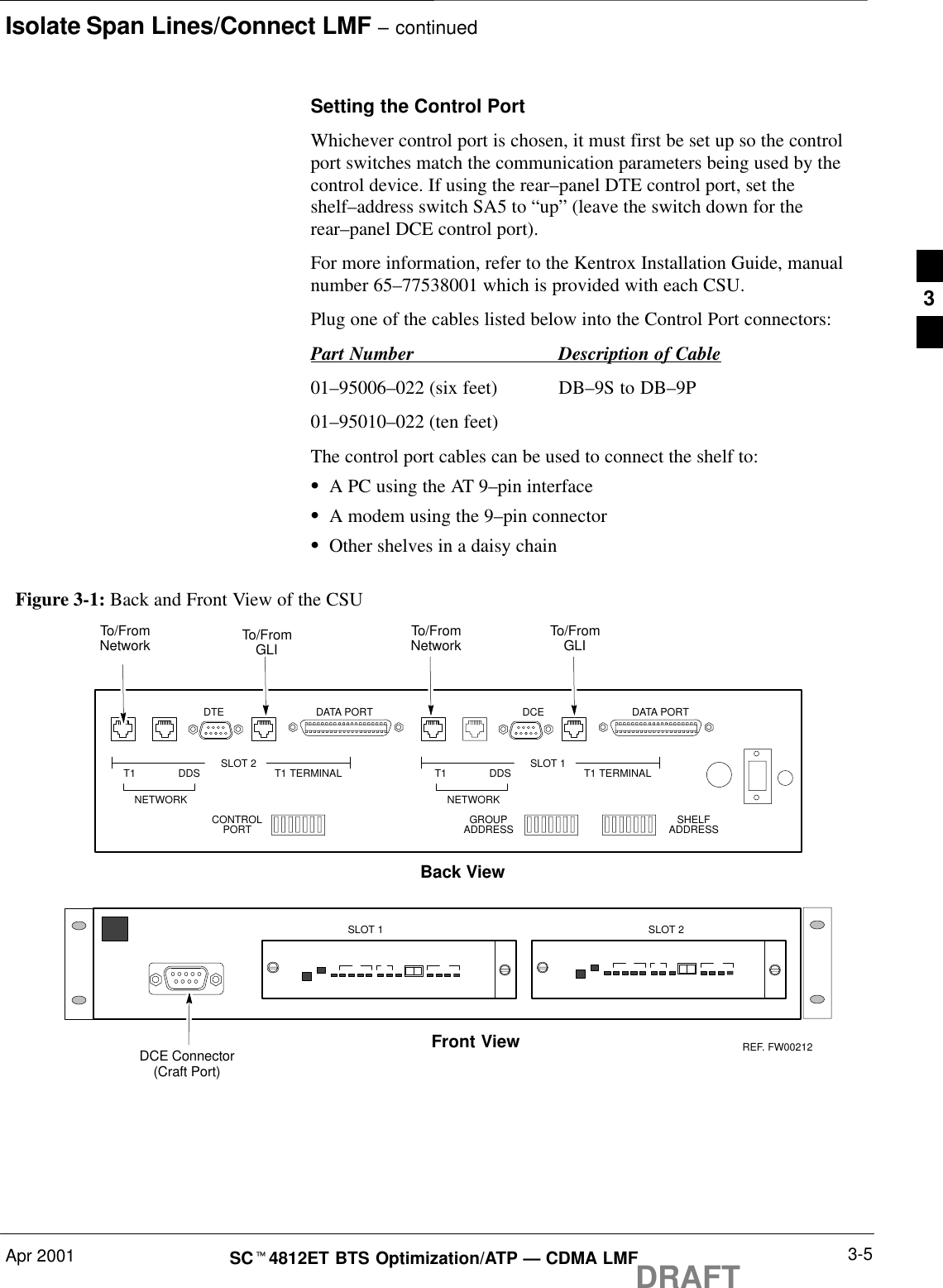
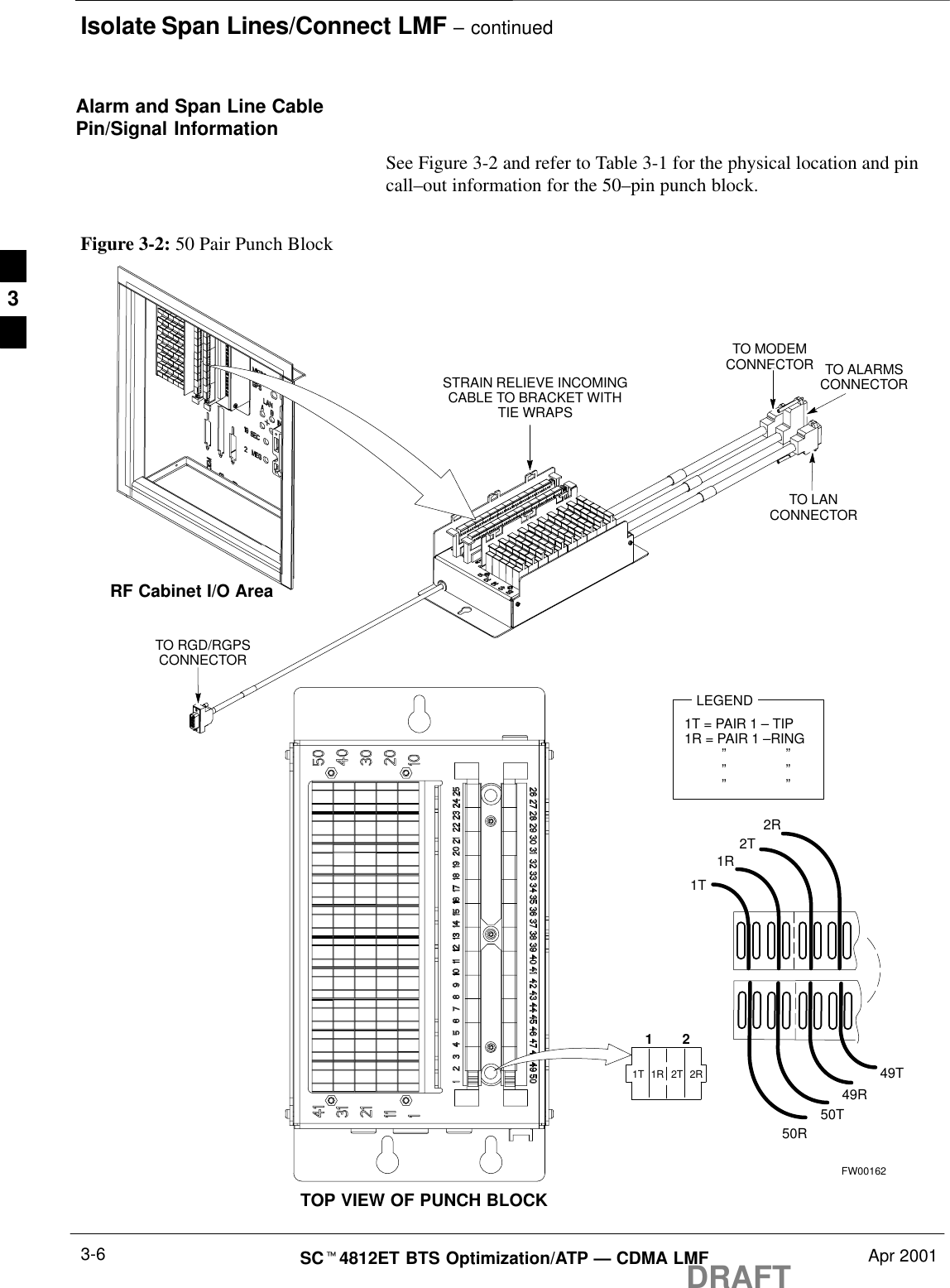
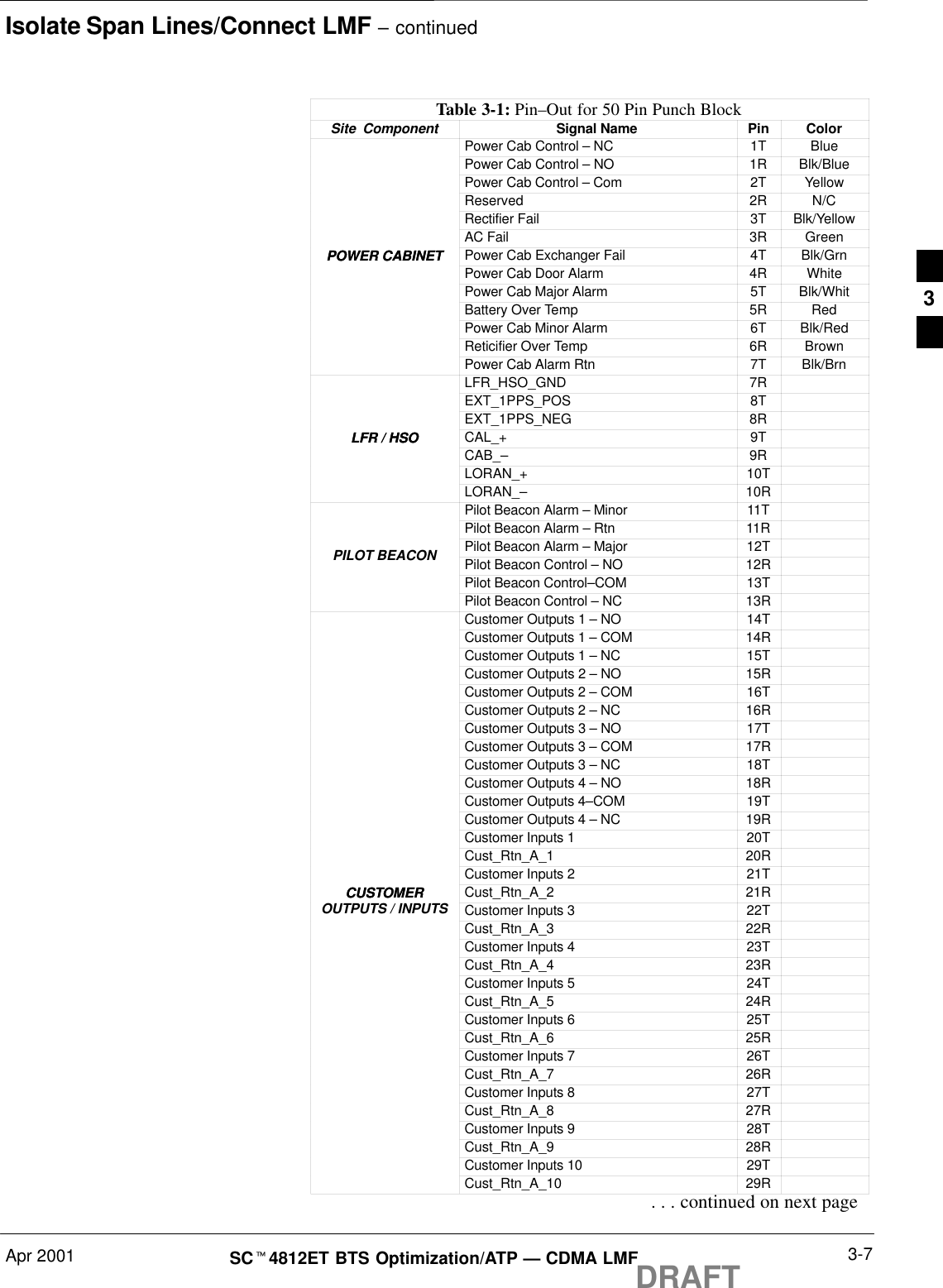
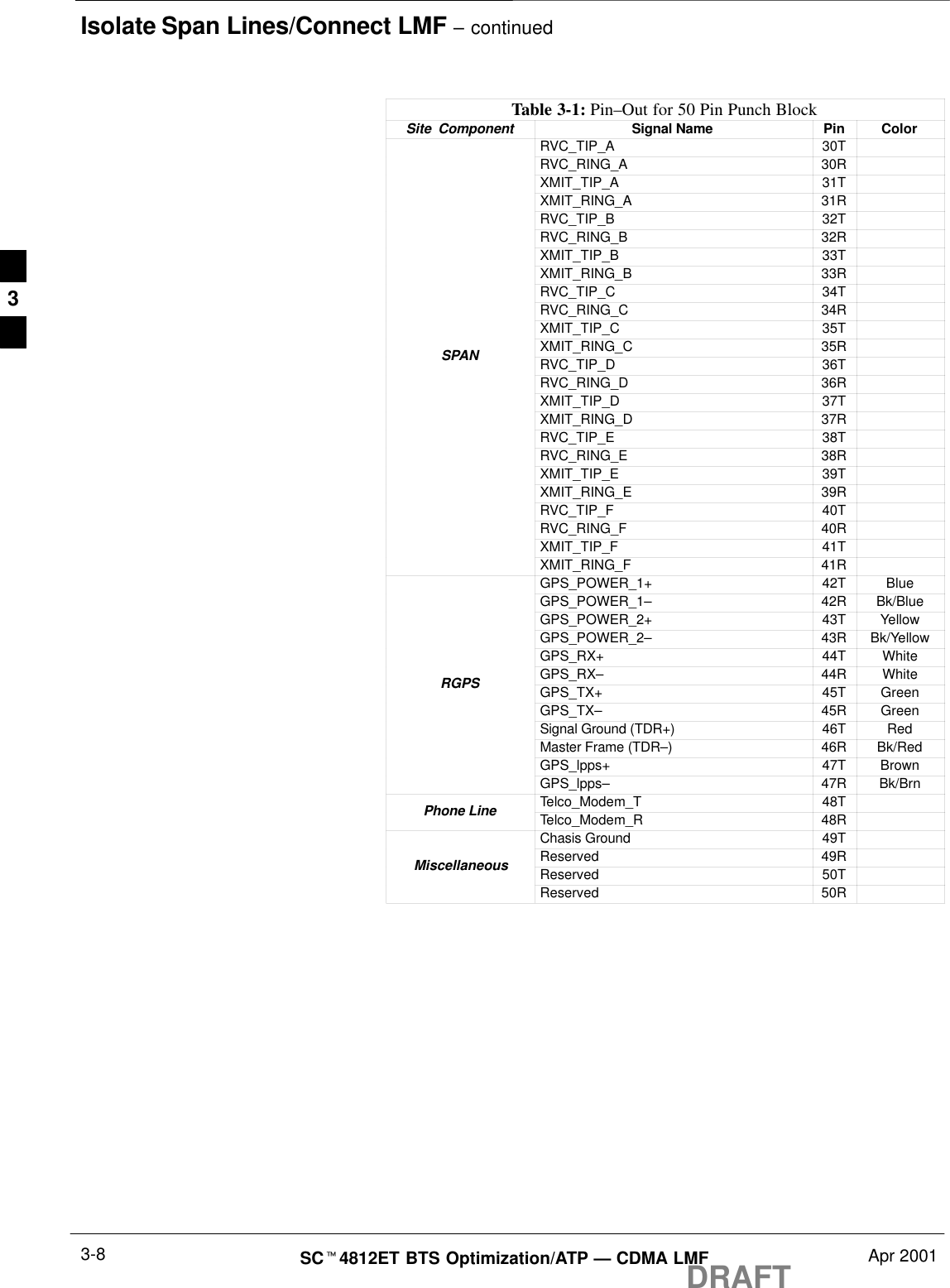
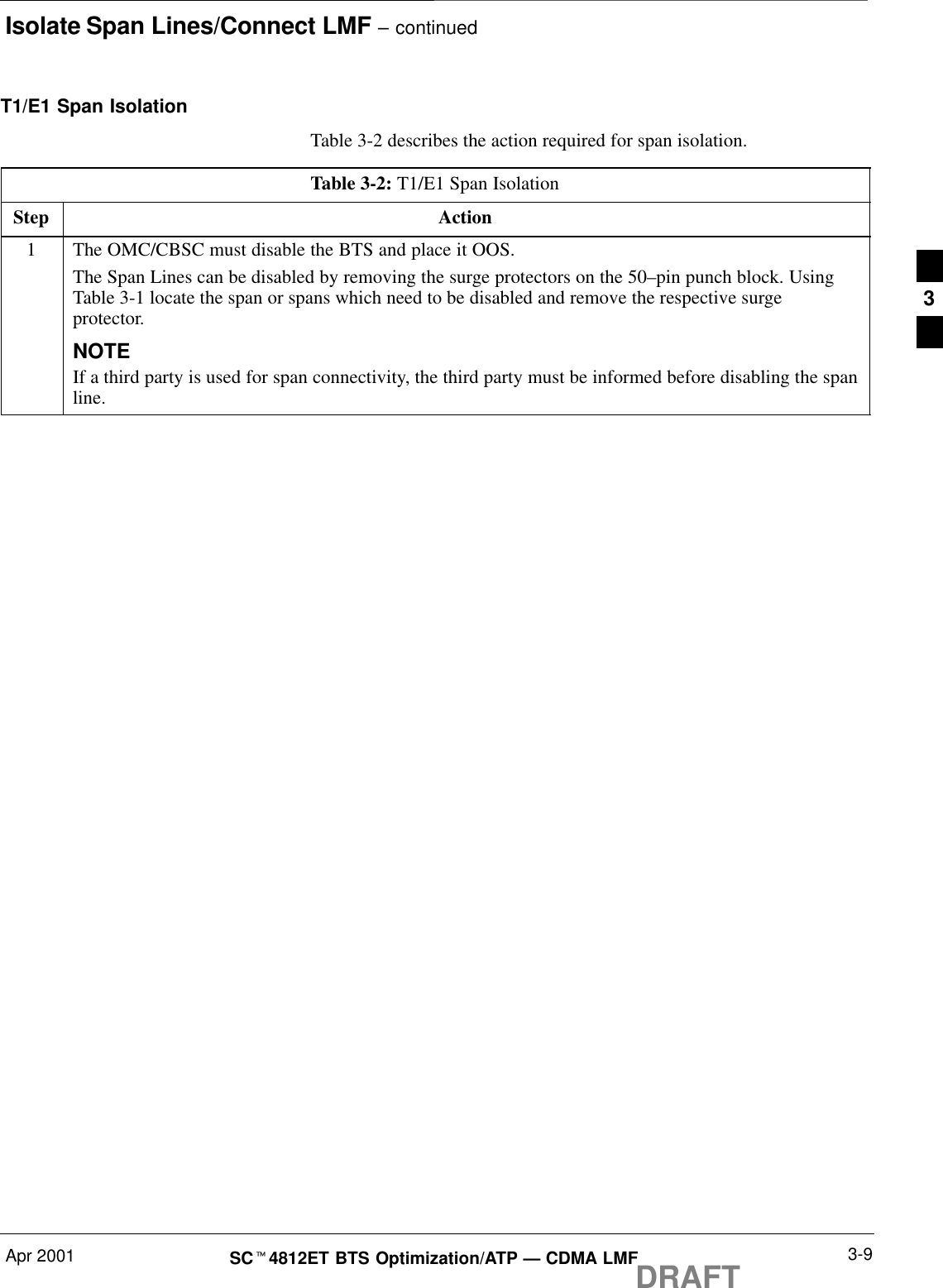

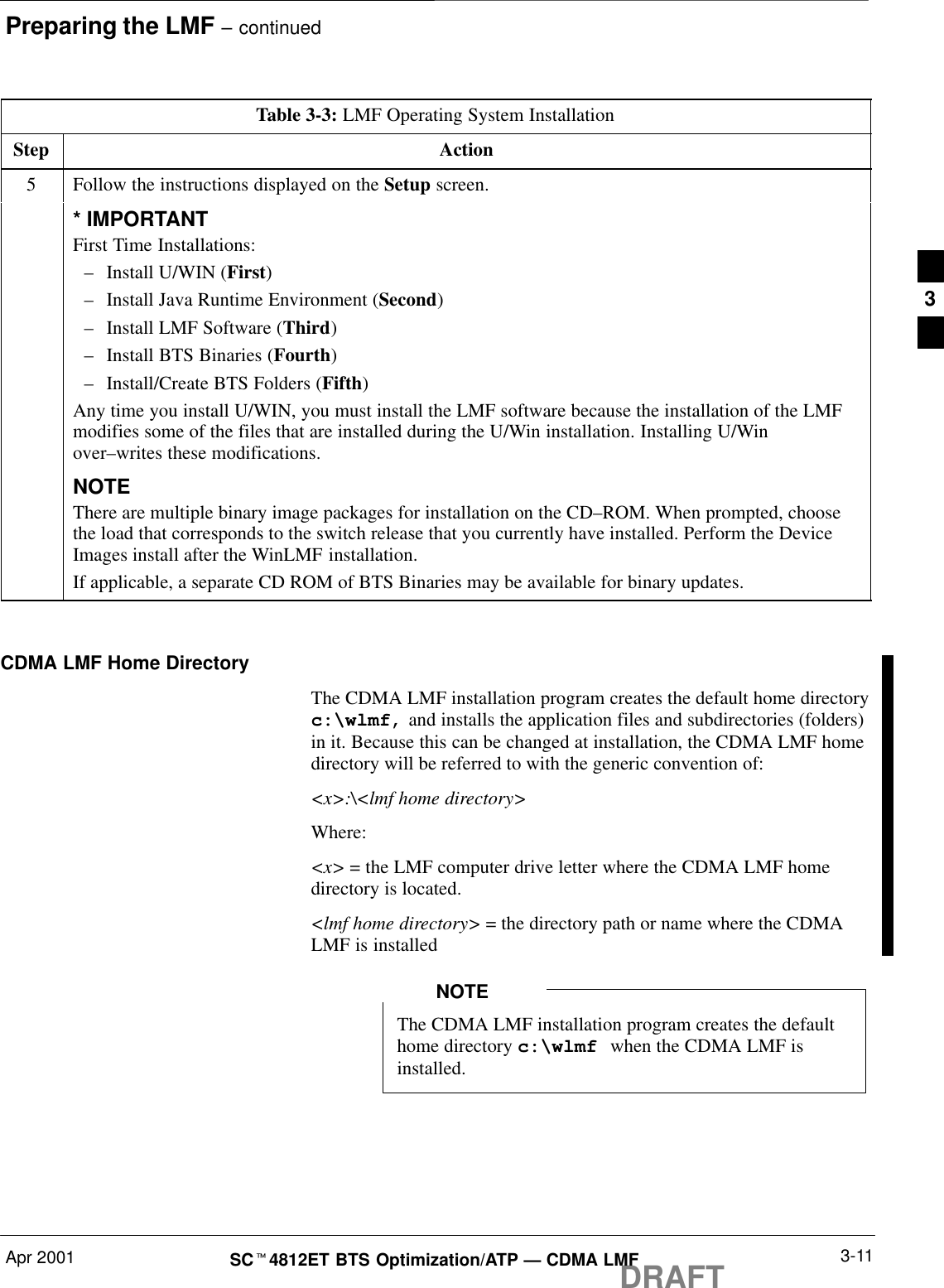
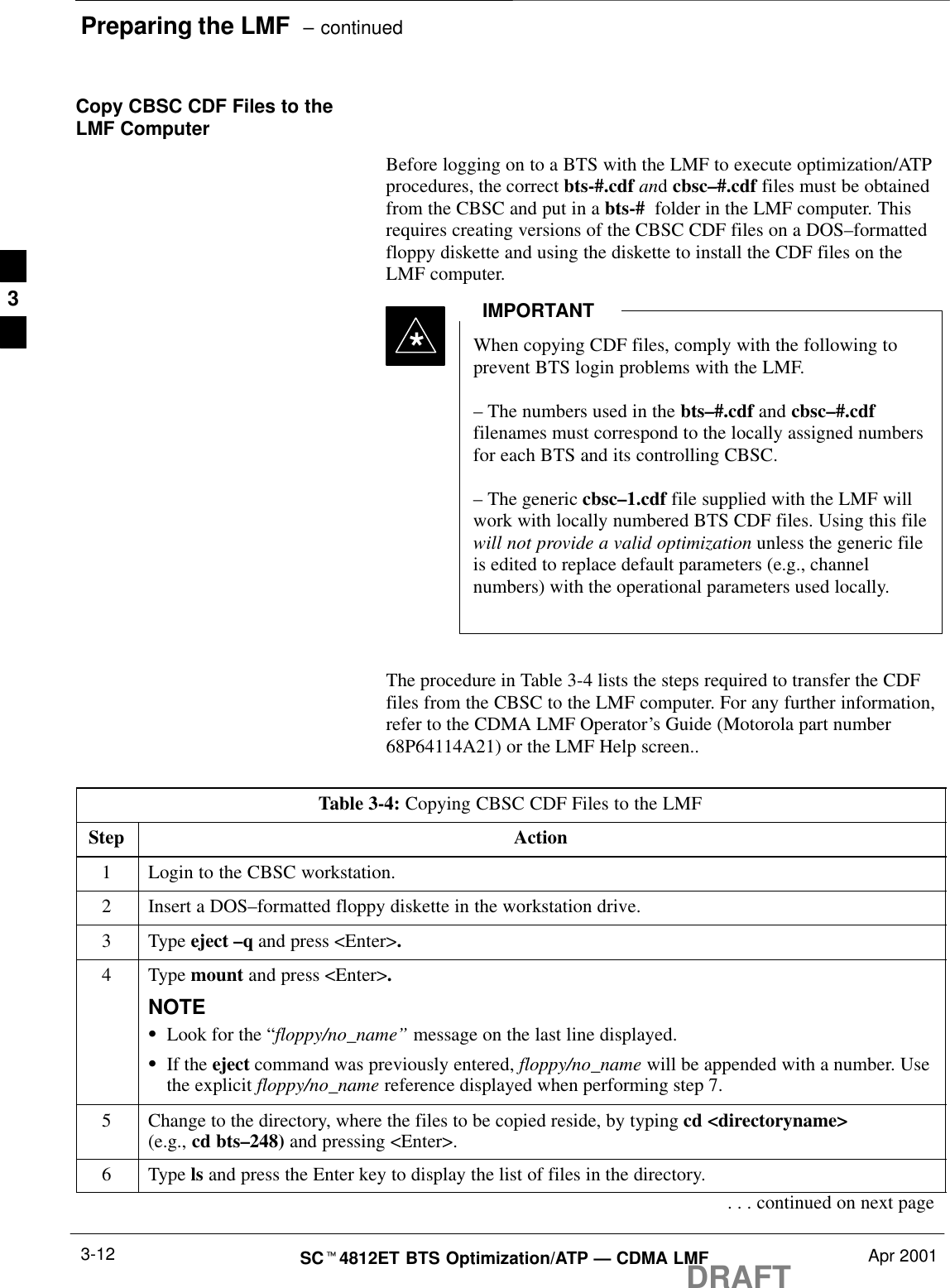
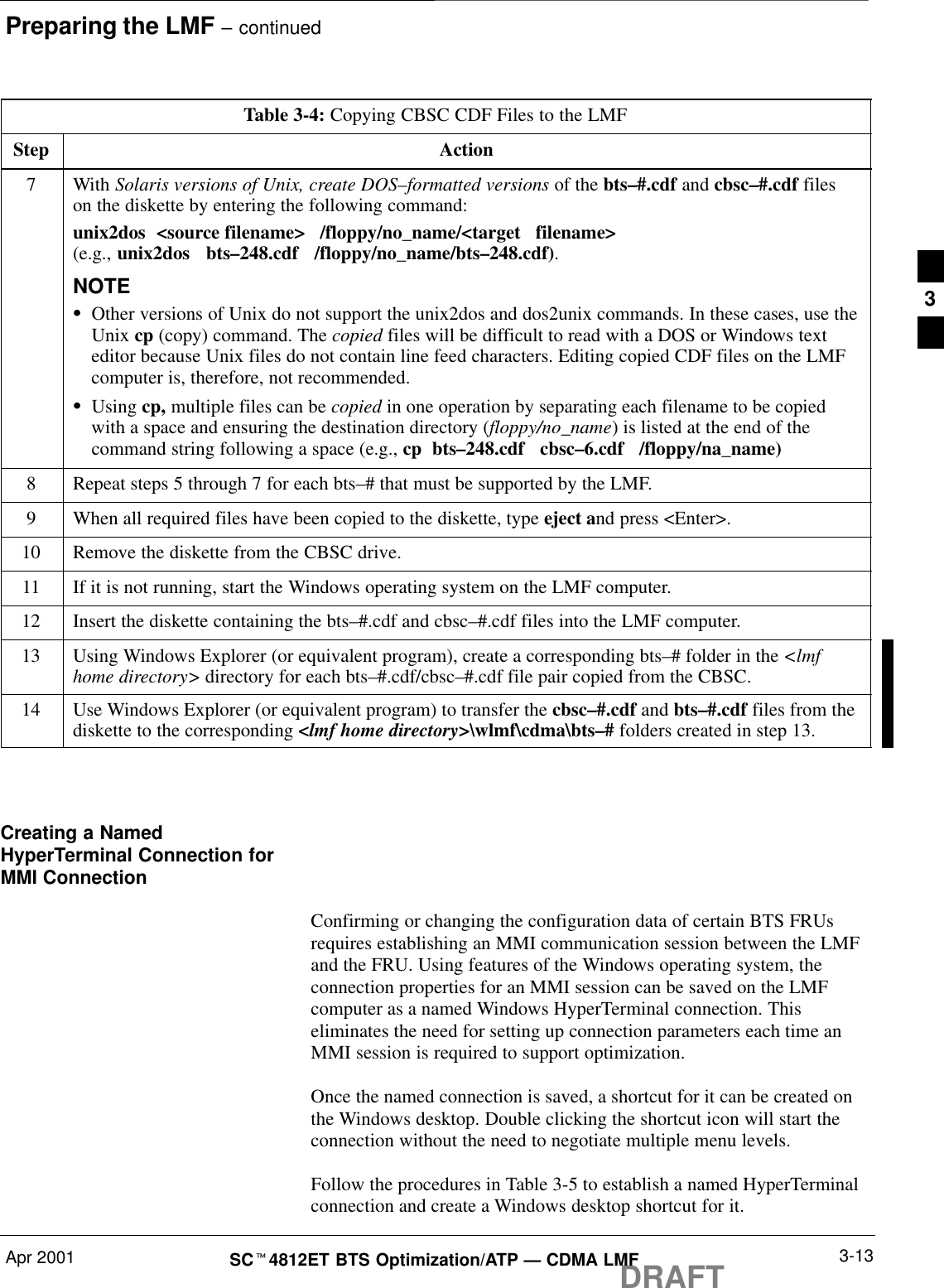
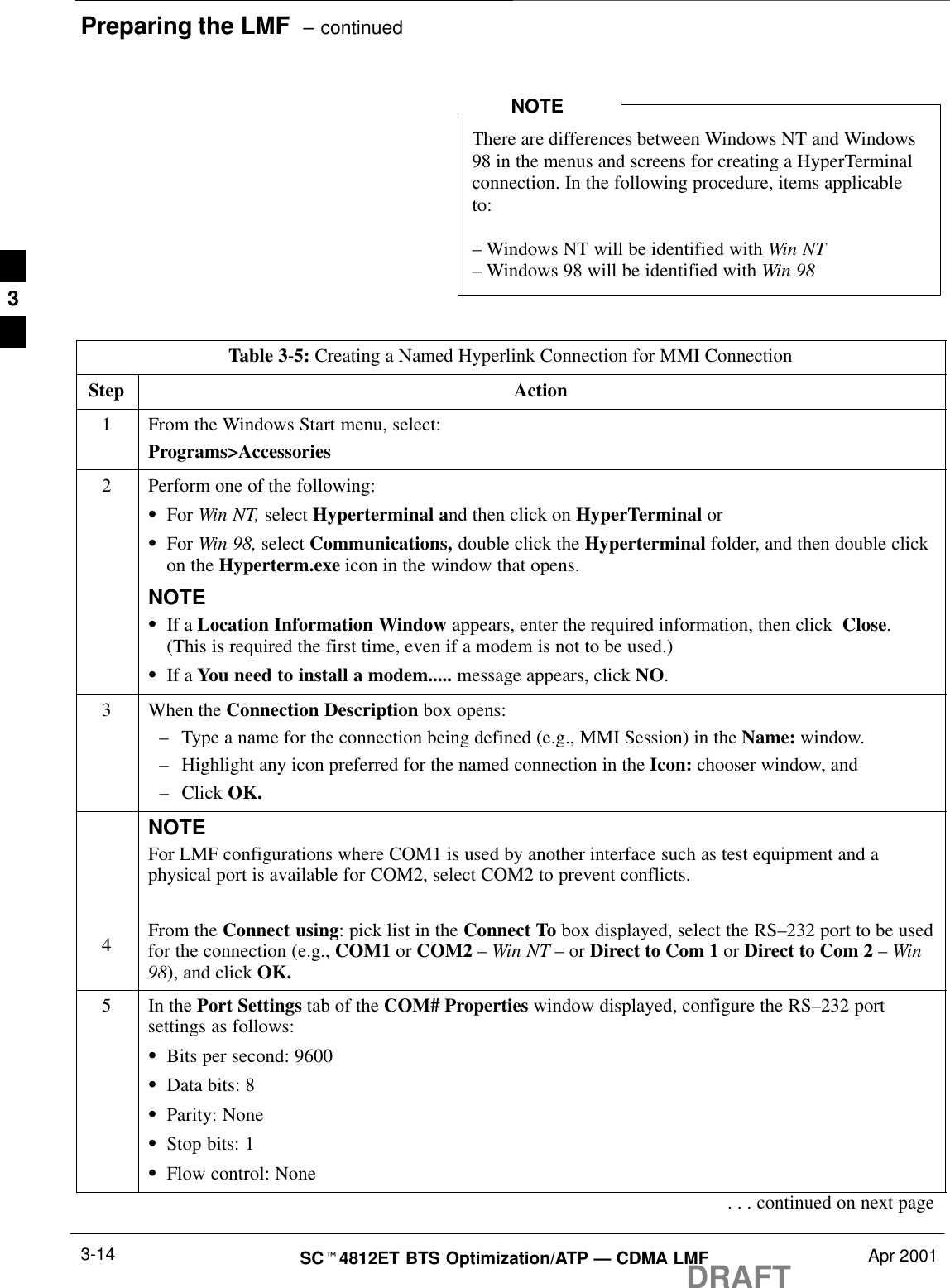
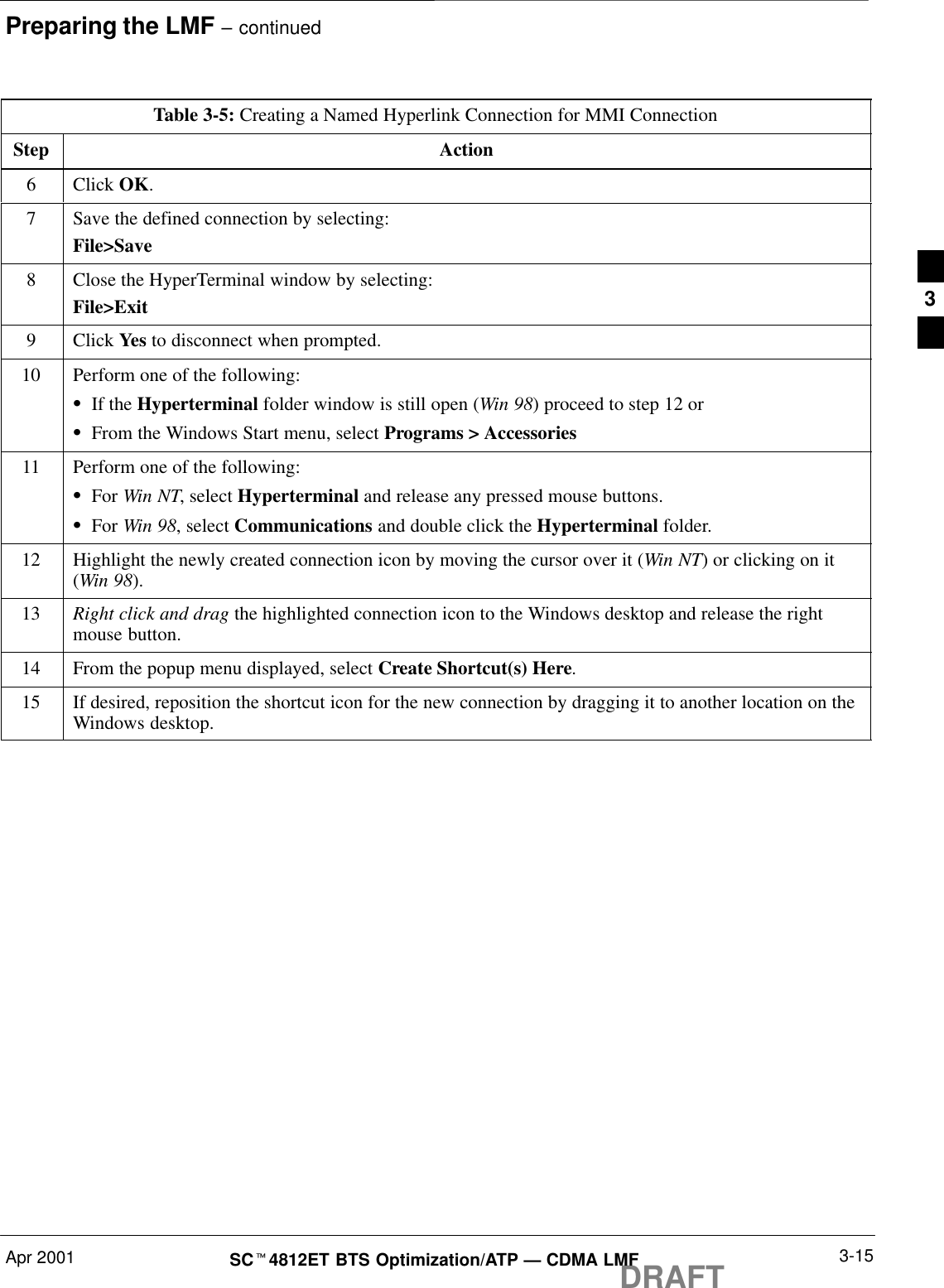
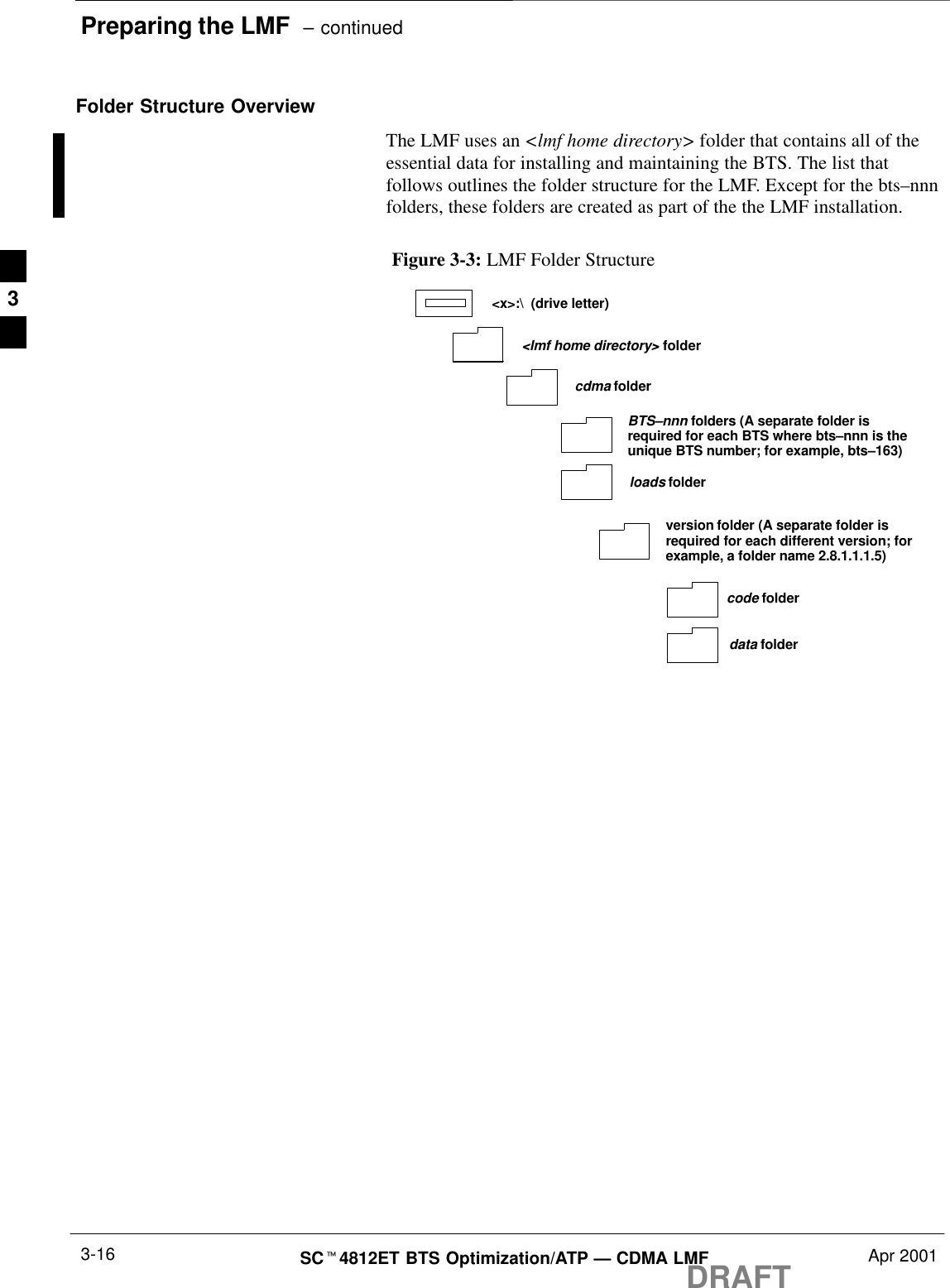
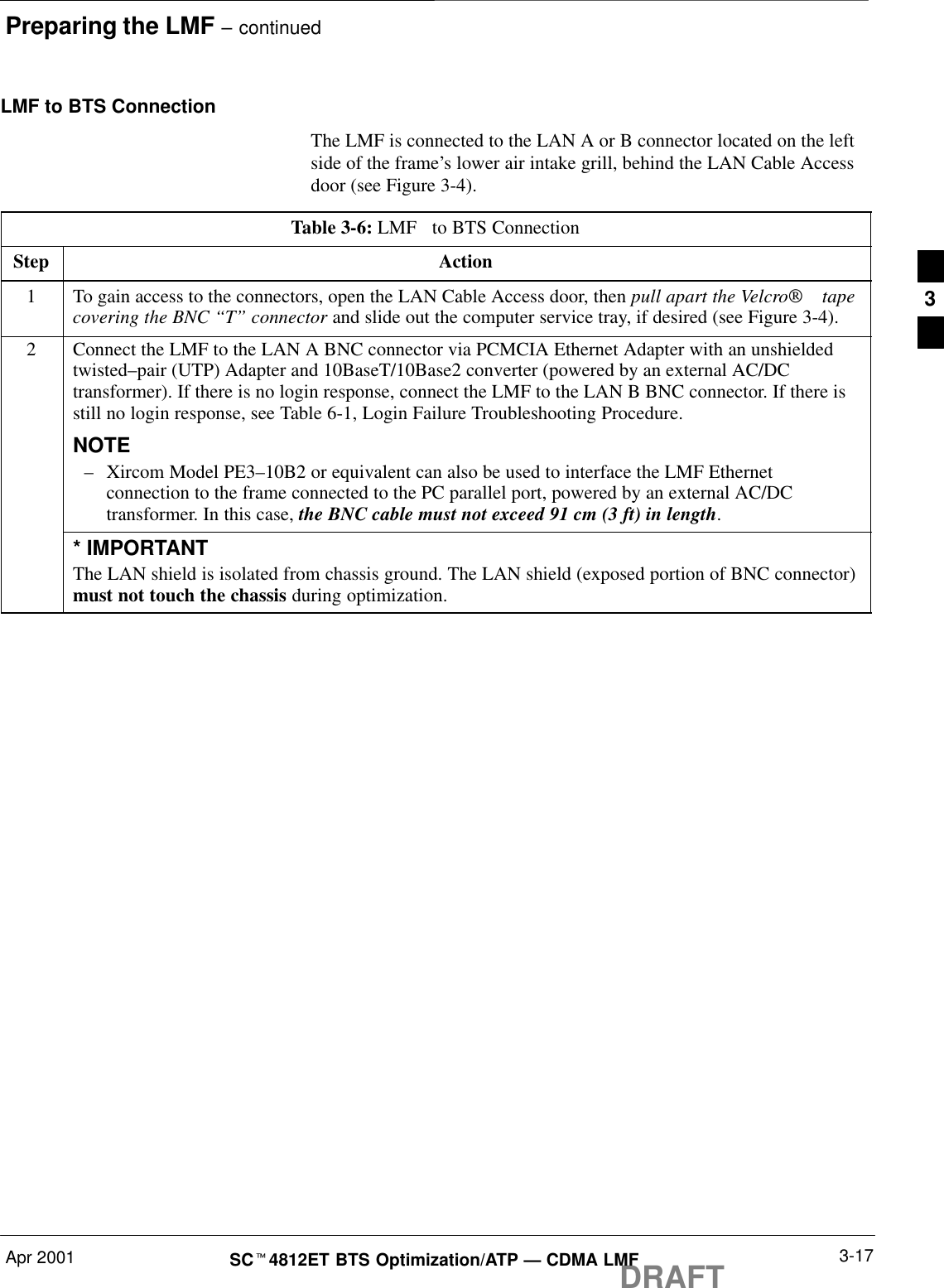
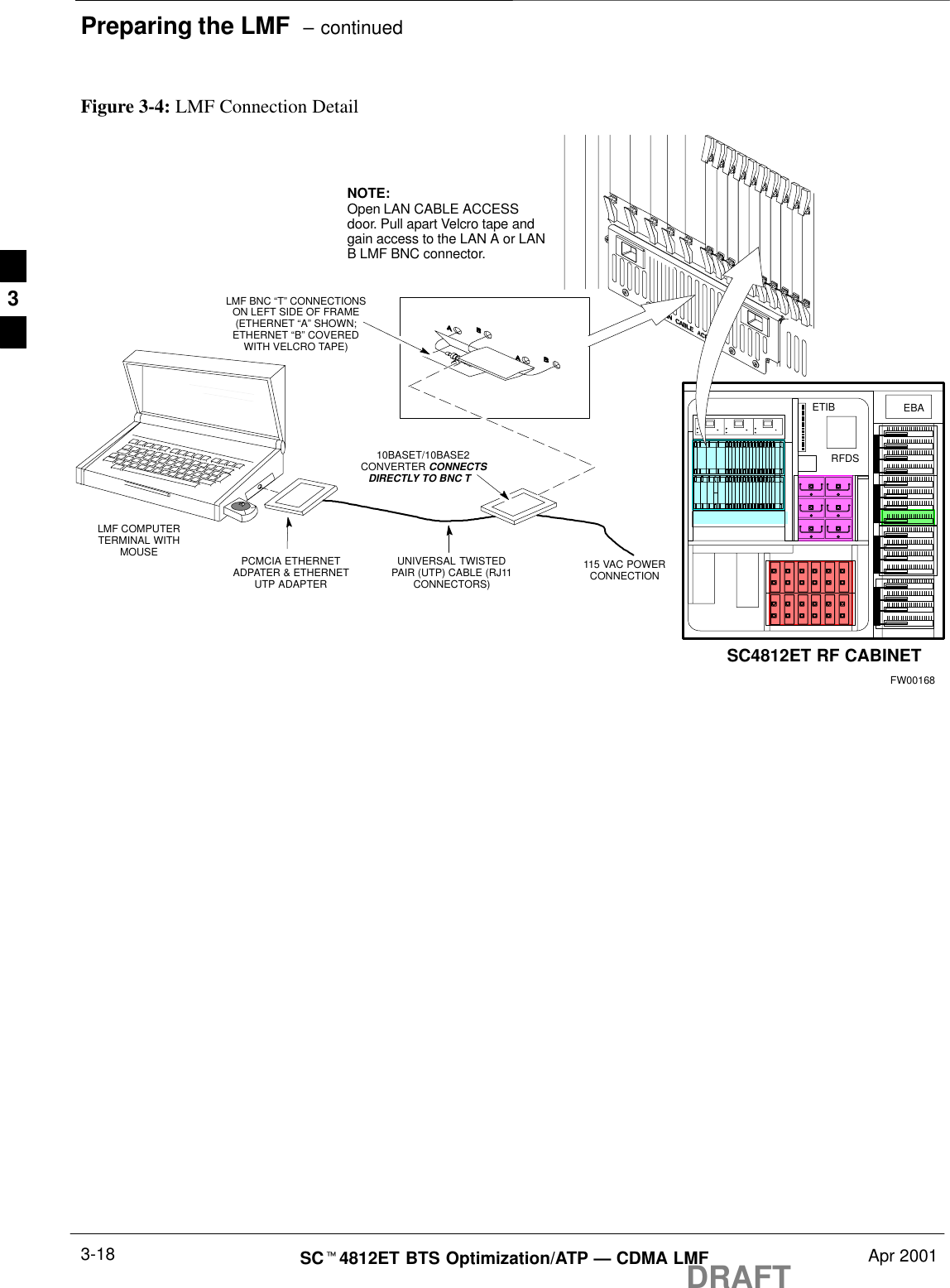
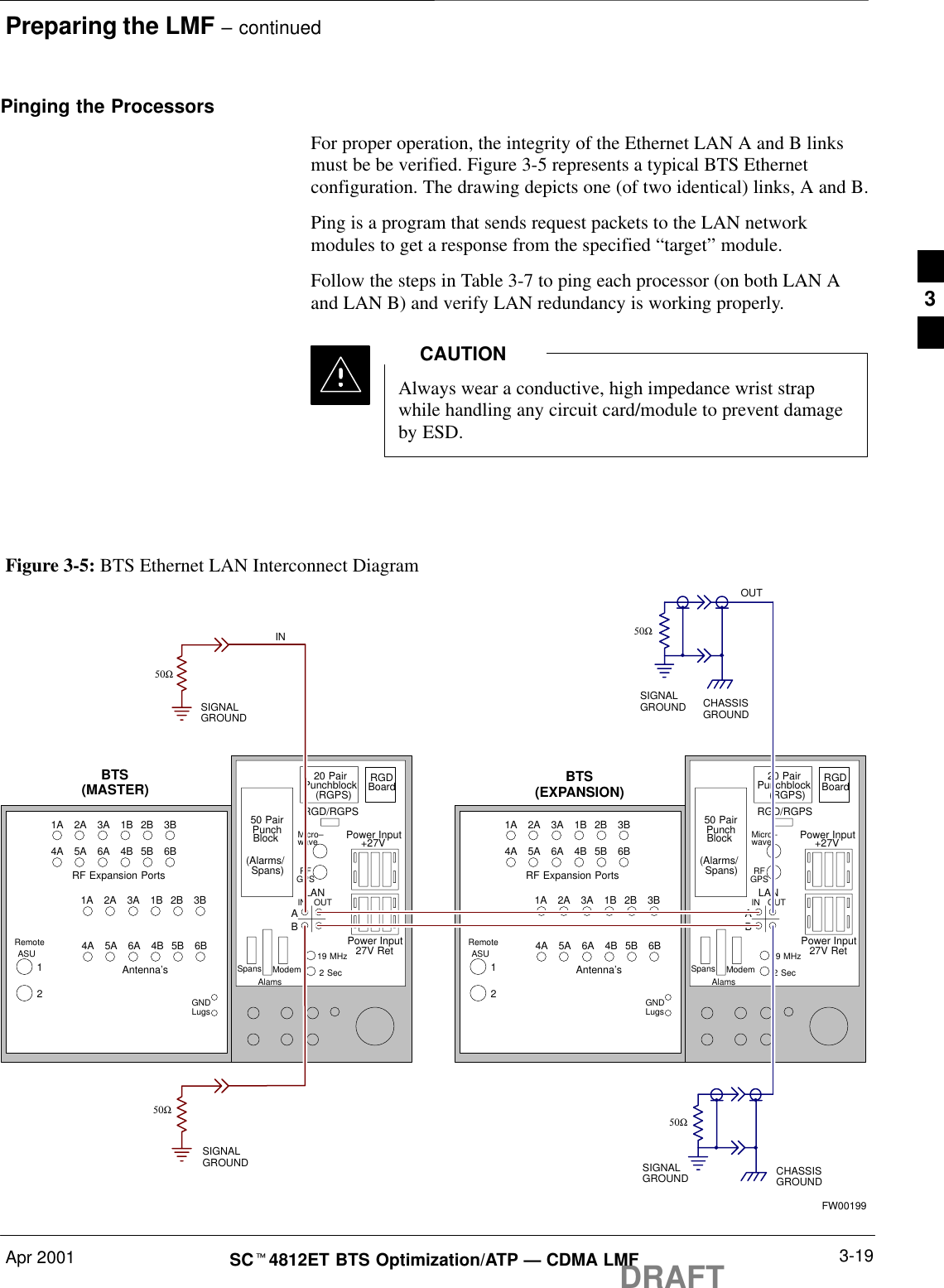
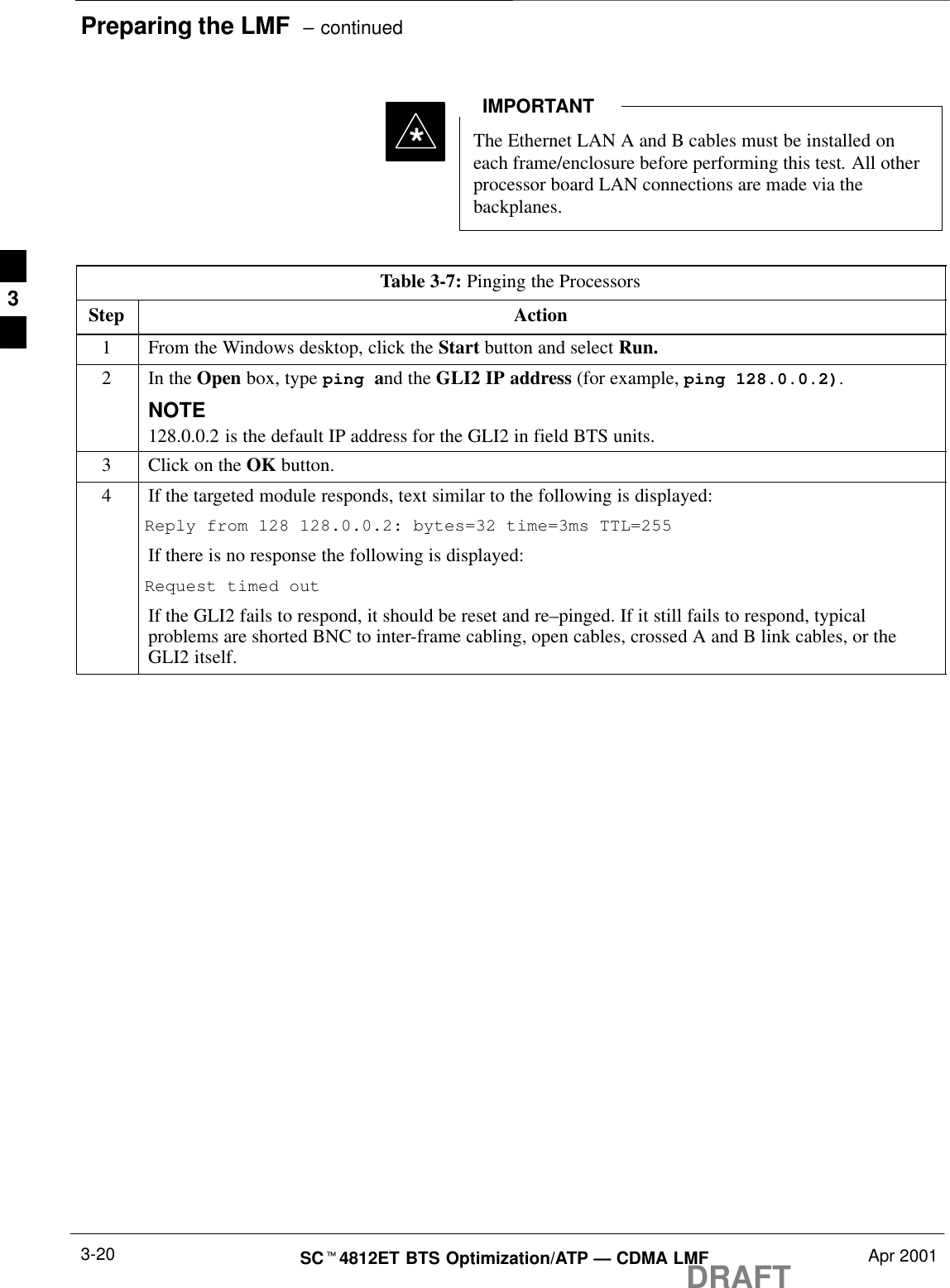
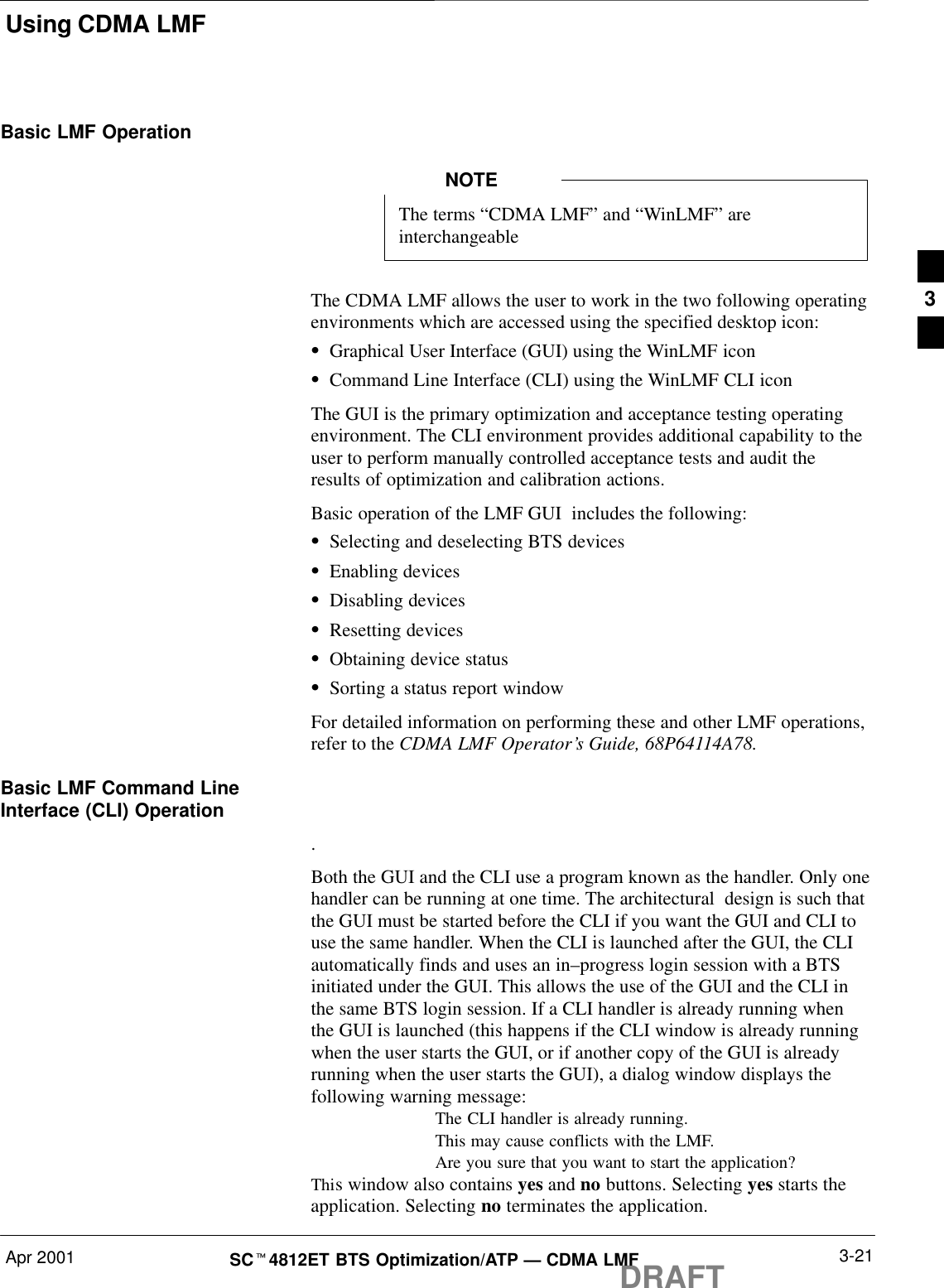
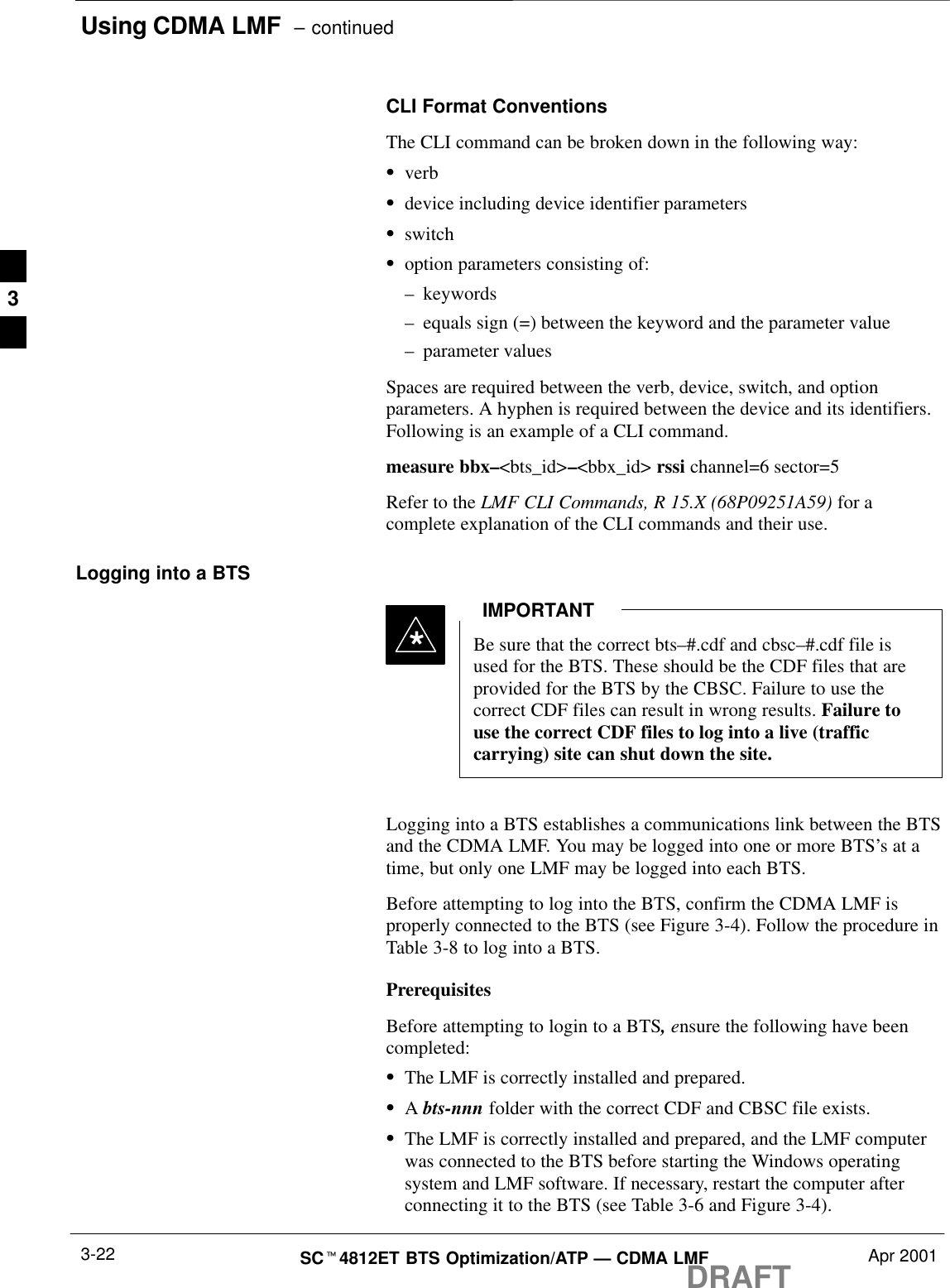
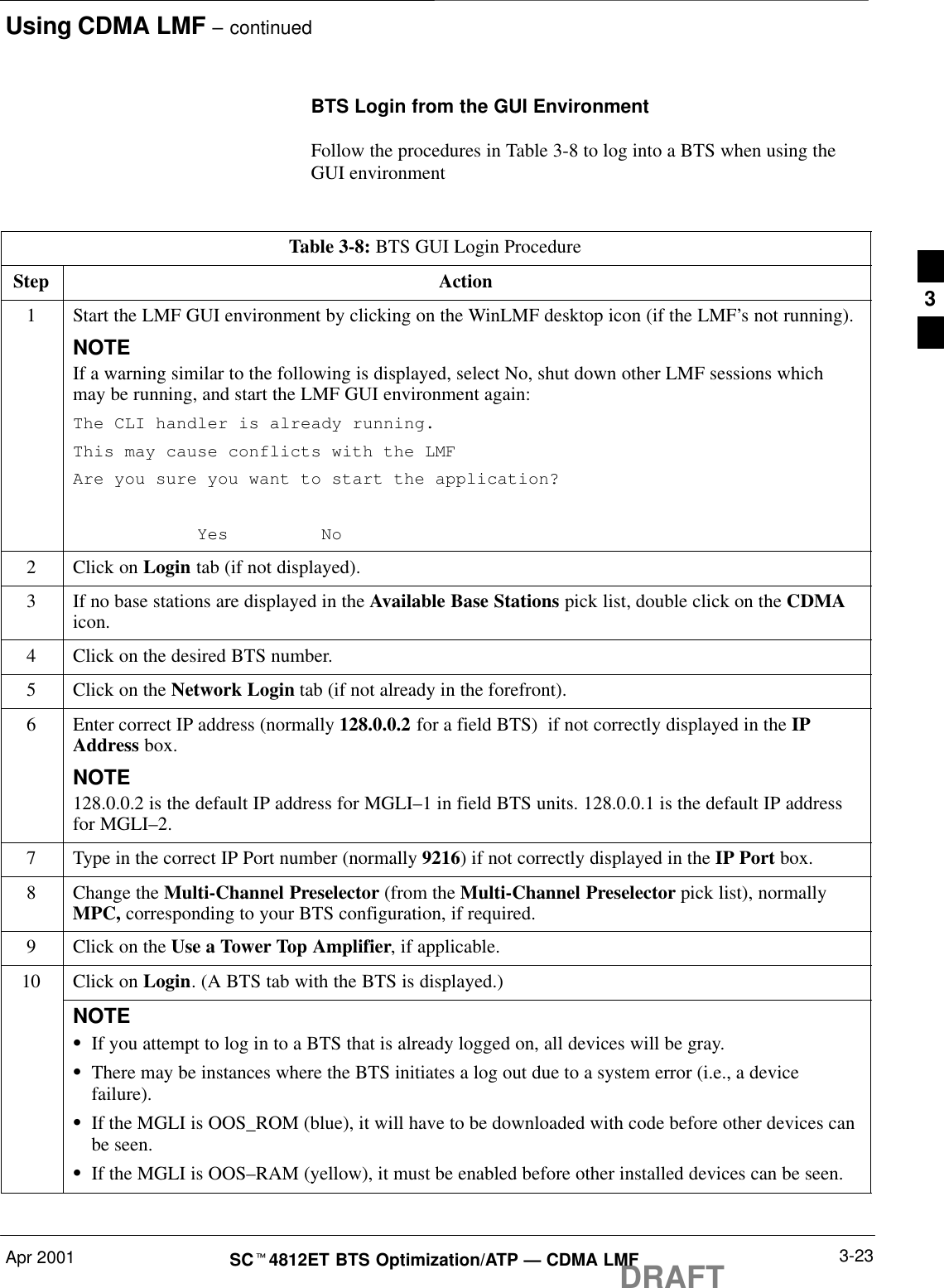
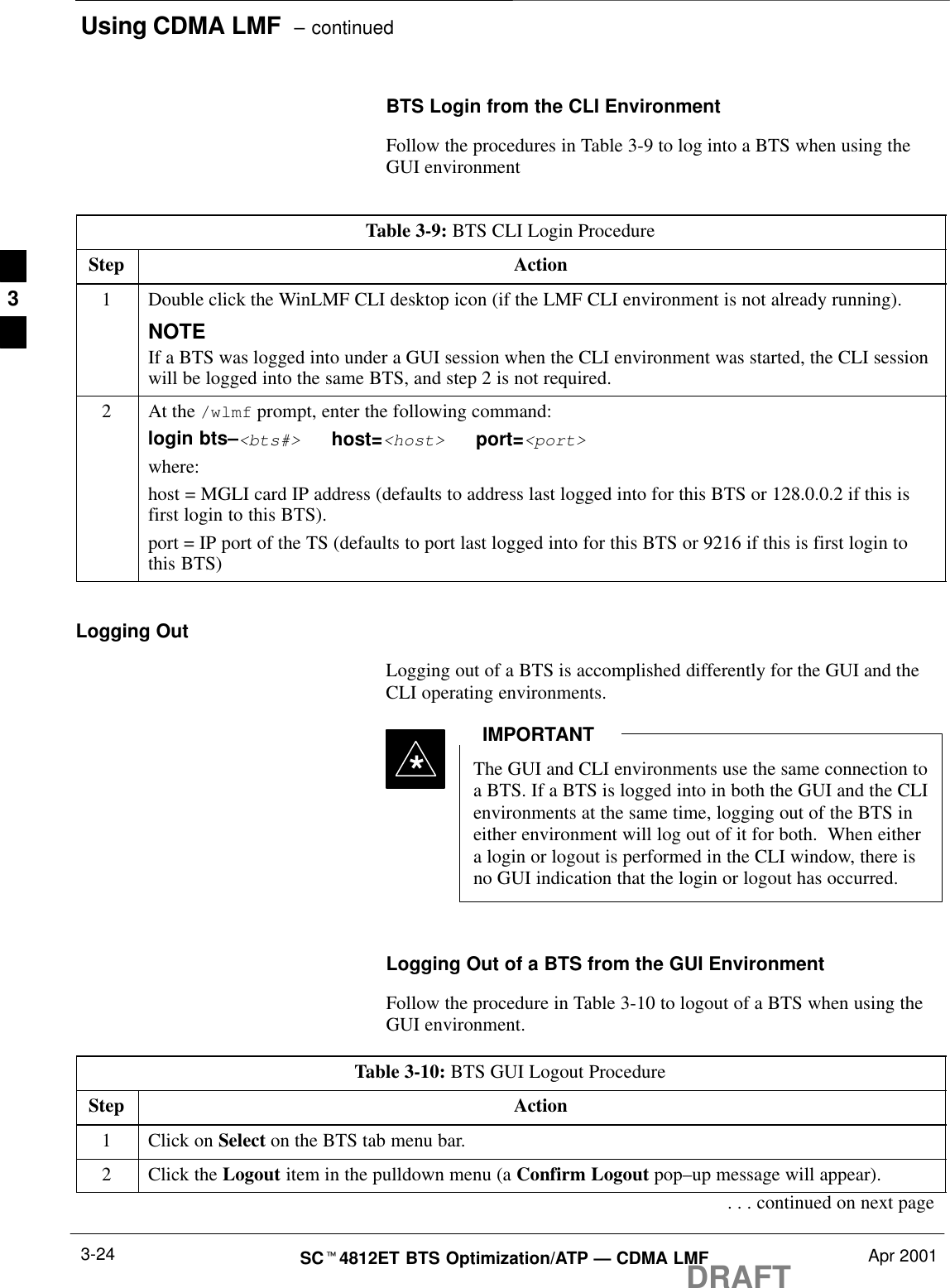
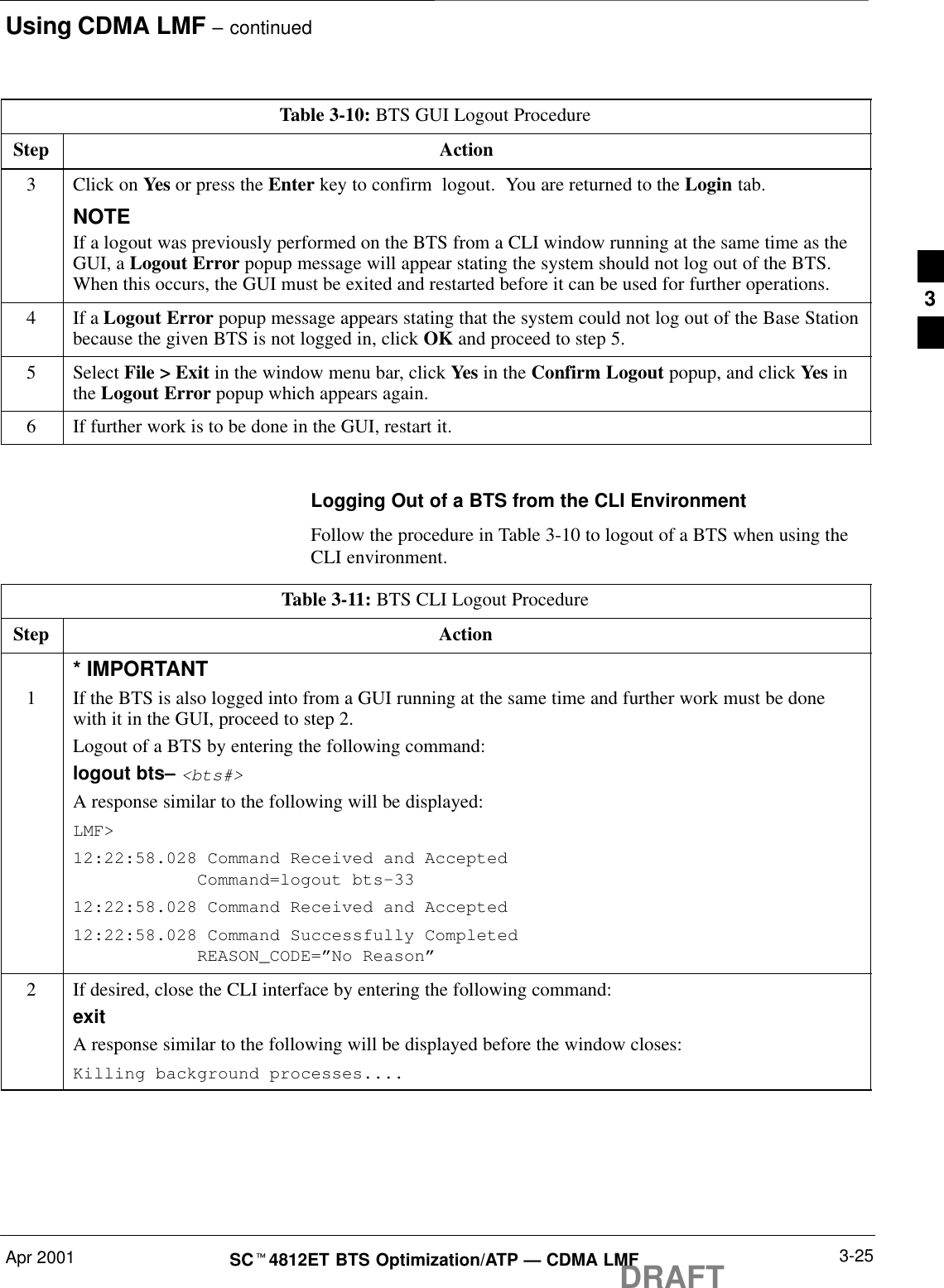
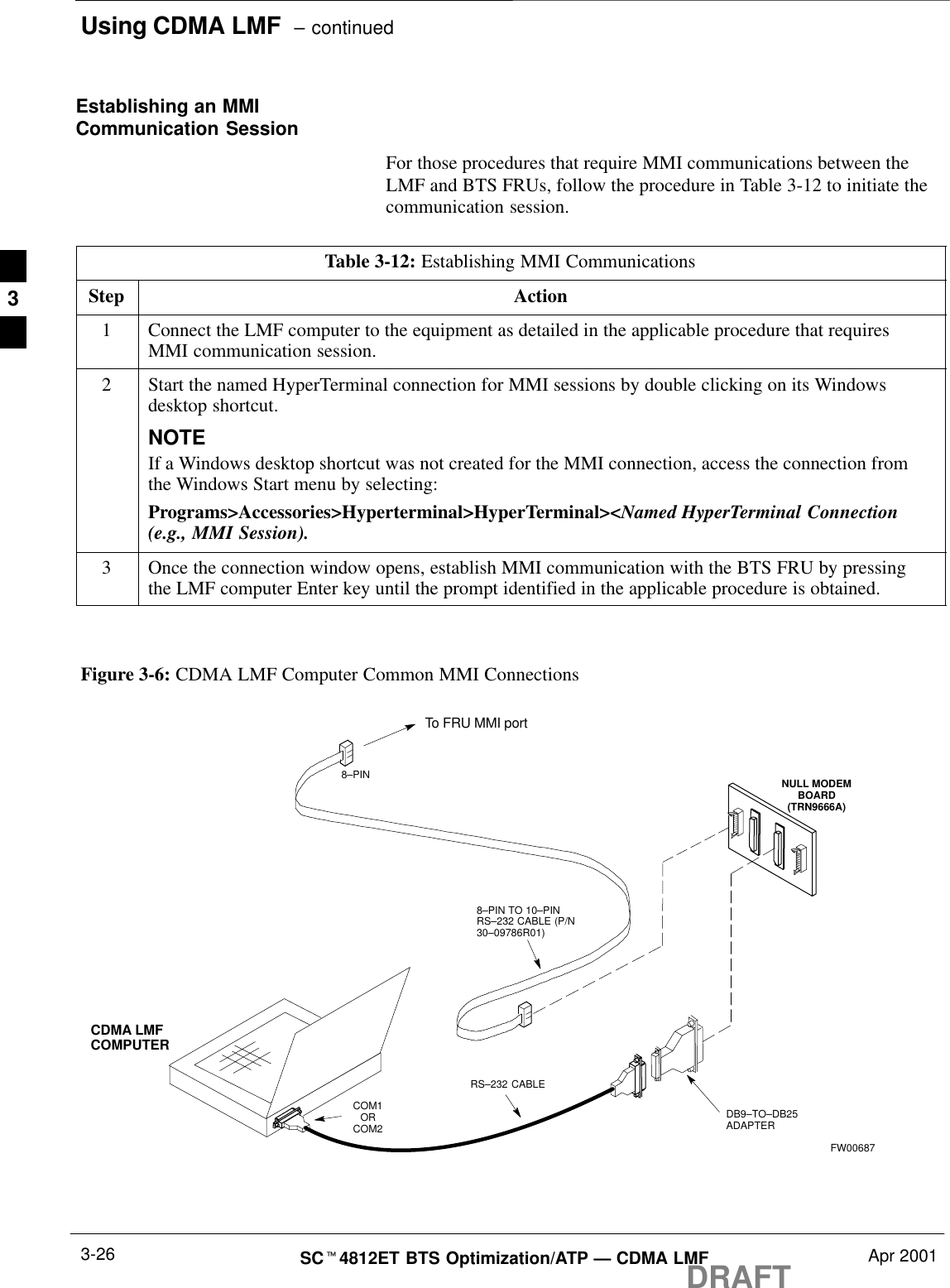
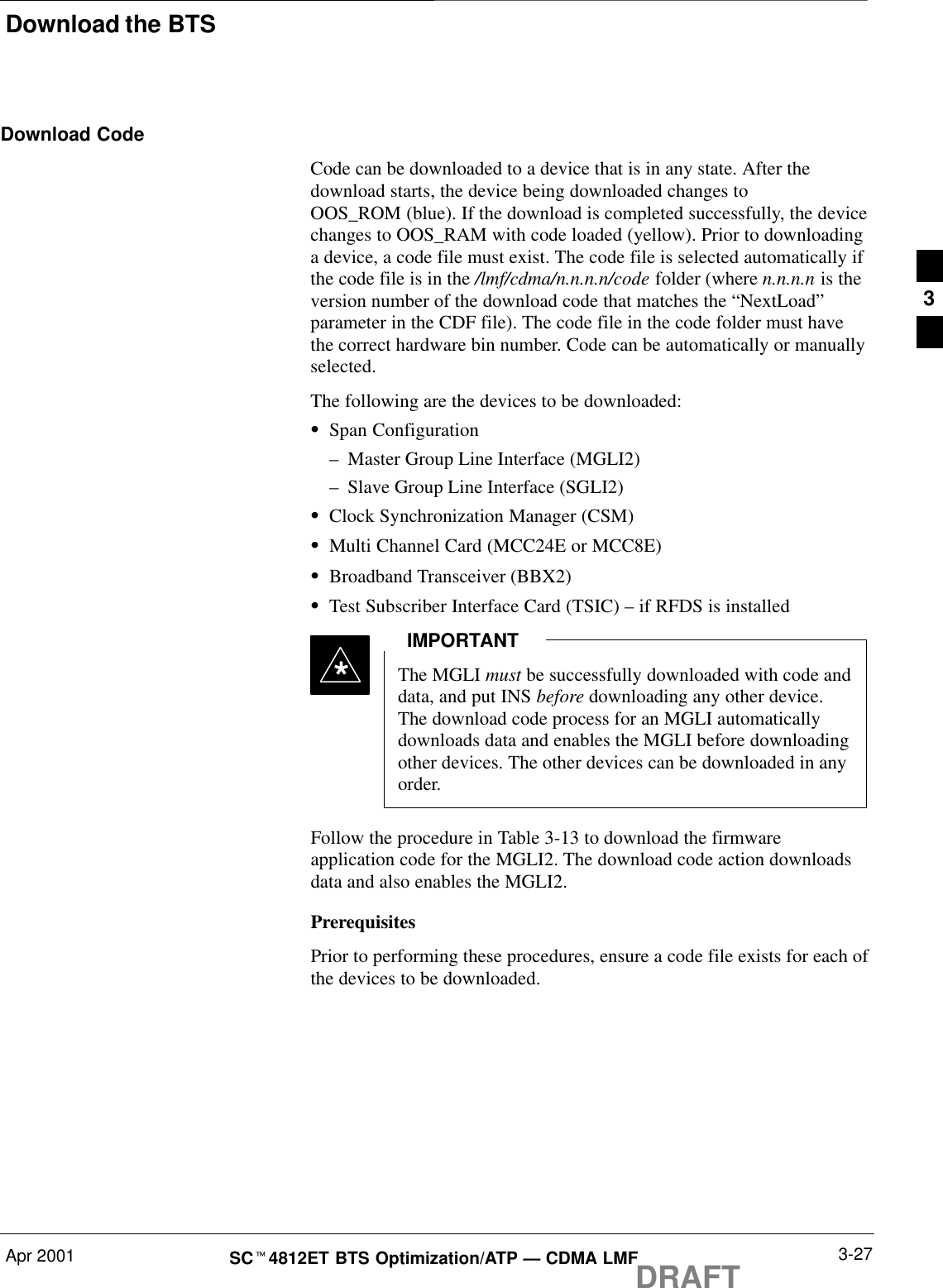
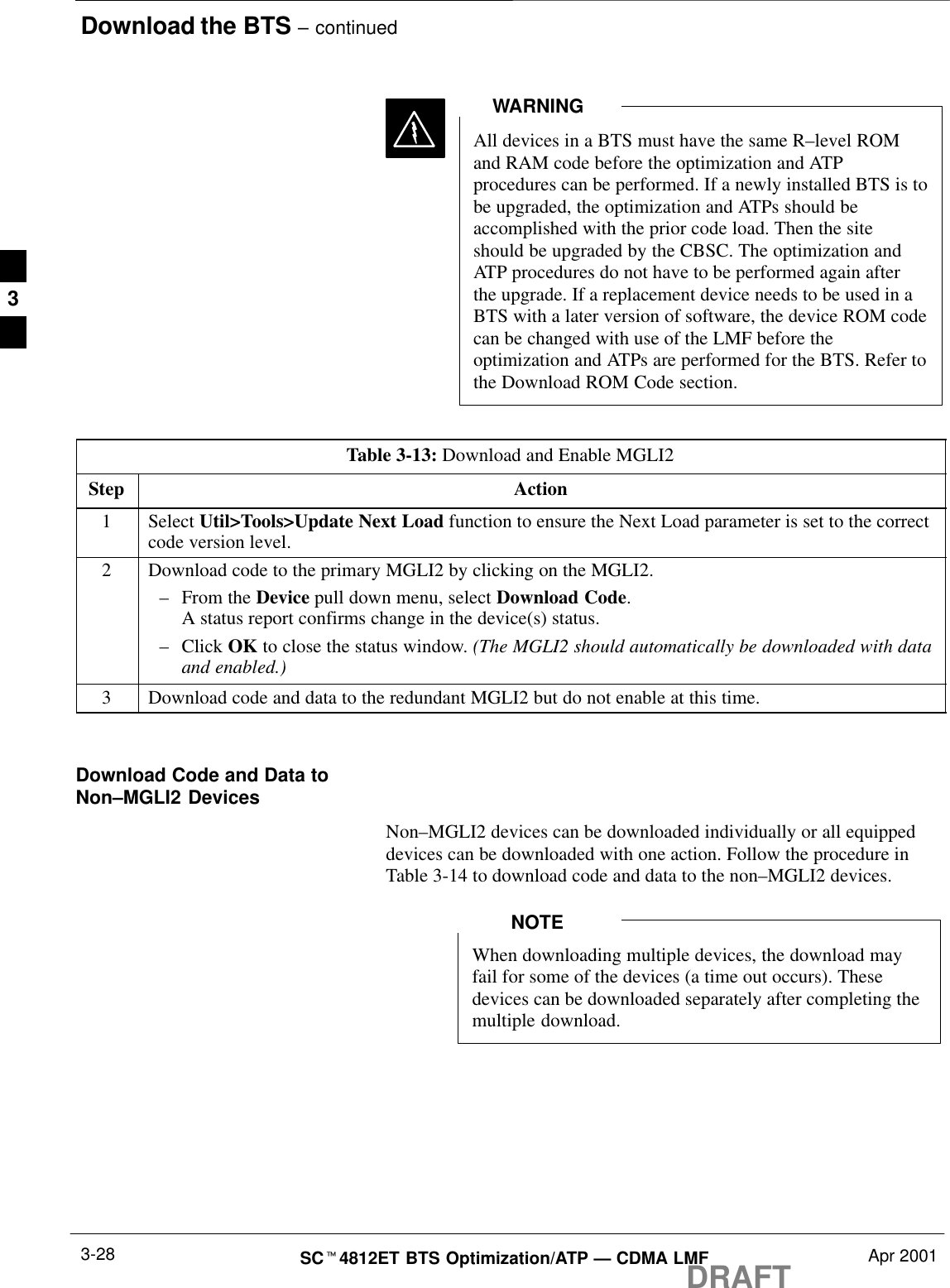
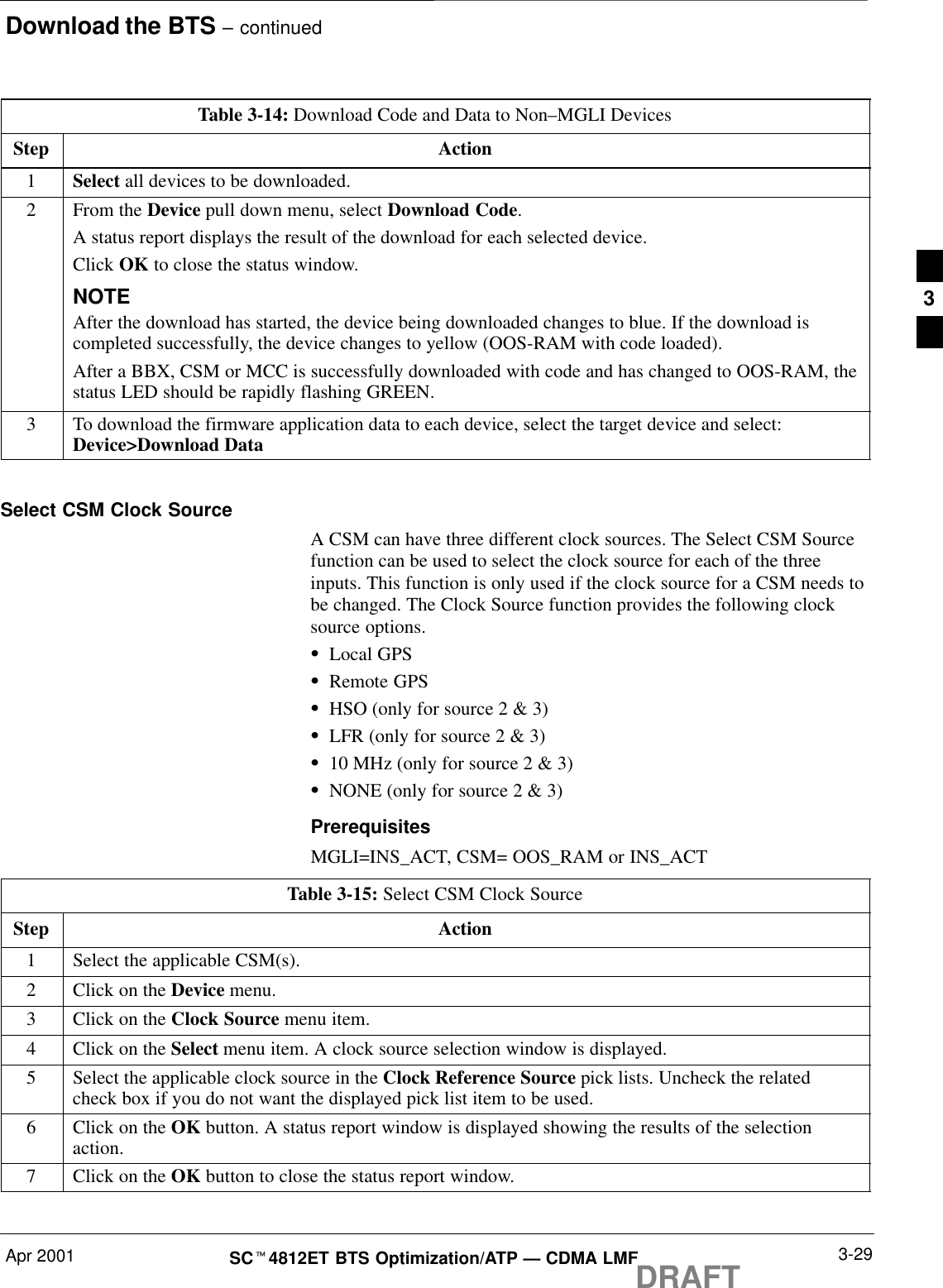
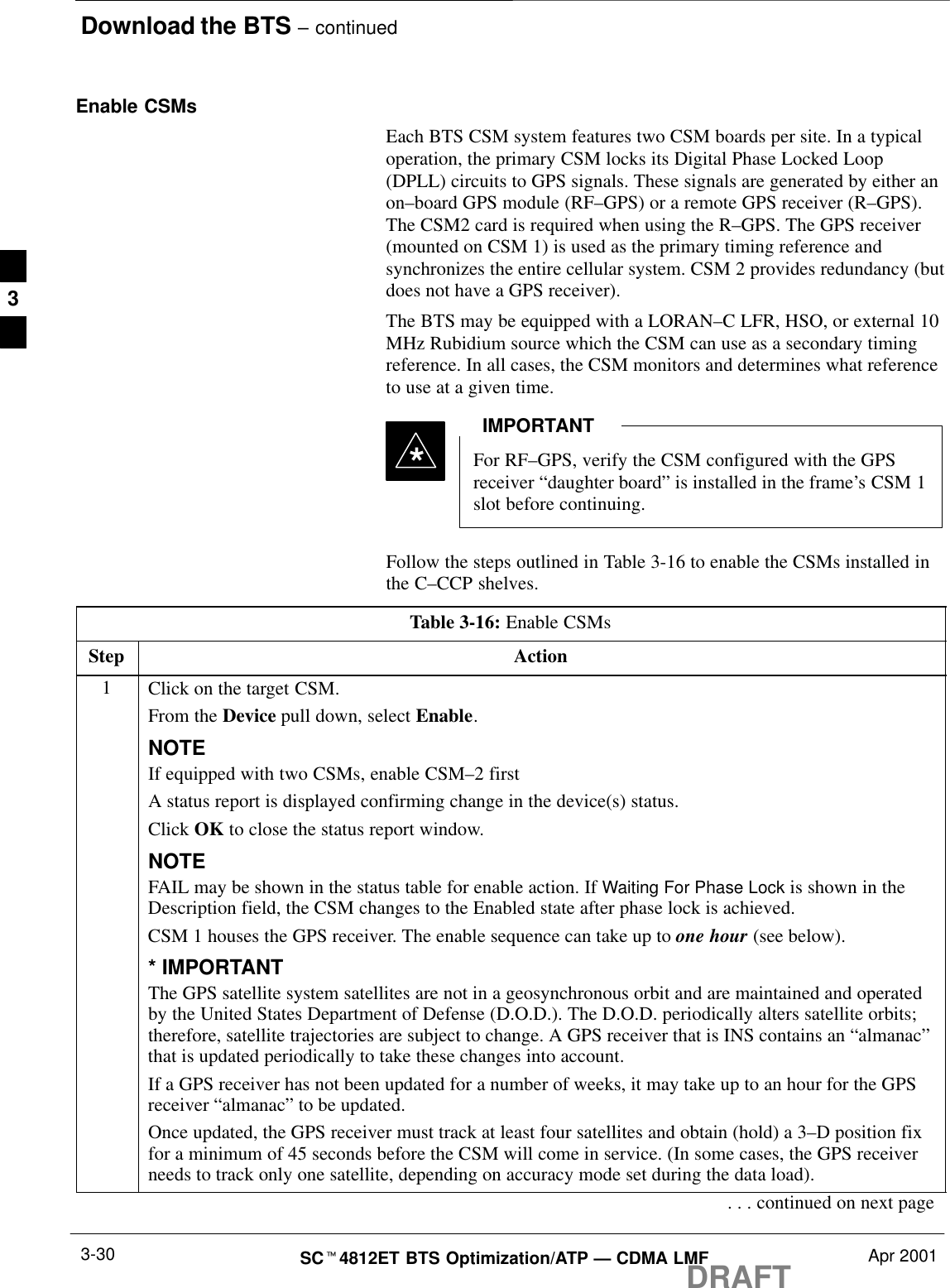

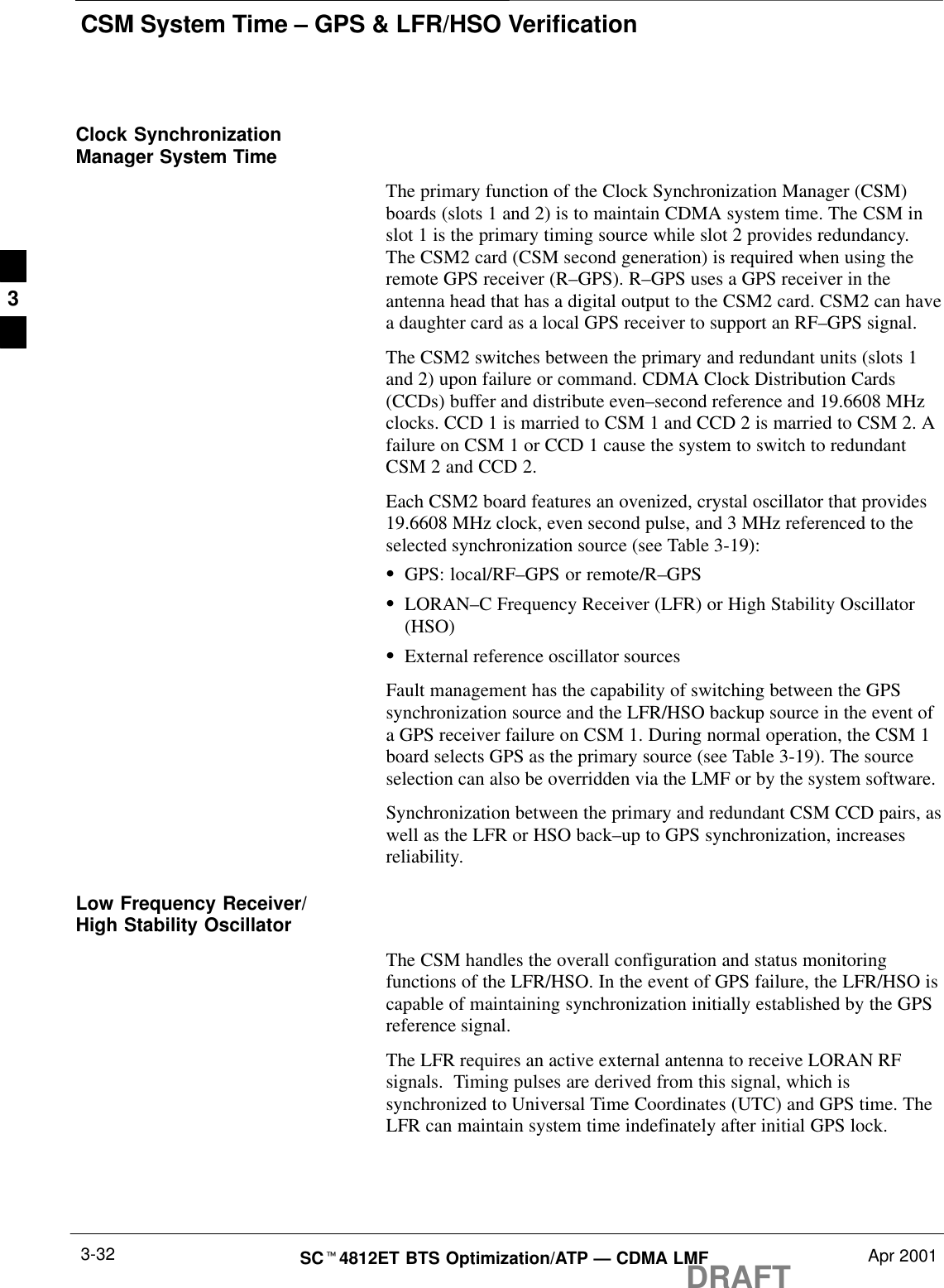
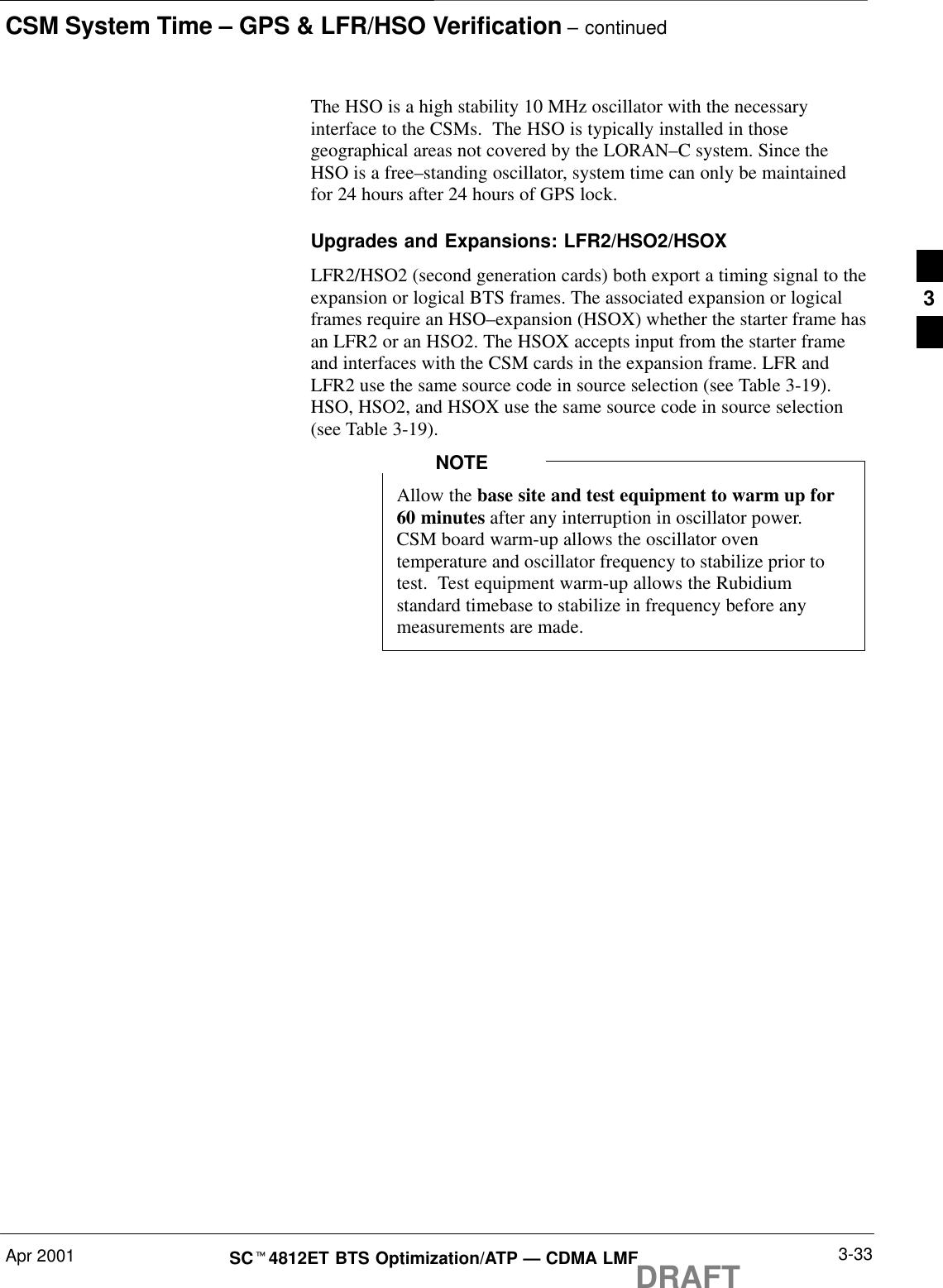
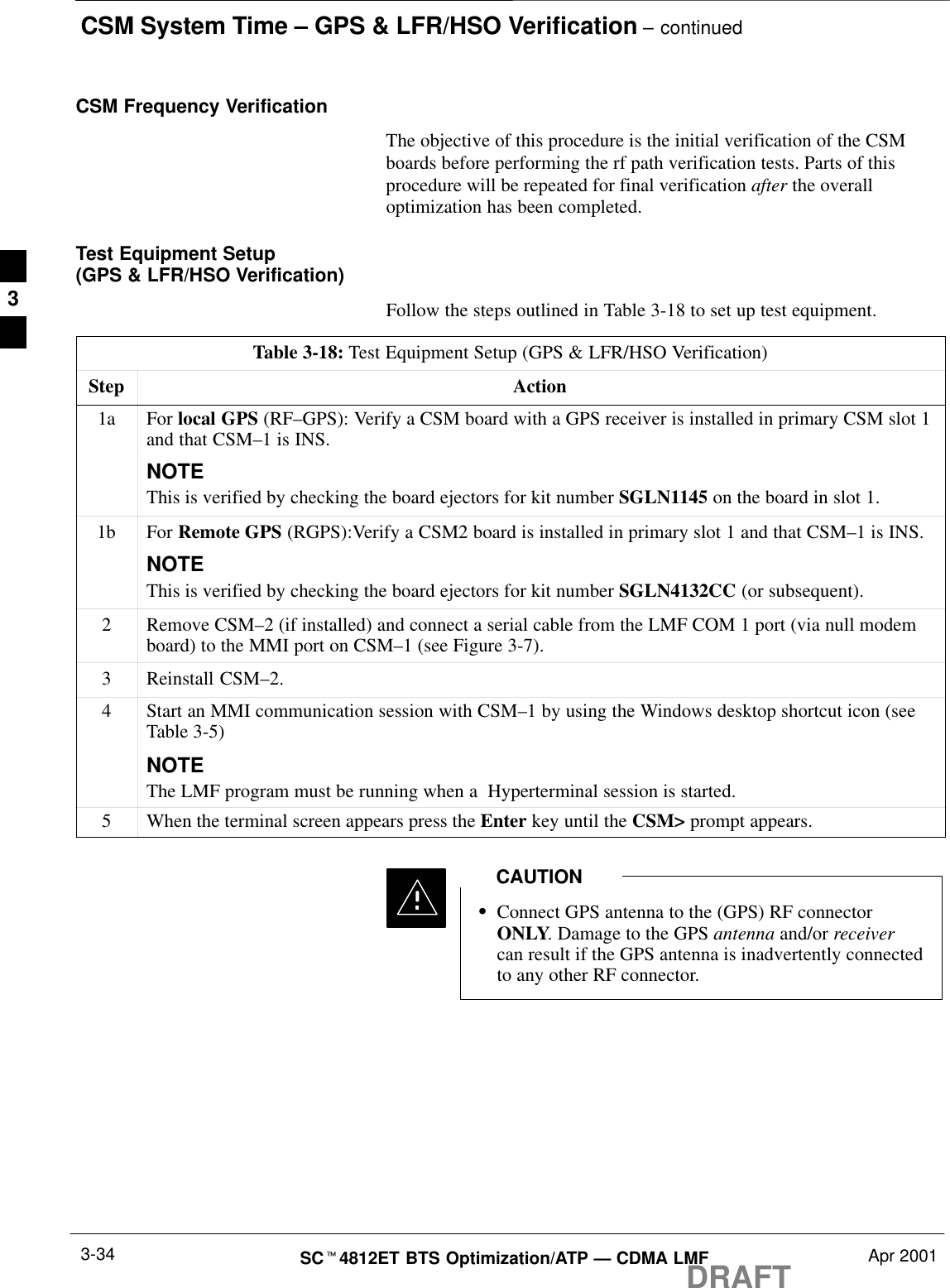
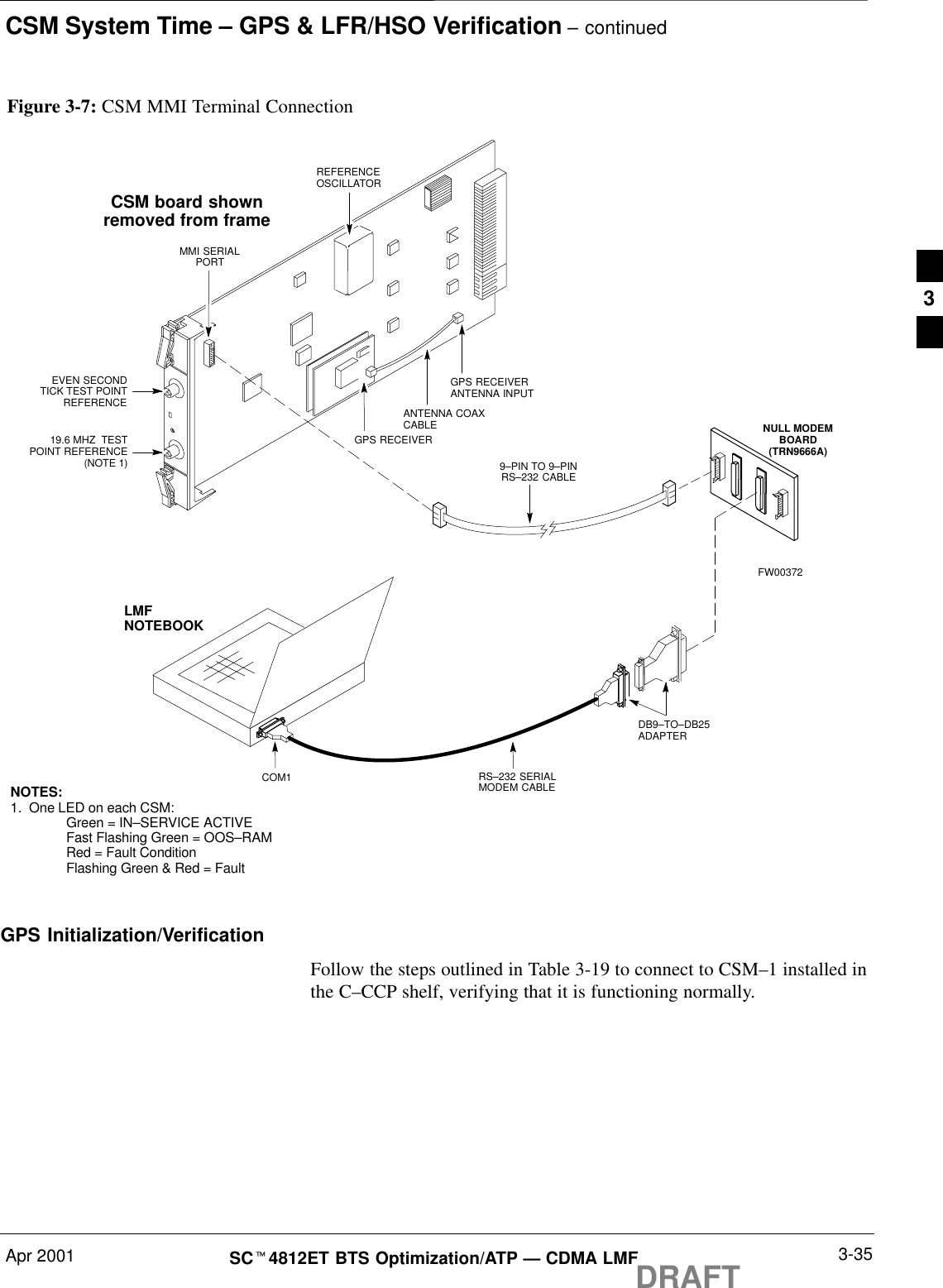
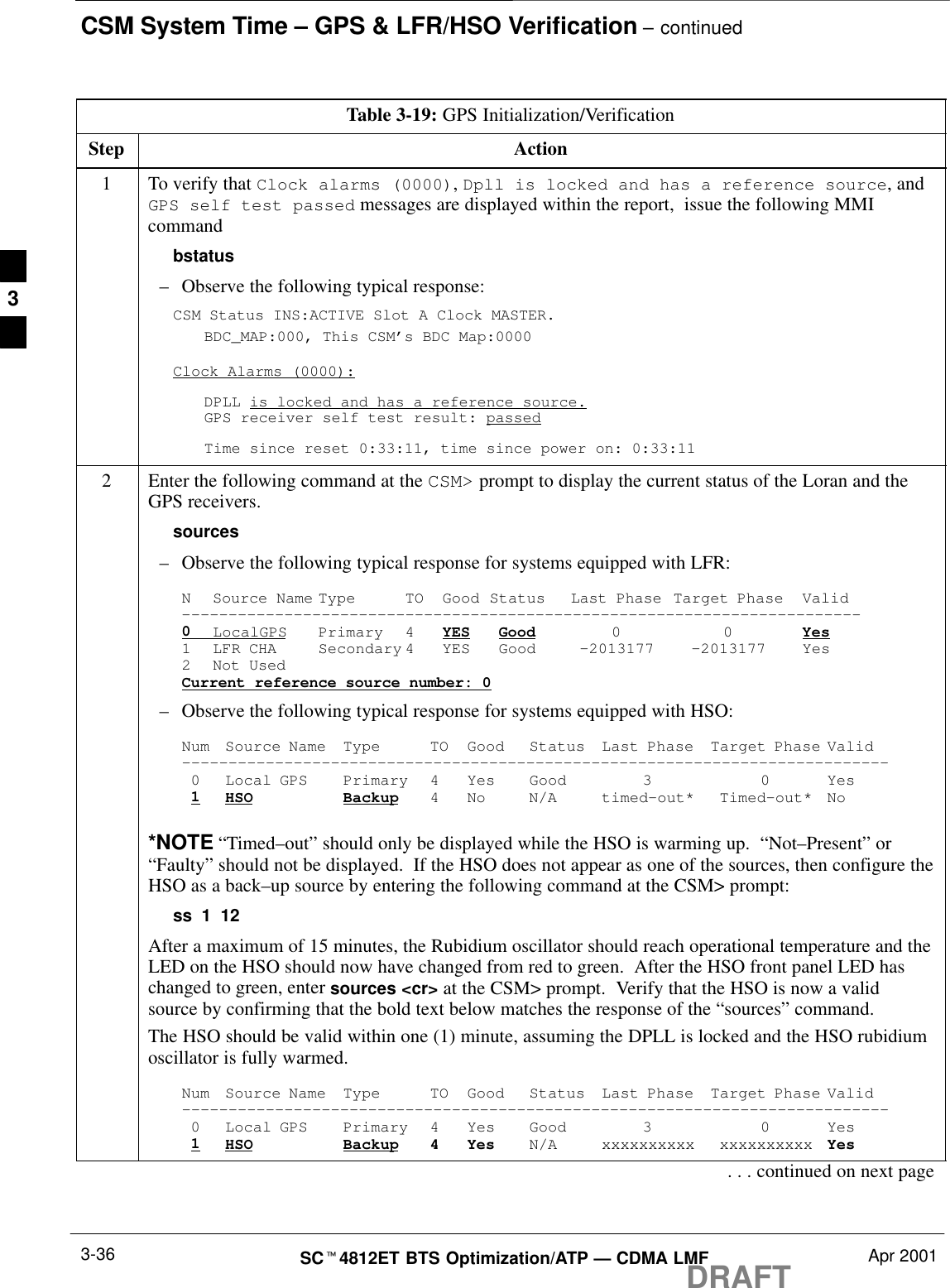
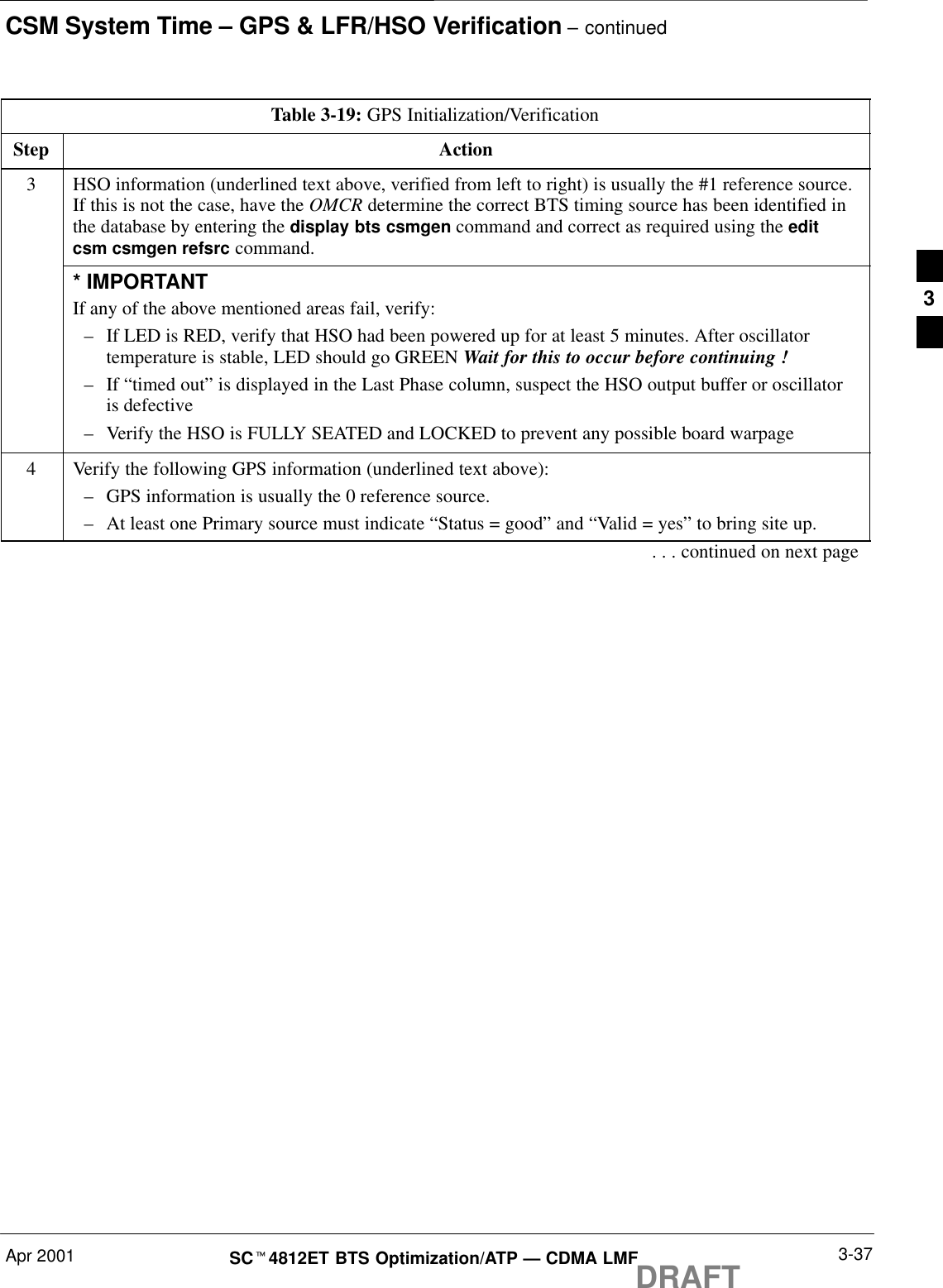
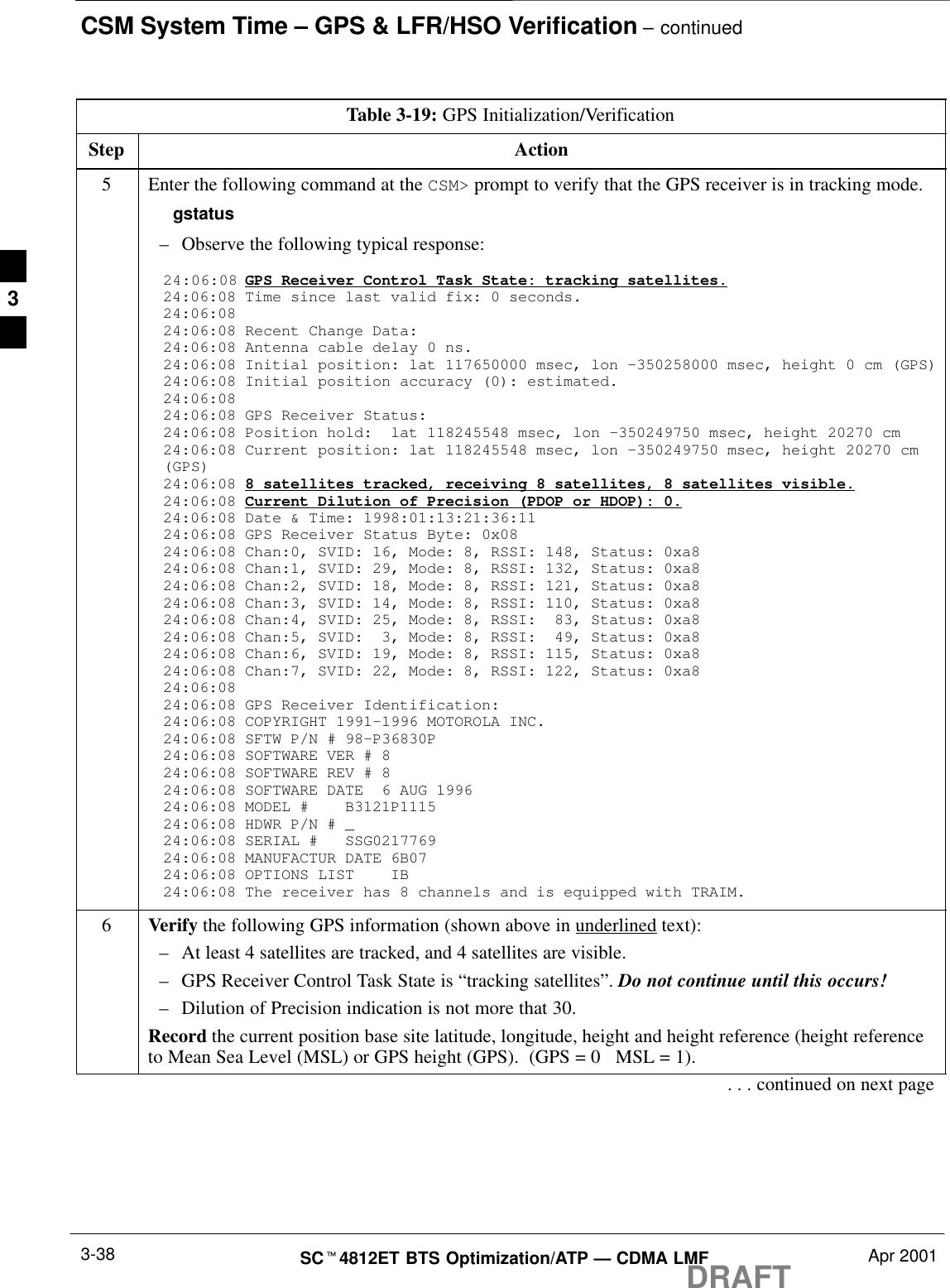
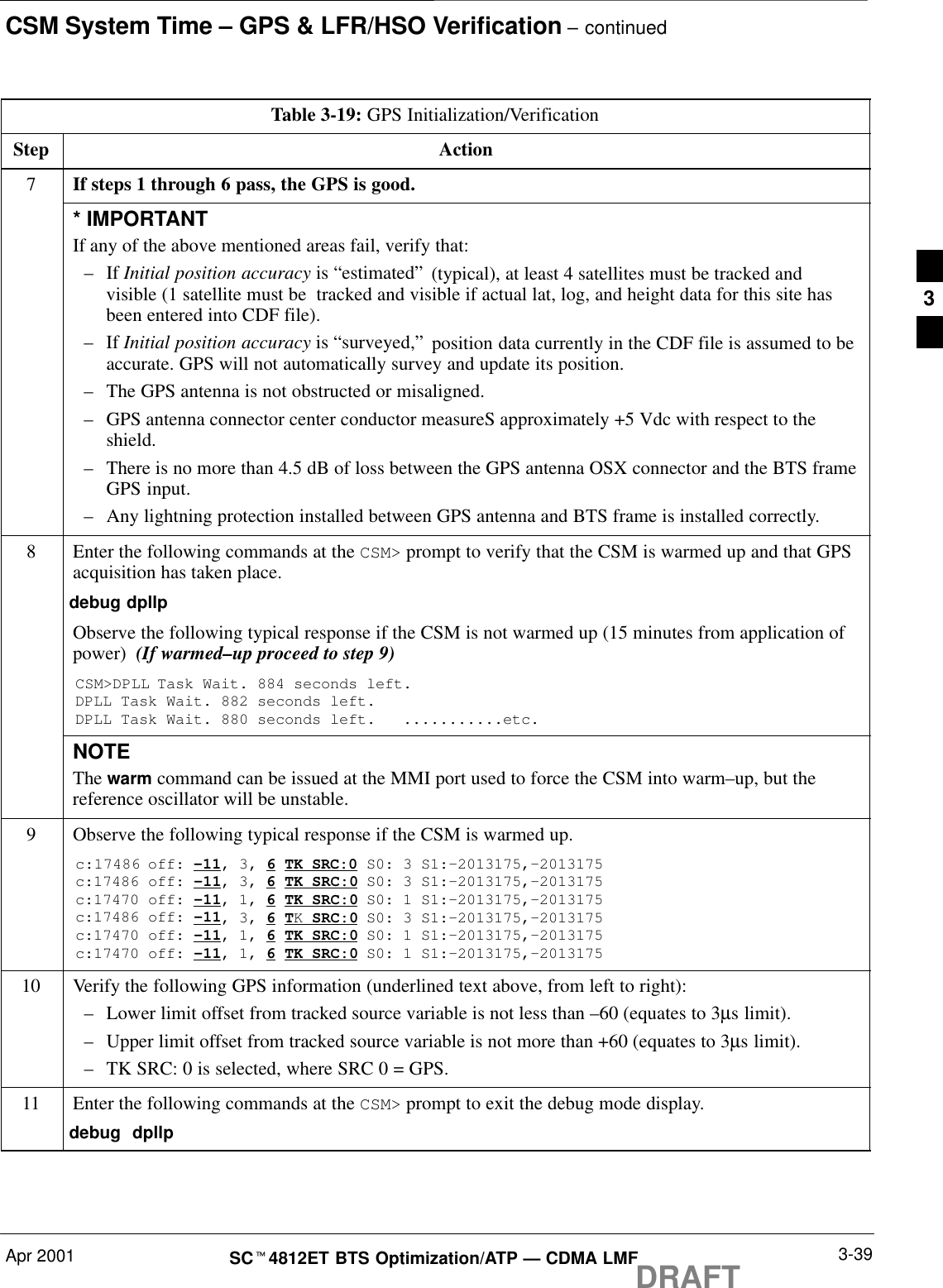
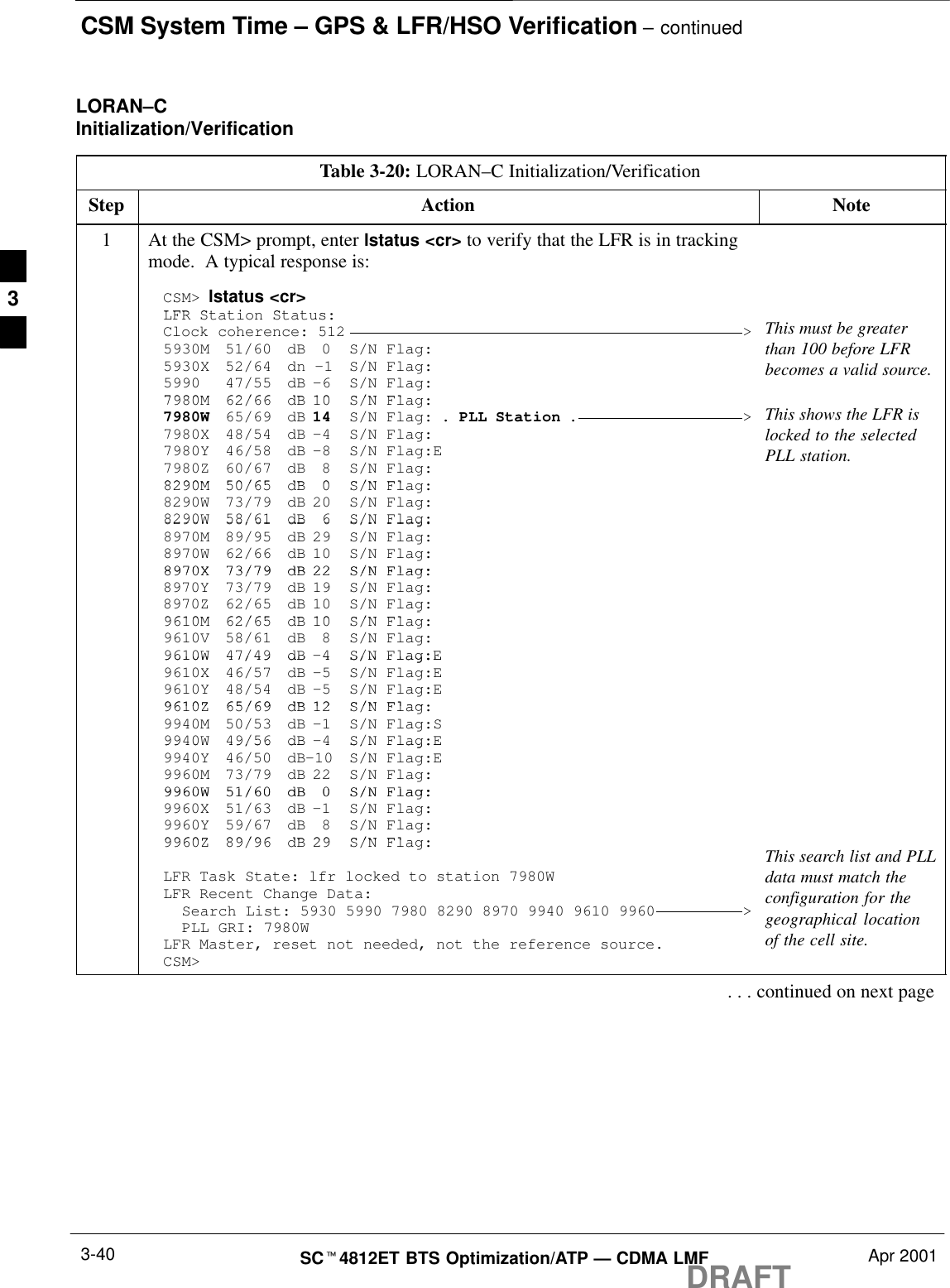
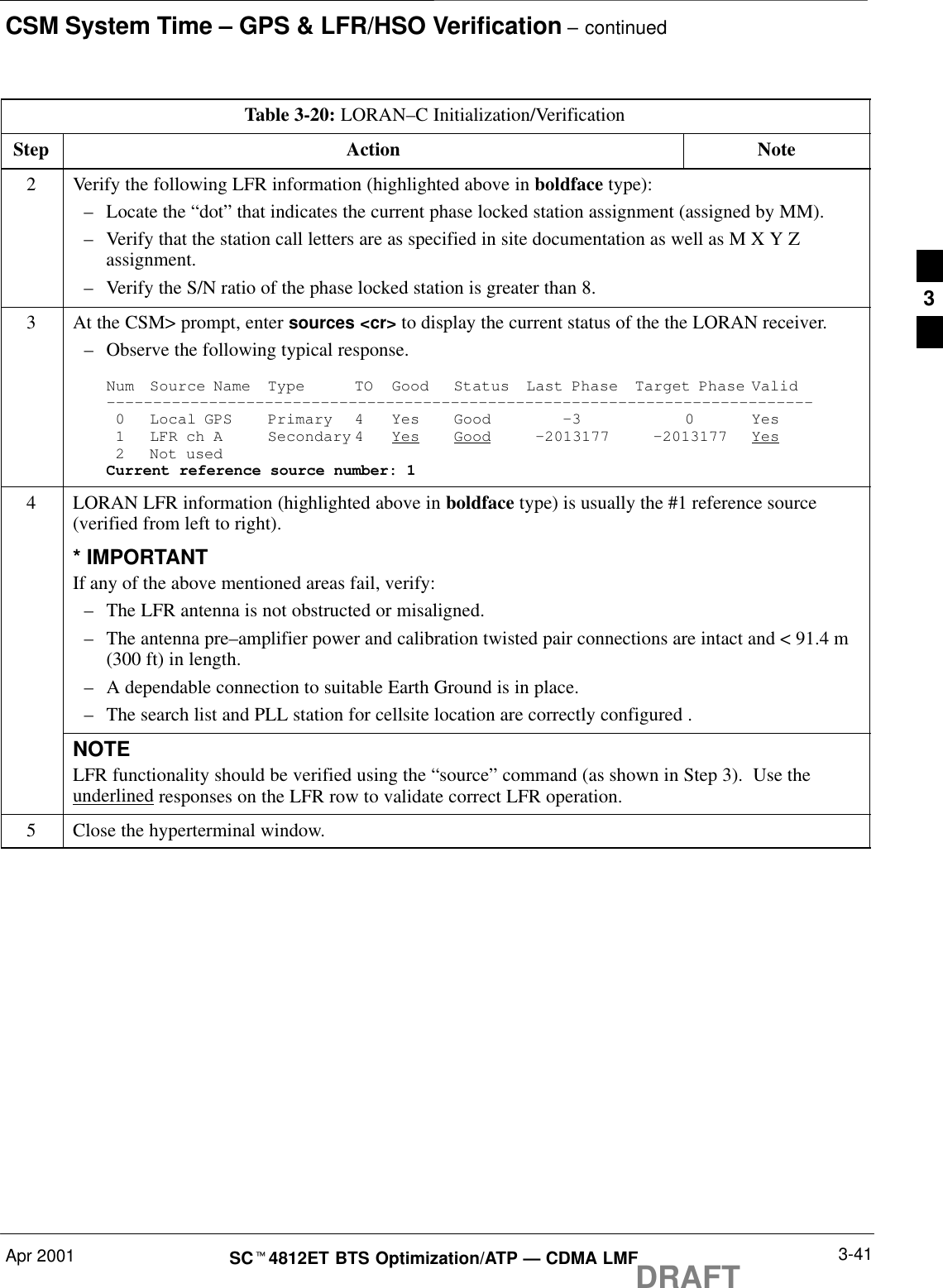
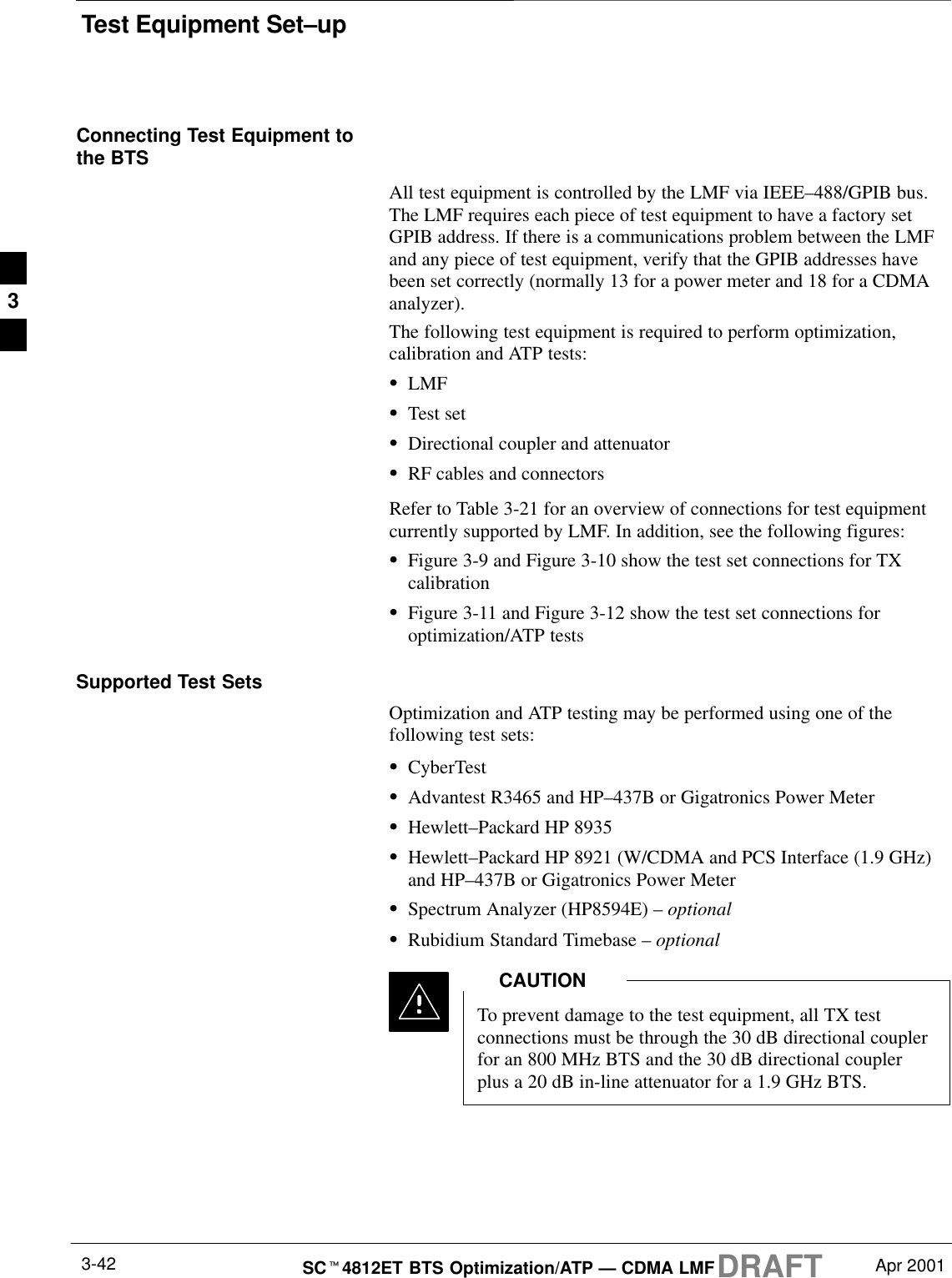
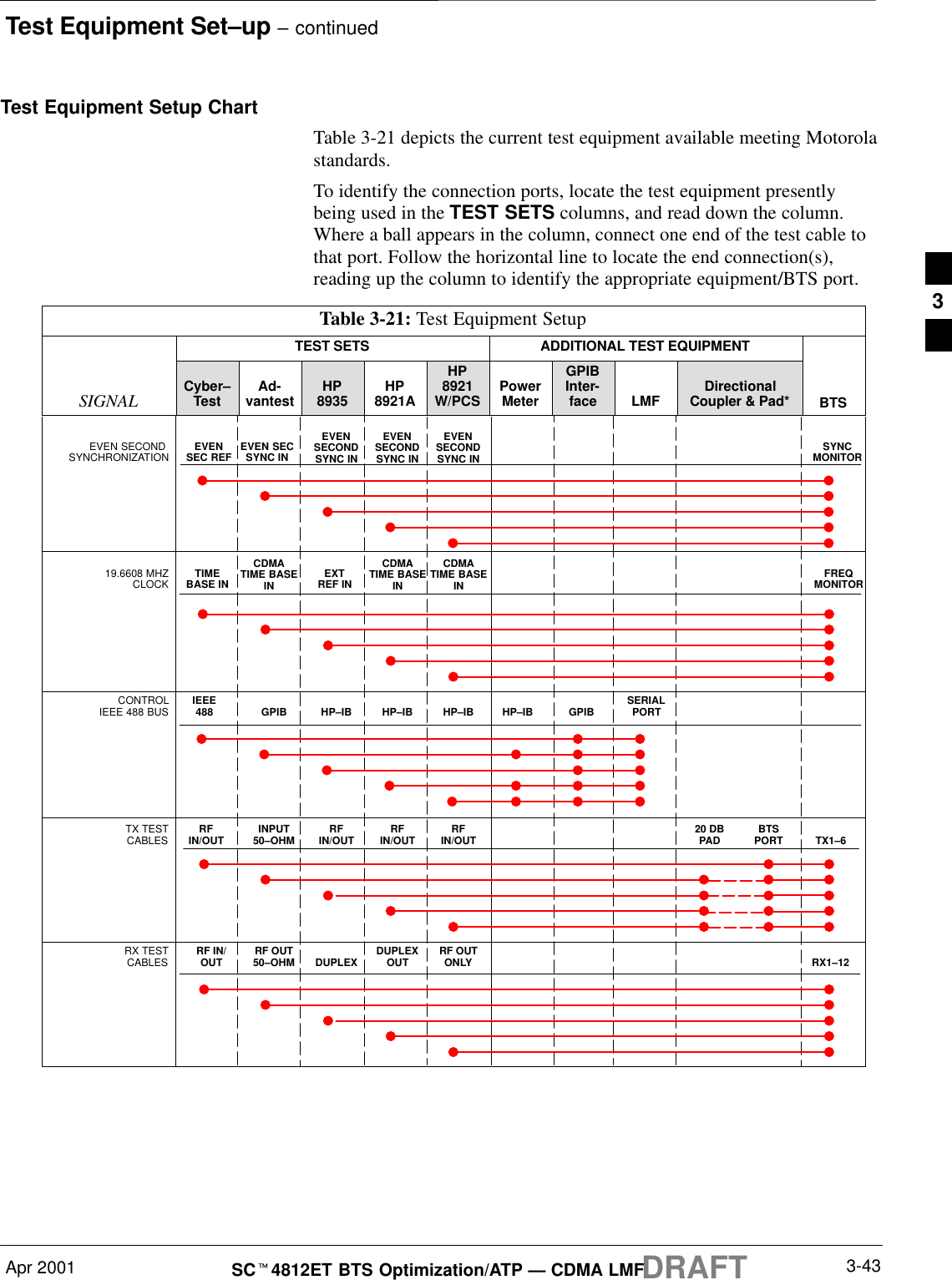
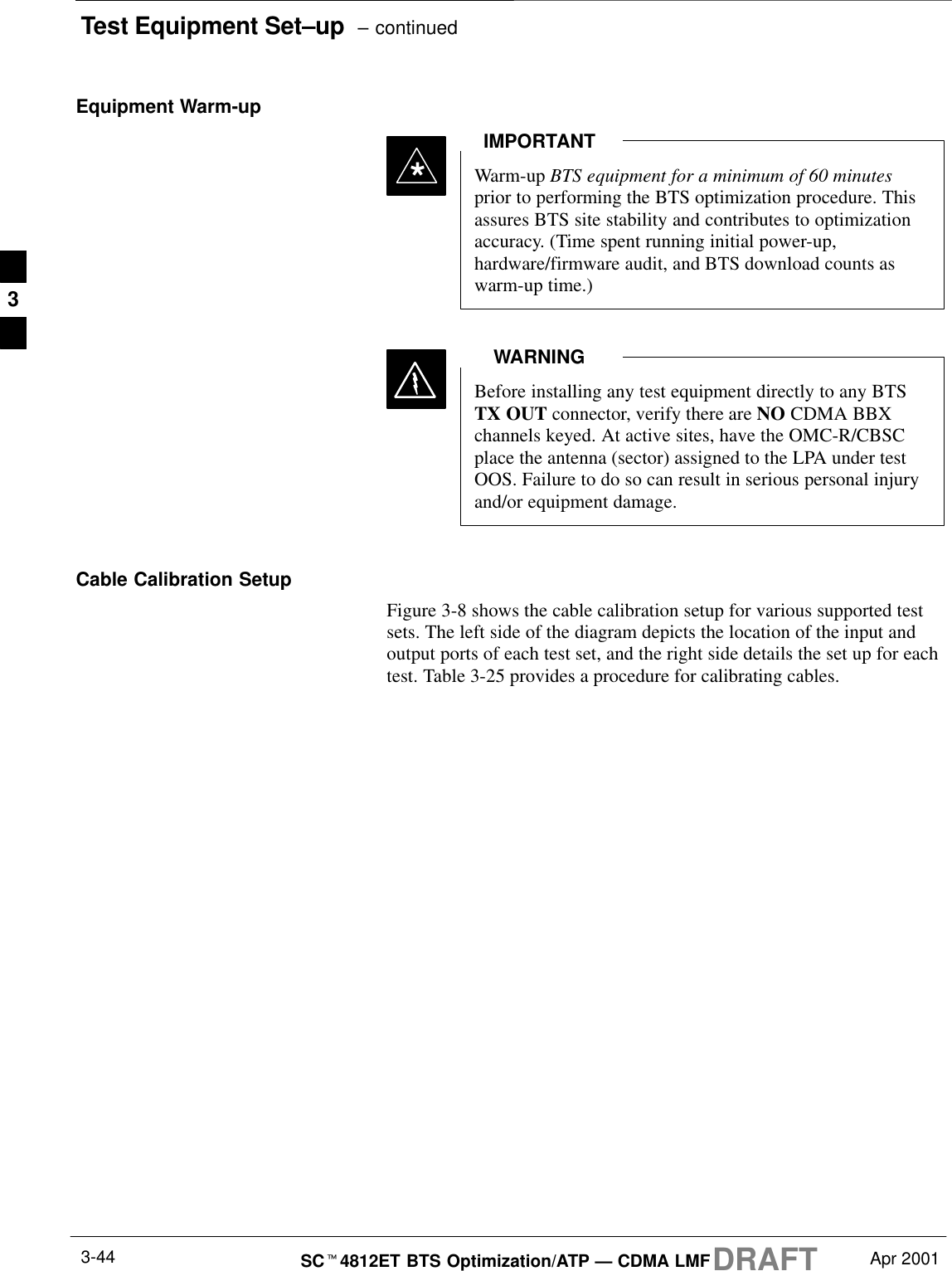
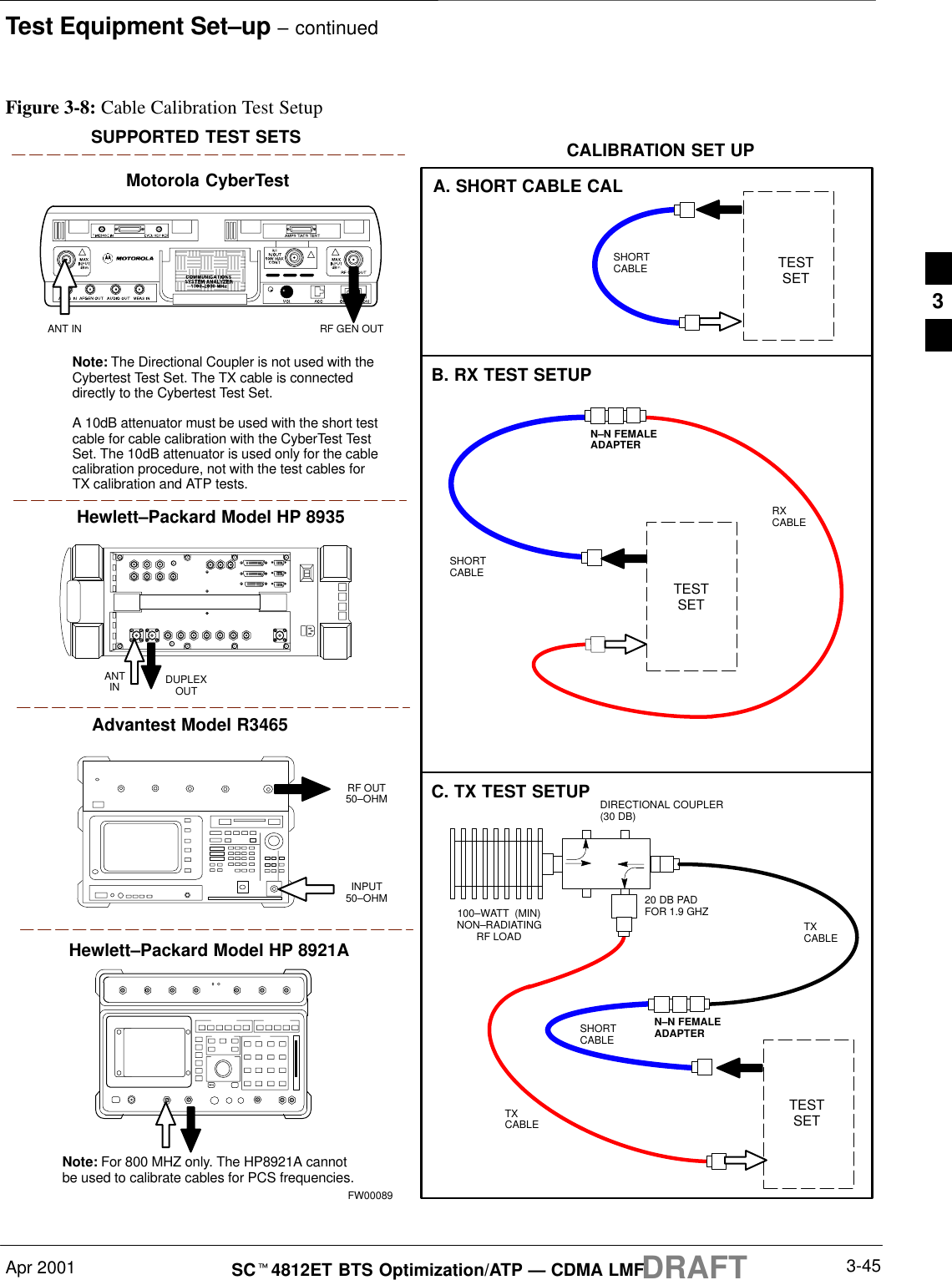
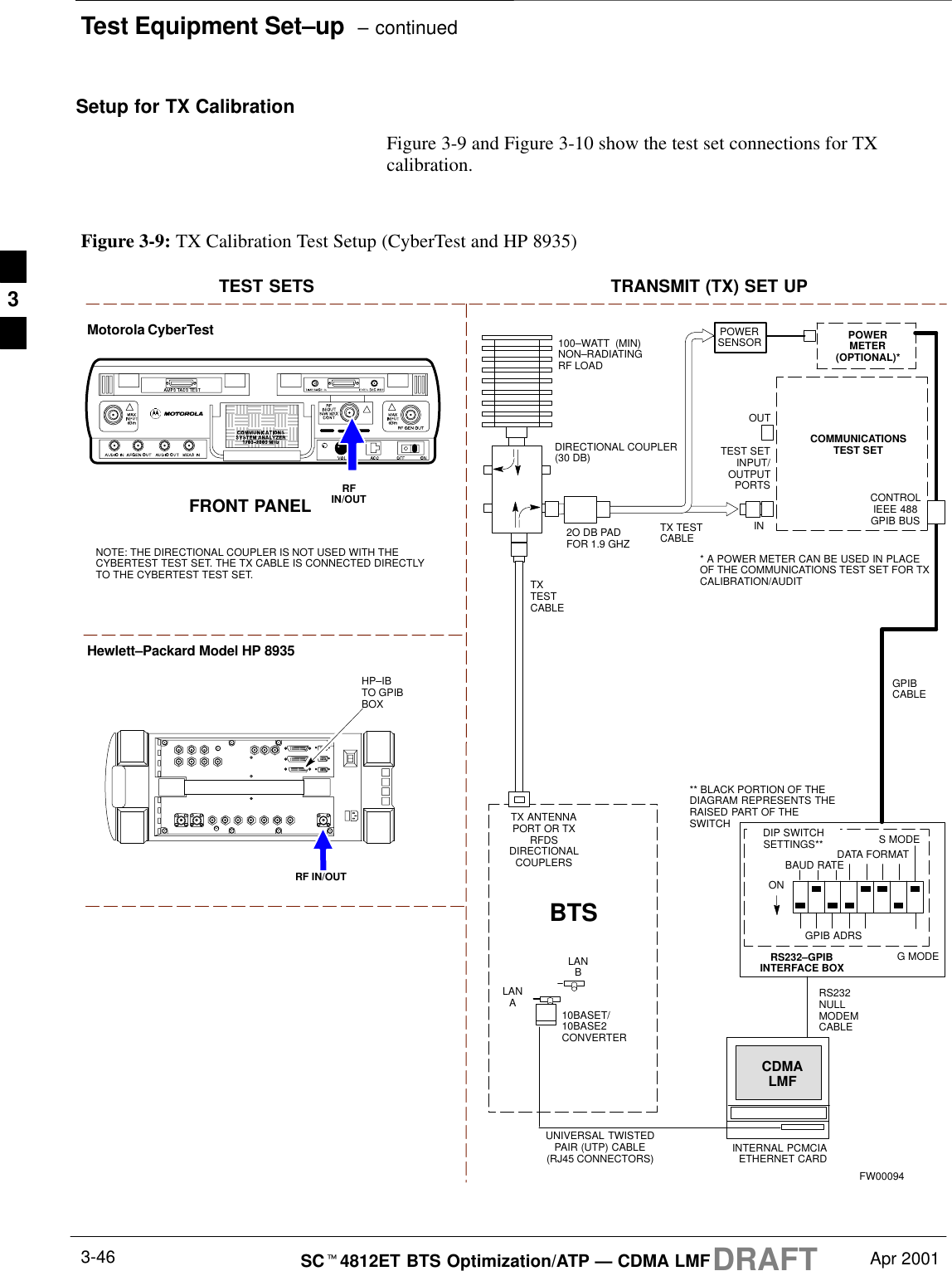

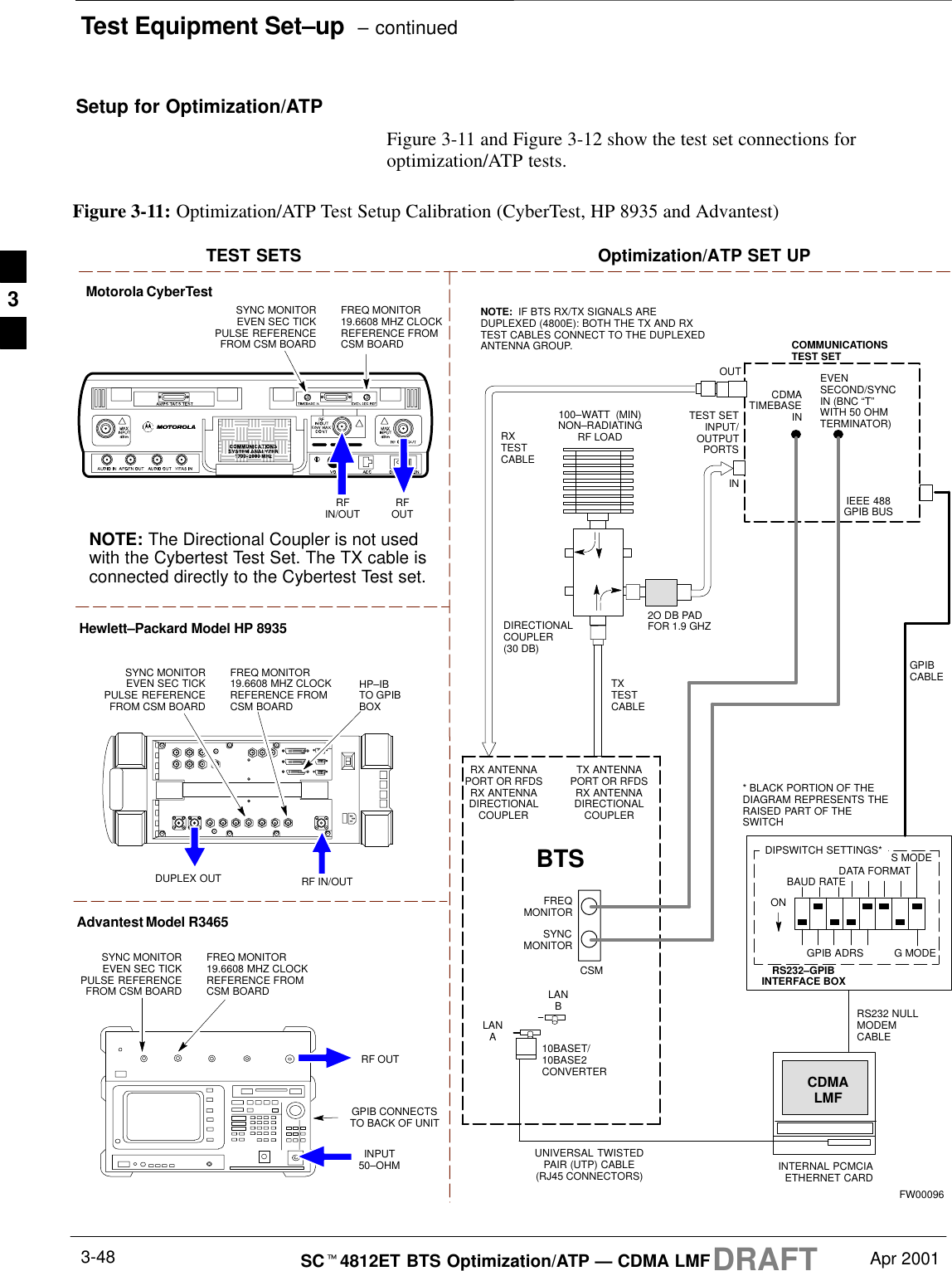
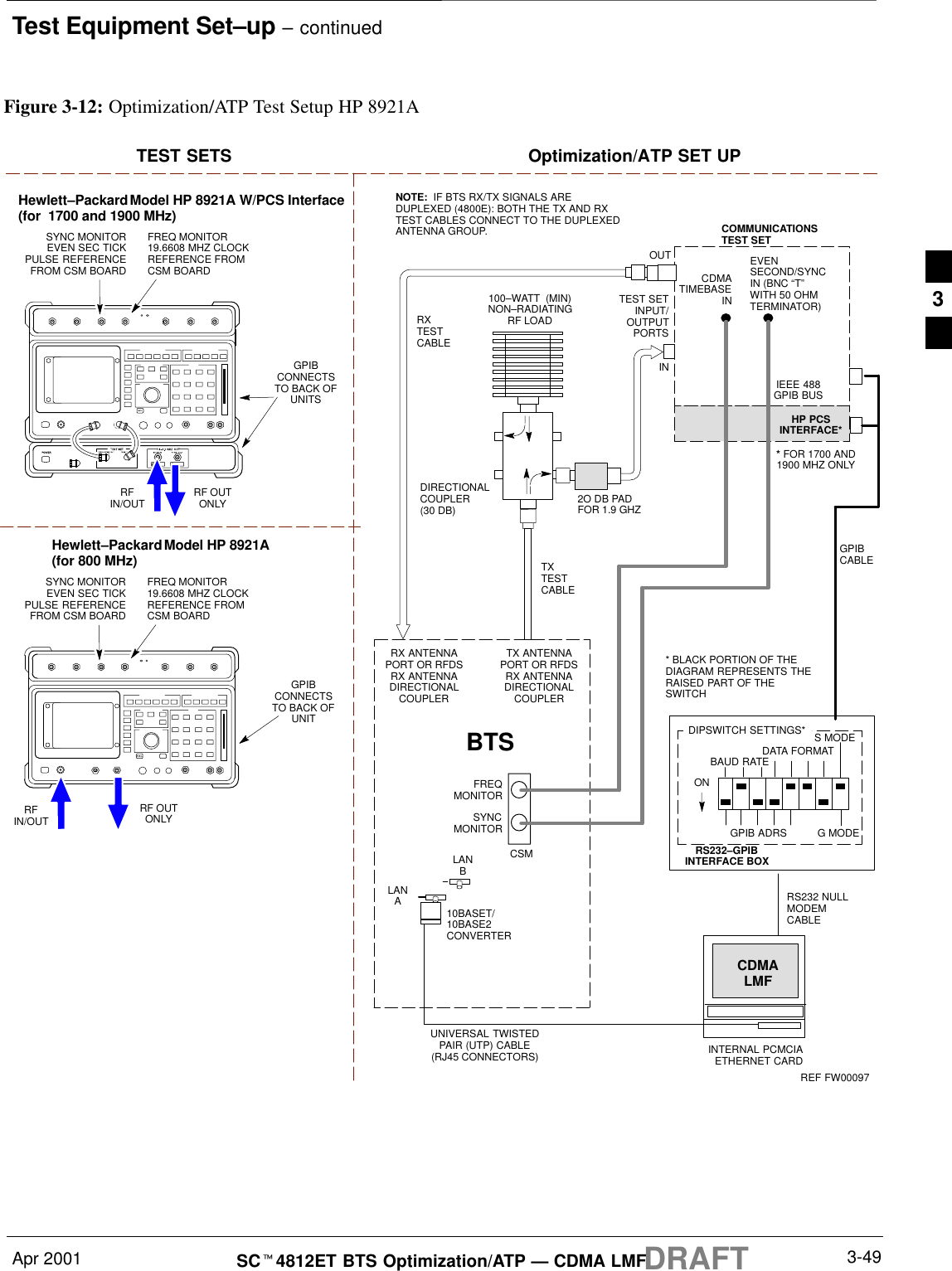
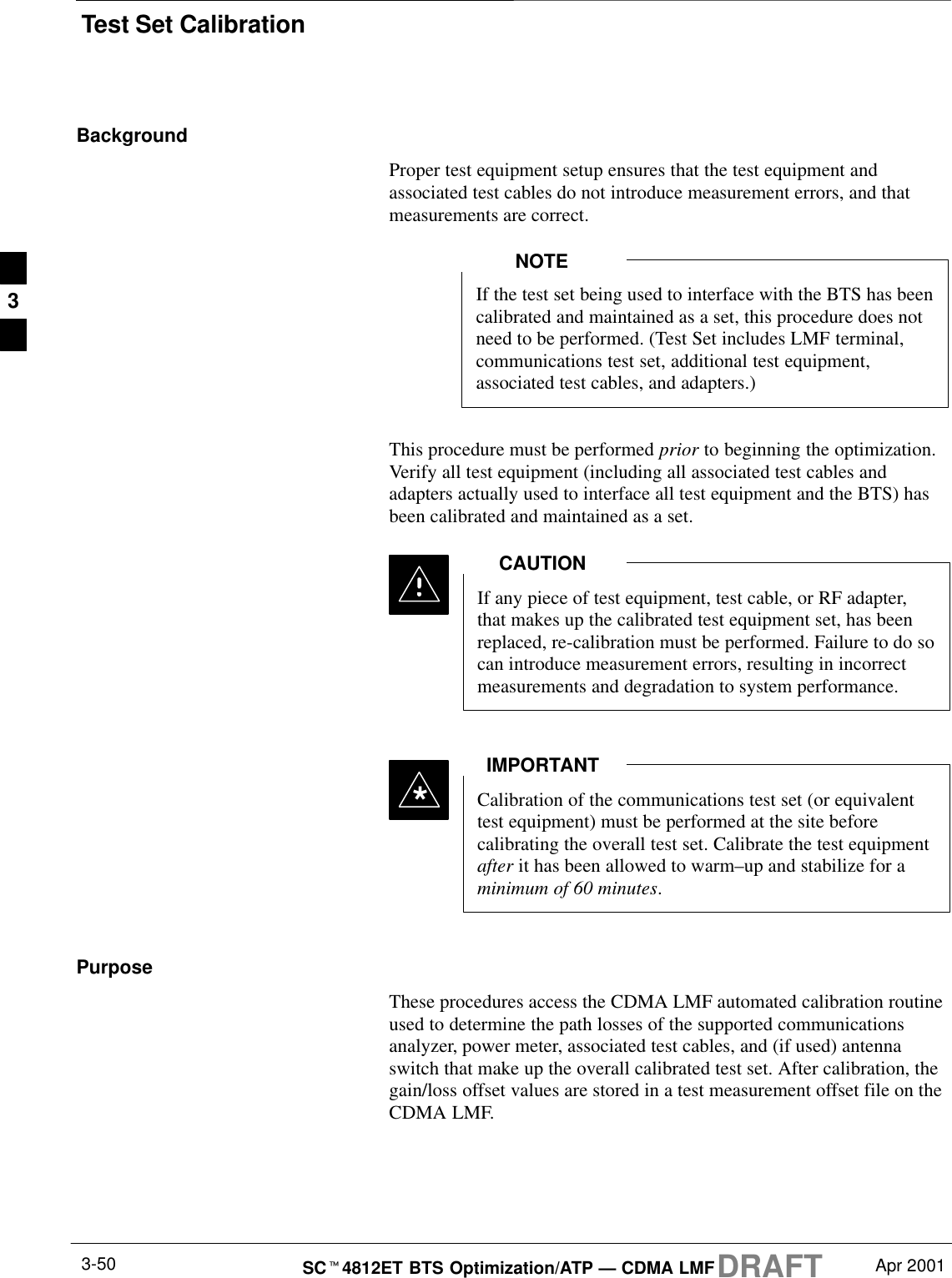
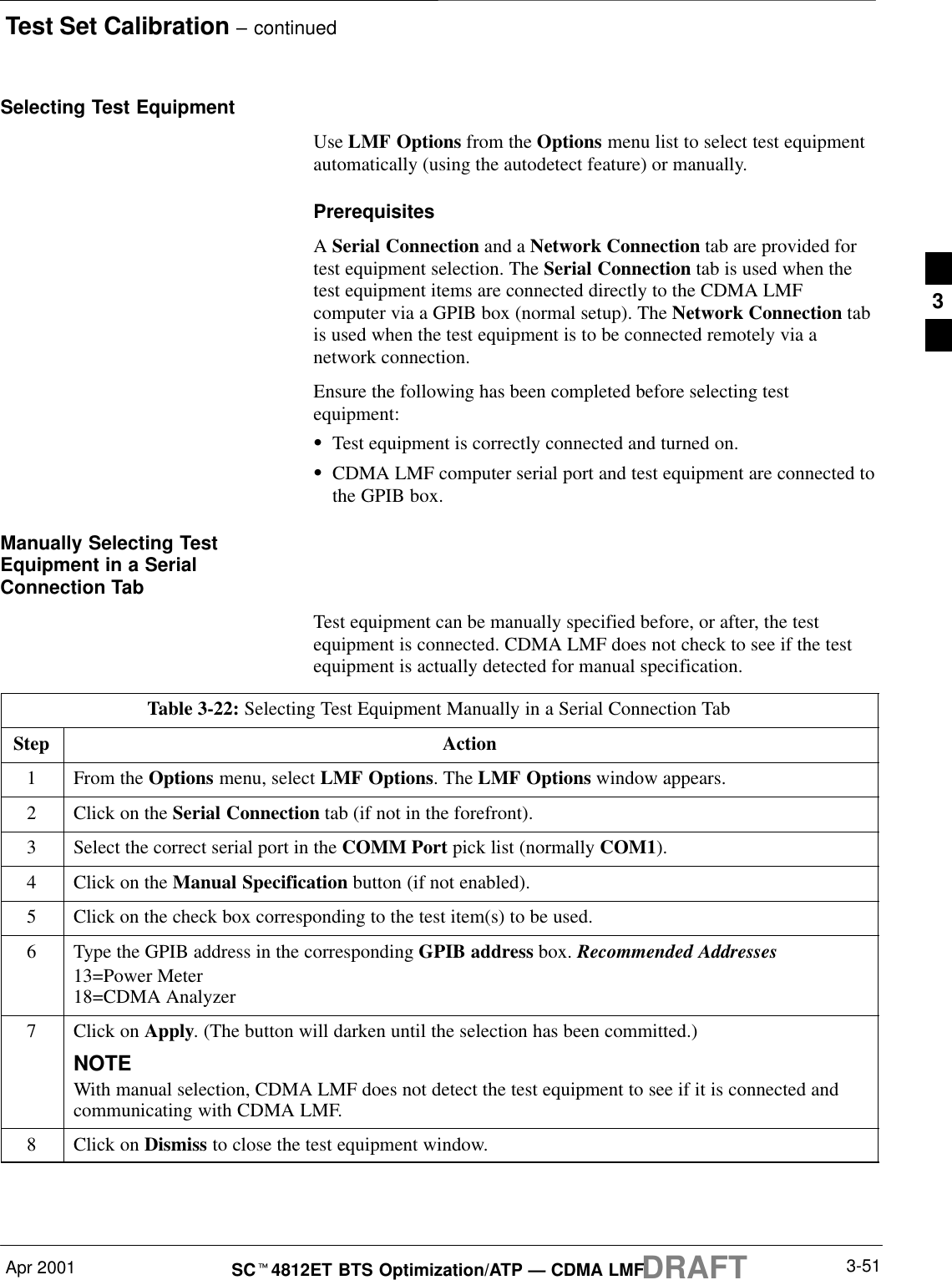
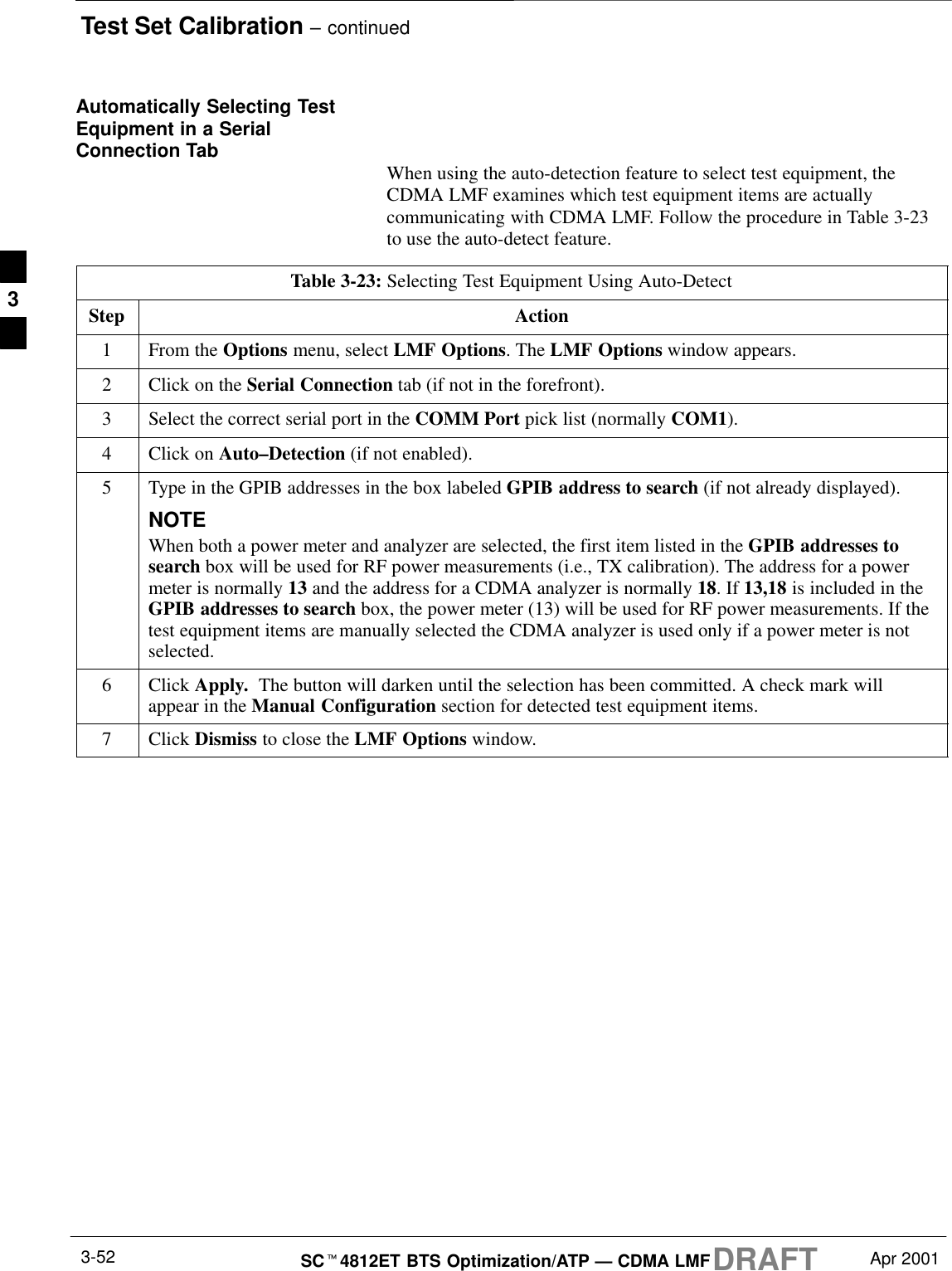
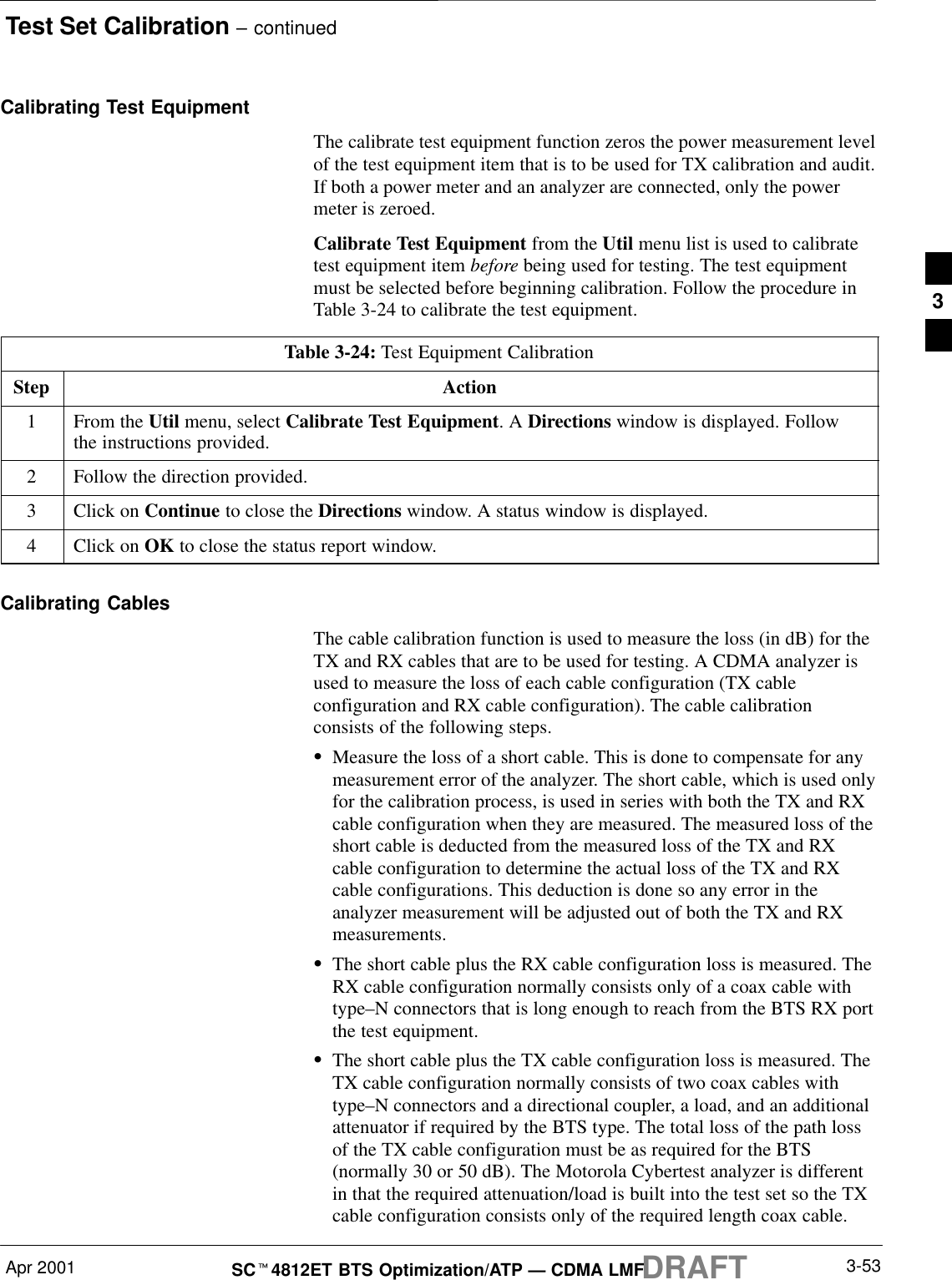
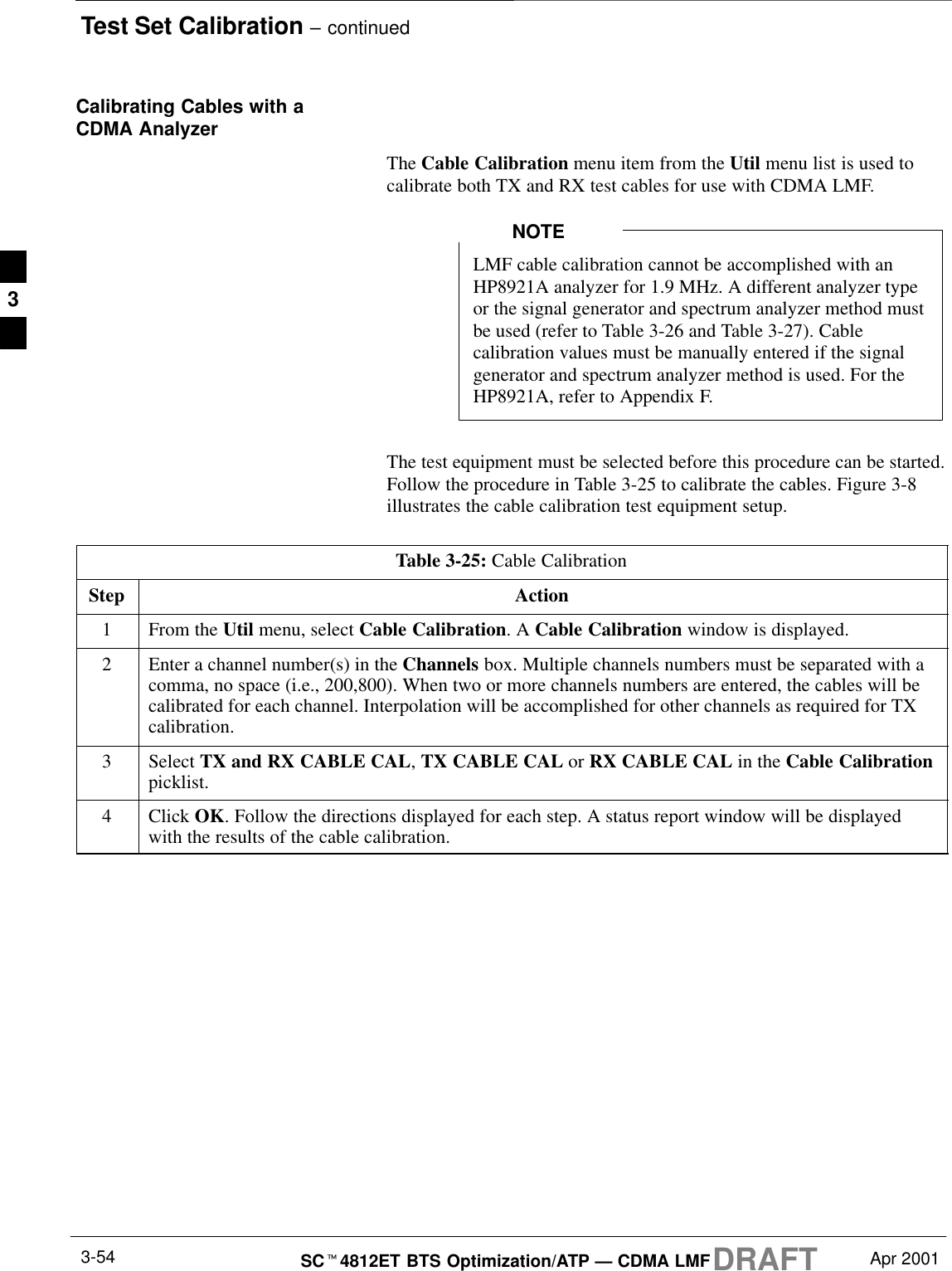
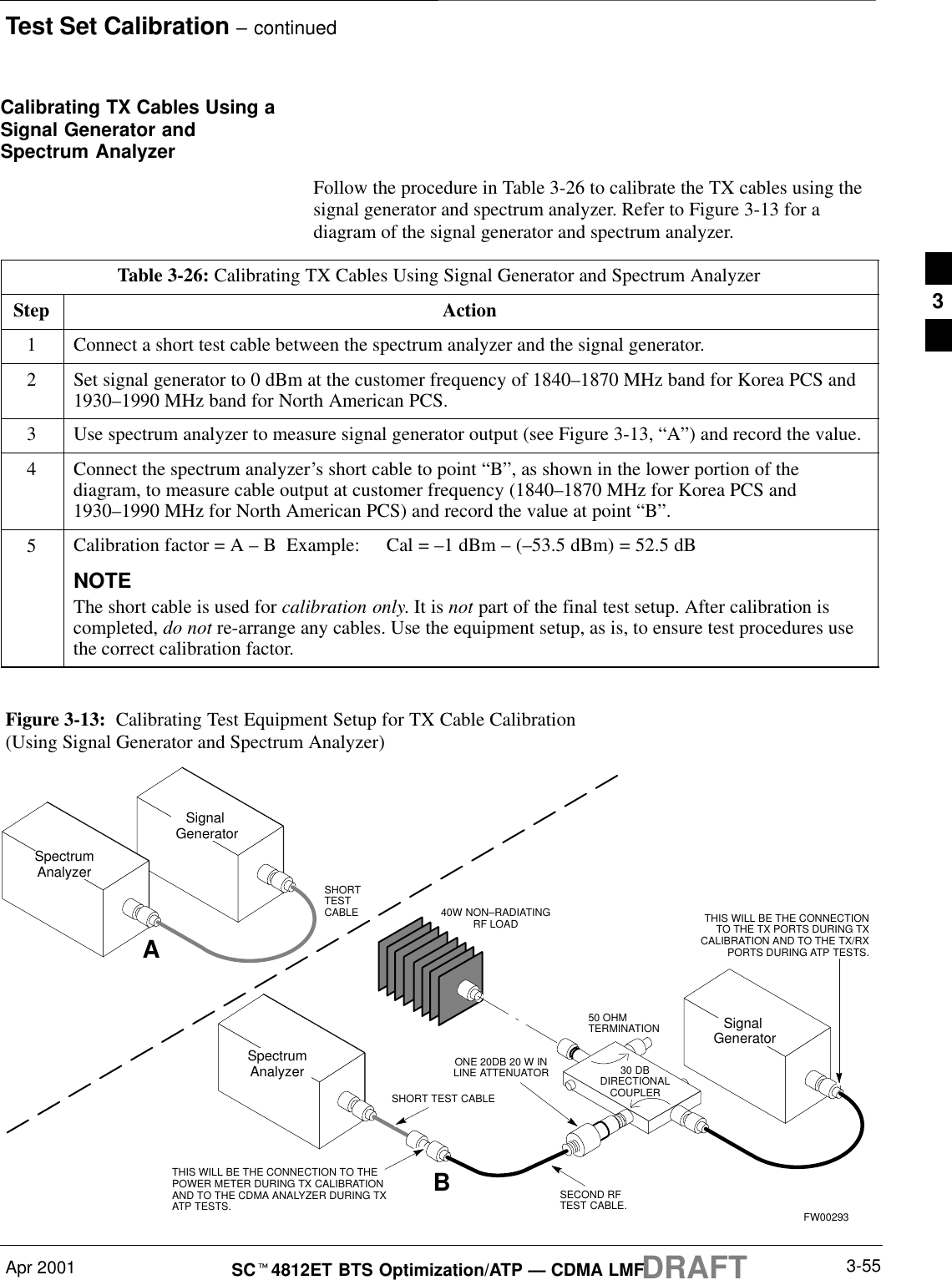
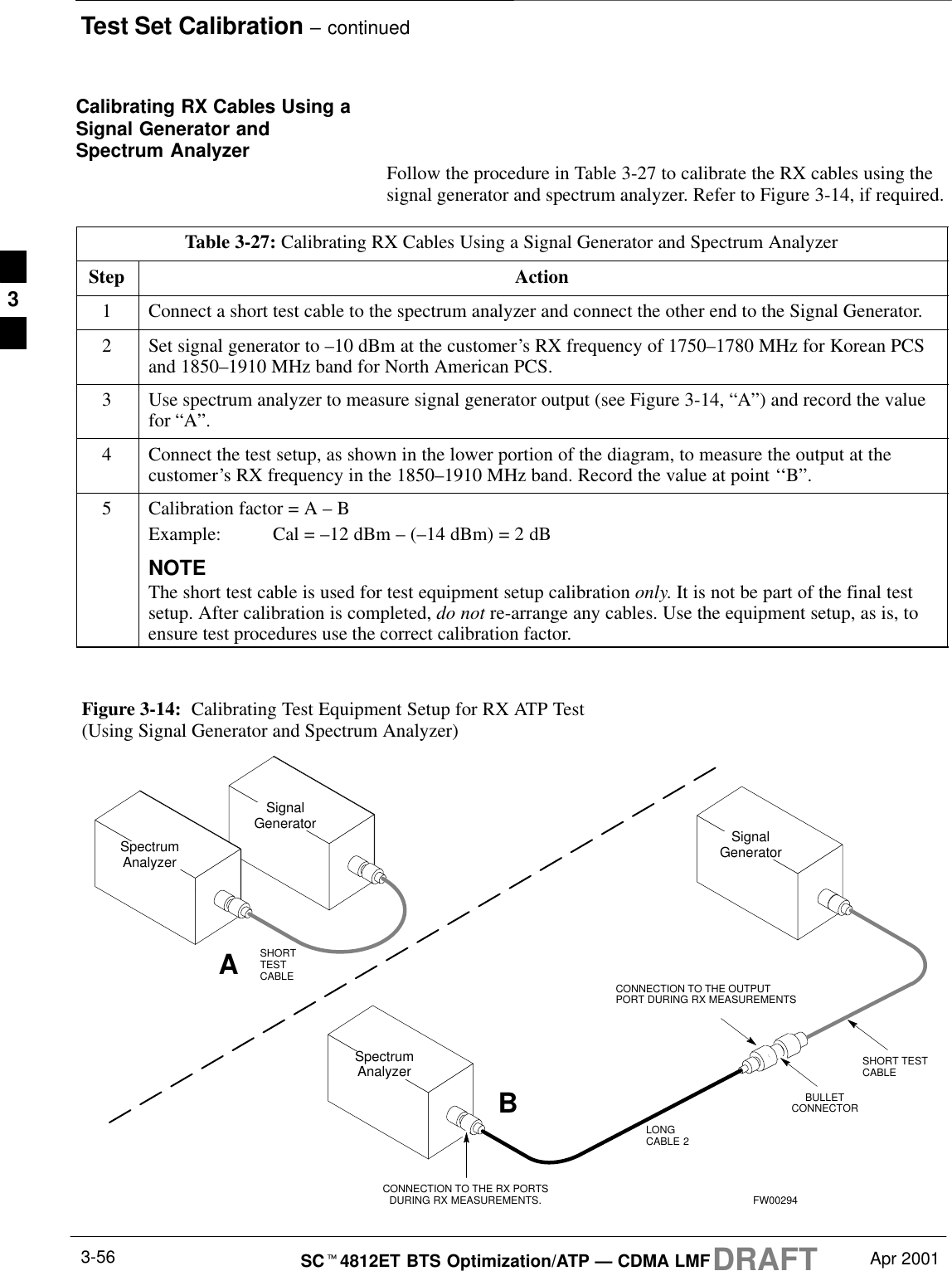
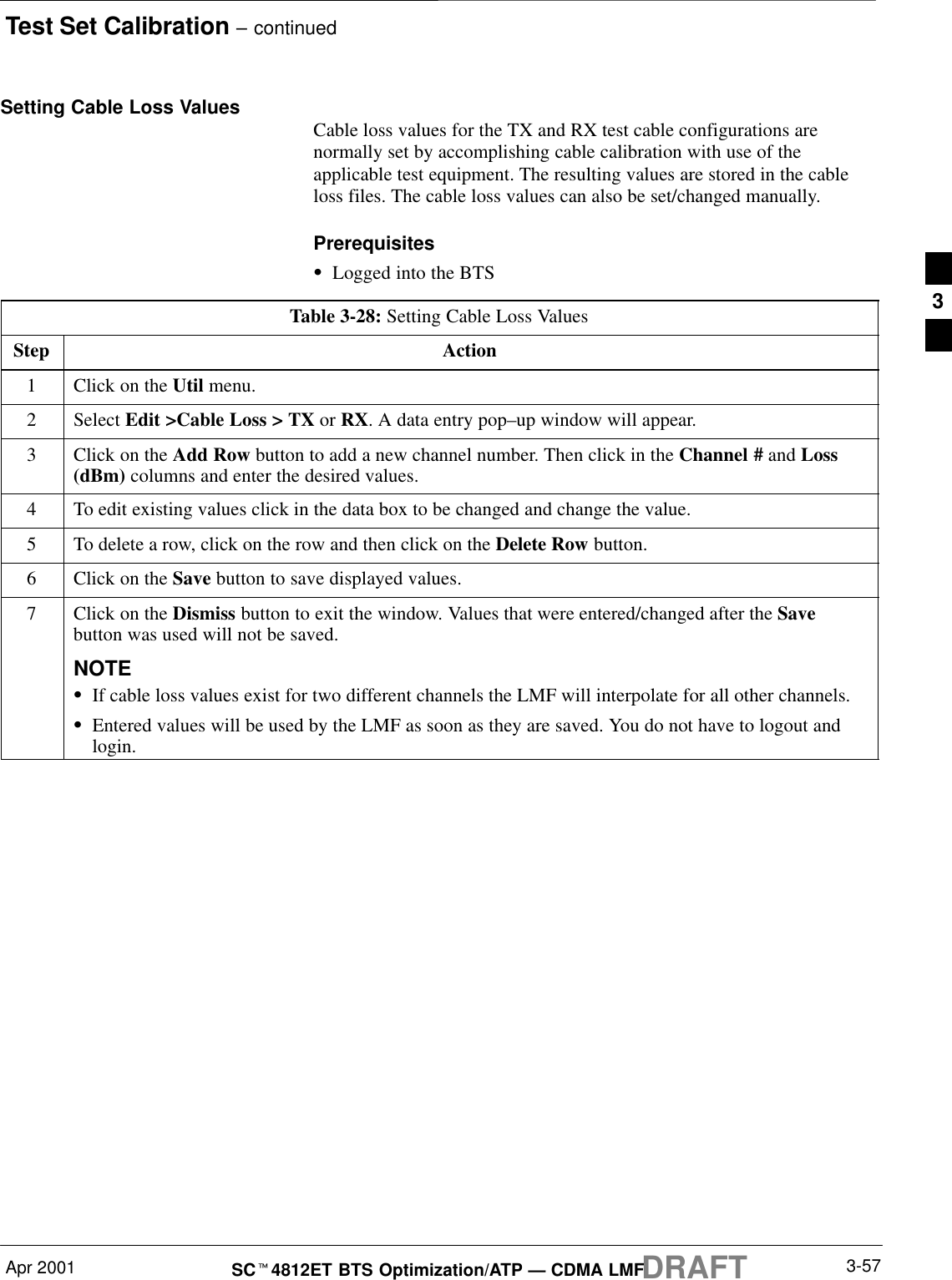
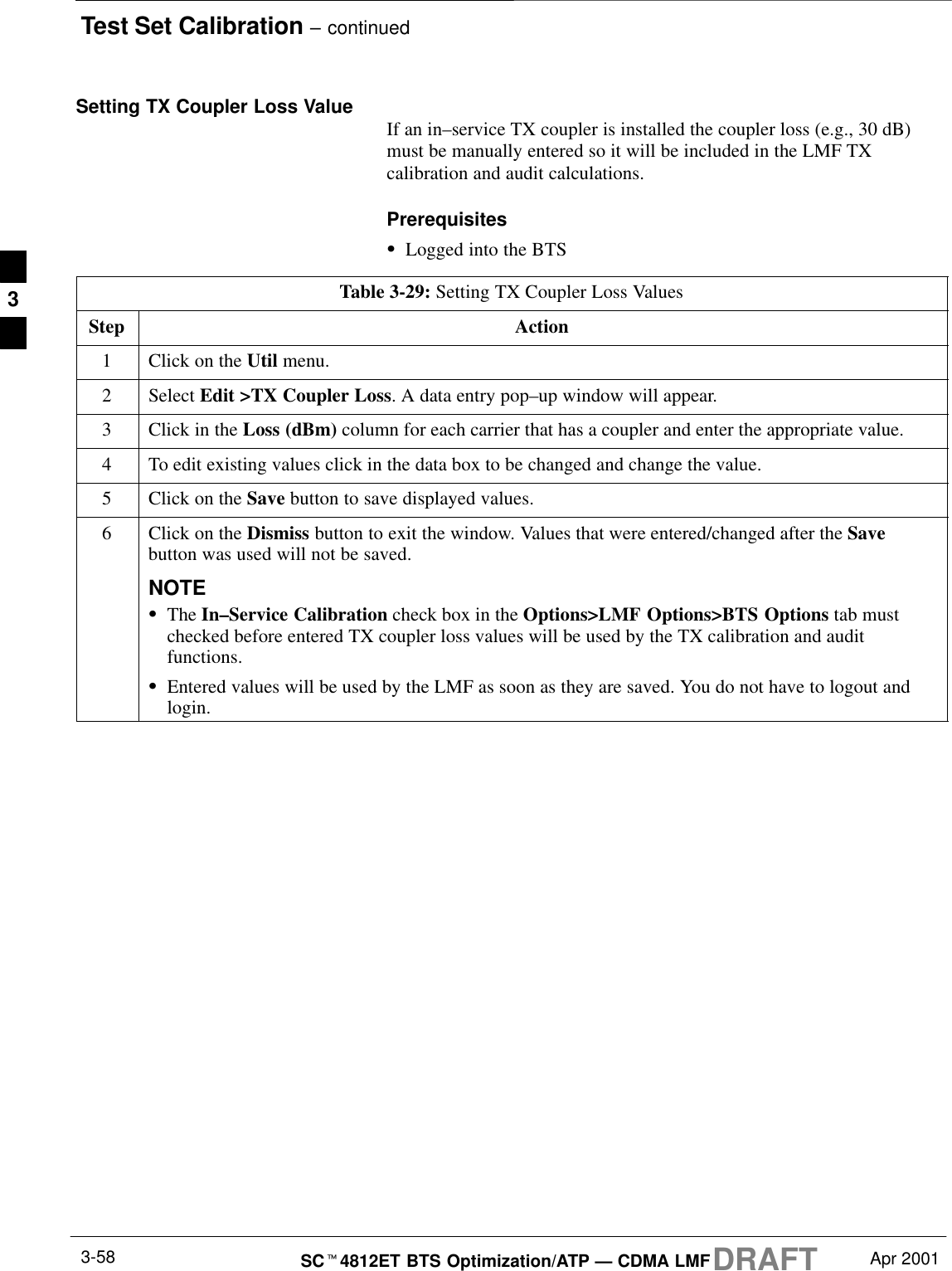

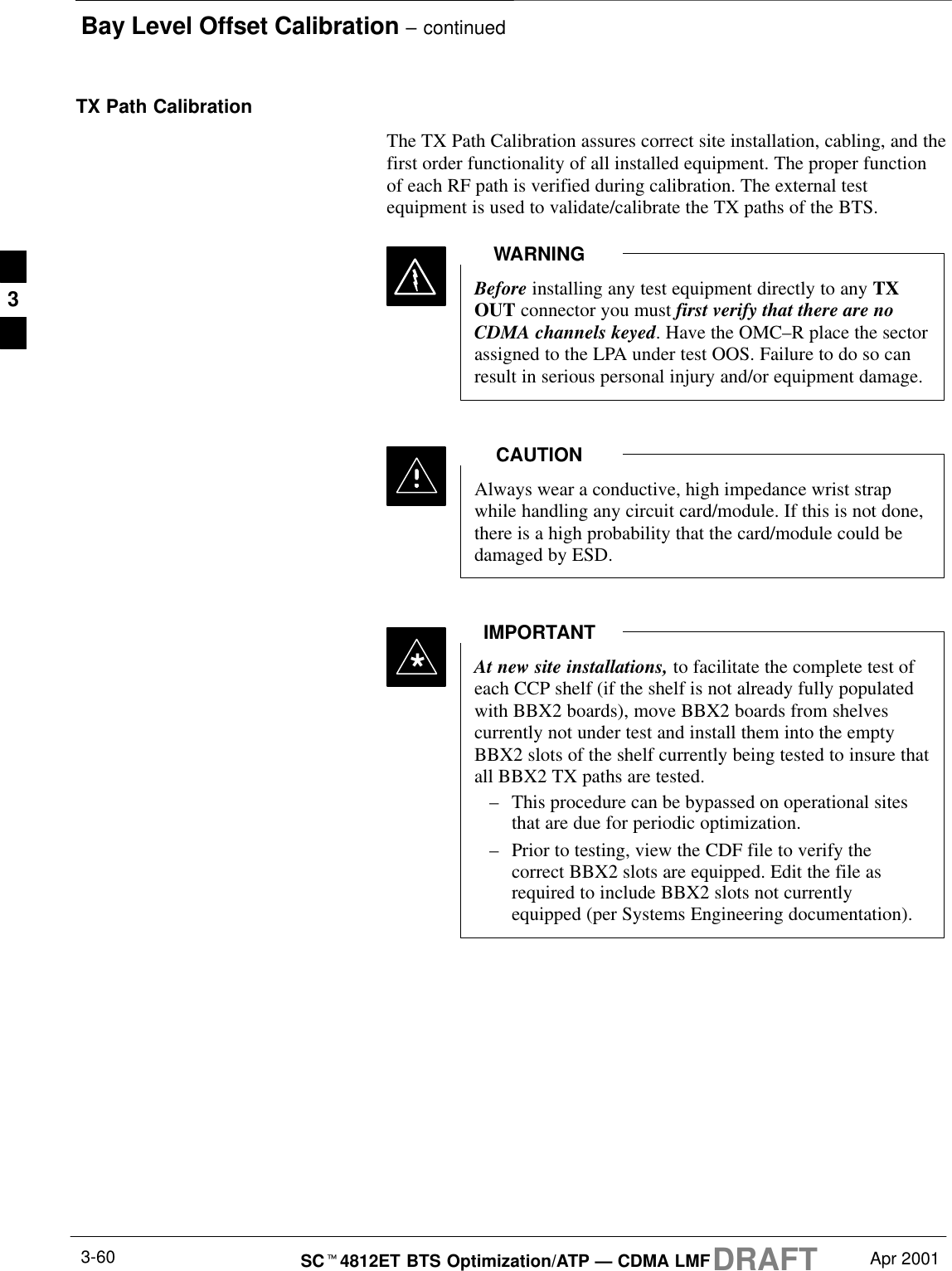
![Bay Level Offset Calibration – continuedApr 2001 3-61SCt4812ET BTS Optimization/ATP — CDMA LMFDRAFTBLO Calibration Data FileDuring the calibration process, the LMF creates a calibration (BLO) datafile. After calibration has been completed, this offset data must bedownloaded to the BBX2s using the Download BLO function. Anexplanation of the file is shown below.Due to the size of the file, Motorola recommends that youprint out a hard copy of a bts.cal file and refer to it for thefollowing descriptions.NOTEThe CAL file is subdivided into sections organized on a per slot basis (aslot Block).Slot 1 contains the calibration data for the 12 BBX2 slots. Slot 20contains the calibration data for the redundant BBX2 (see Table 3-31).Each BBX2 slot header block contains:SA creation Date and Time – broken down into separate parameters ofcreateMonth, createDay, createYear, createHour, and createMin.SThe number of calibration entries – fixed at 720 entries correspondingto 360 calibration points of the CAL file including the slot header andactual calibration data.SThe calibration data for a BBX2 is organized as a large flat array. Thearray is organized by branch, BBX2 slot, and calibration point.–The first breakdown of the array indicates which branch thecontained calibration points are for. The array covers transmit, mainreceive and diversity receive offsets as follows:Table 3-30: BLO BTS.cal file Array Branch AssignmentsRange AssignmentC[1]–C[240] TransmitC[241]–C[480] ReceiveC[481]–C[720] Diversity Receive3](https://usermanual.wiki/Nokia-Solutions-and-Networks/T5BQ1.IHET5BQ1-User-Manual-Part-2-of-3/User-Guide-167950-Page-75.png)
![Bay Level Offset Calibration – continuedDRAFTSCt4812ET BTS Optimization/ATP — CDMA LMF Apr 20013-62–The second breakdown of the array is per sector. Three sectors areallowed.Table 3-31: BTS.cal File Array (Per Sector)BBX2 Sectorization TX RX RX DiversitySlot[1] (Primary BBX2s 1 through 12)1 (Omni) 3–Sector, C[1]–C[20] C[241]–C[260] C[481]–C[500]23–Sector,1st C[21]–C[40] C[261]–C[280] C[501]–C[520]36 Sector, Carrier C[41]–C[60] C[281]–C[300] C[521]–C[540]41stCarrier 3–Sector, C[61]–C[80] C[301]–C[320] C[541]–C[560]5Carrier 3–Sector,3rd C[81]–C[100] C[321]–C[340] C[561]–C[580]6Carrier C[101]–C[120] C[341]–C[360] C[581]–C[600]73–Sector, C[121]–C[140] C[361]–C[380] C[601]–C[620]83–Sector,2nd C[141]–C[160] C[381]–C[400] C[621]–C[640]96 Sector, Carrier C[161]–C[180] C[401]–C[420] C[641]–C[660]10 2ndCarrier 3–Sector, C[181]–C[200] C[421]–C[440] C[661]–C[680]11 Carrier 3–Sector,4th C[201]–C[220] C[441]–C[460] C[681]–C[700]12 Carrier C[221]–C[240] C[461]–C[480] C[701]–C[720]Slot[20] (Redundant BBX2–13)1 (Omni) 3–Sector, C[1]–C[20] C[241]–C[260] C[481]–C[500]23–Sector,1st C[21]–C[40] C[261]–C[280] C[501]–C[520]36 Sector, Carrier C[41]–C[60] C[281]–C[300] C[521]–C[540]41stCarrier 3–Sector, C[61]–C[80] C[301]–C[320] C[541]–C[560]5Carrier 3–Sector,3rd C[81]–C[100] C[321]–C[340] C[561]–C[580]6Carrier C[101]–C[120] C[341]–C[360] C[581]–C[600]73–Sector, C[121]–C[140] C[361]–C[380] C[601]–C[620]83–Sector,2nd C[141]–C[160] C[381]–C[400] C[621]–C[640]96 Sector, Carrier C[161]–C[180] C[401]–C[420] C[641]–C[660]10 2ndCarrier 3–Sector, C[181]–C[200] C[421]–C[440] C[661]–C[680]11 Carrier 3–Sector,4th C[201]–C[220] C[441]–C[460] C[681]–C[700]12 Carrier C[221]–C[240] C[461]–C[480] C[701]–C[720]SRefer to the hard copy of the file. As you can see, 10 calibrationpoints per sector are supported for each branch. Two entries arerequired for each calibration point.SThe first value (all odd entries) refer to the CDMA channel(frequency) the BLO is measured at. The second value (all evenentries) is the power set level. The valid range for PwrLvlAdj is from2500 to 27500 (2500 corresponds to –125 dBm and 27500corresponds to +125 dBm).3](https://usermanual.wiki/Nokia-Solutions-and-Networks/T5BQ1.IHET5BQ1-User-Manual-Part-2-of-3/User-Guide-167950-Page-76.png)
![Bay Level Offset Calibration – continuedApr 2001 3-63SCt4812ET BTS Optimization/ATP — CDMA LMFDRAFTSThe 20 calibration entries for each slot/branch combination must bestored in order of increasing frequency. If less than 10 points(frequencies) are calibrated, the largest frequency that is calibrated isrepeated to fill out the 10 points.Example:C[1]=384, odd cal entry = 1 ‘‘calibration point”C[2]=19102, even cal entryC[3]=777,C[4]=19086,..C[19]=777,C[20]=19086, (since only two cal points were calibrated this would be repeated for the next 8 points)SWhen the BBX2 is loaded with BLO data, the cal file data for theBBX2 is downloaded to the device in the order it is stored in the CALfile. TxCal data is sent first, C[1] – C[60]. BBX2 slot 1’s 10calibration points are sent (C[1] – C[20]), followed by BBX2 slot 2’s10 calibration points (C[21] – C[40]), etc. The RxCal data is sent next,followed by the RxDCal data.STemperature compensation data is also stored in the cal file for eachslot.Test Equipment Setup:RF Path CalibrationFollow the steps outlined in Table 3-32 to set up test equipment.Table 3-32: Test Equipment Setup (RF Path Calibration)Step ActionNOTEVerify the GPIB is properly connected and turned on.! CAUTIONTo prevent damage to the test equipment, all transmit (TX) test connections must be via the 30 dBdirectional coupler for 800 MHz or via a 30 dB coupler with a 20 dB in–line attenuator for 1900 MHz.1Connect the LMF computer terminal to the BTS LAN A connector on the BTS (if you have notalready done so). Refer to the procedure in Table 3-6.SIf required, calibrate the test equipment per the procedure in Table 3-24.SConnect the test equipment as shown in Figure 3-9 and Figure 3-10.3](https://usermanual.wiki/Nokia-Solutions-and-Networks/T5BQ1.IHET5BQ1-User-Manual-Part-2-of-3/User-Guide-167950-Page-77.png)
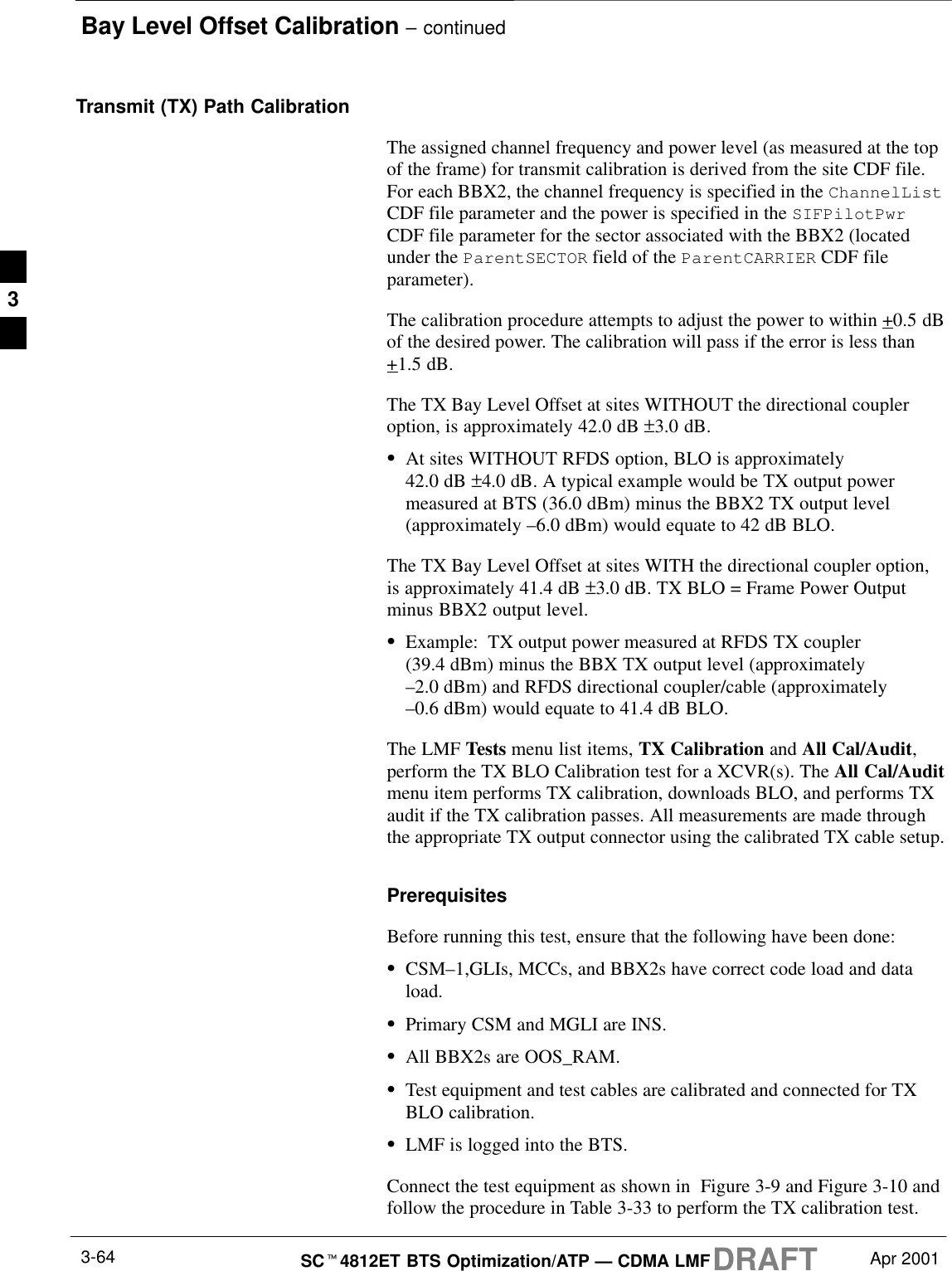
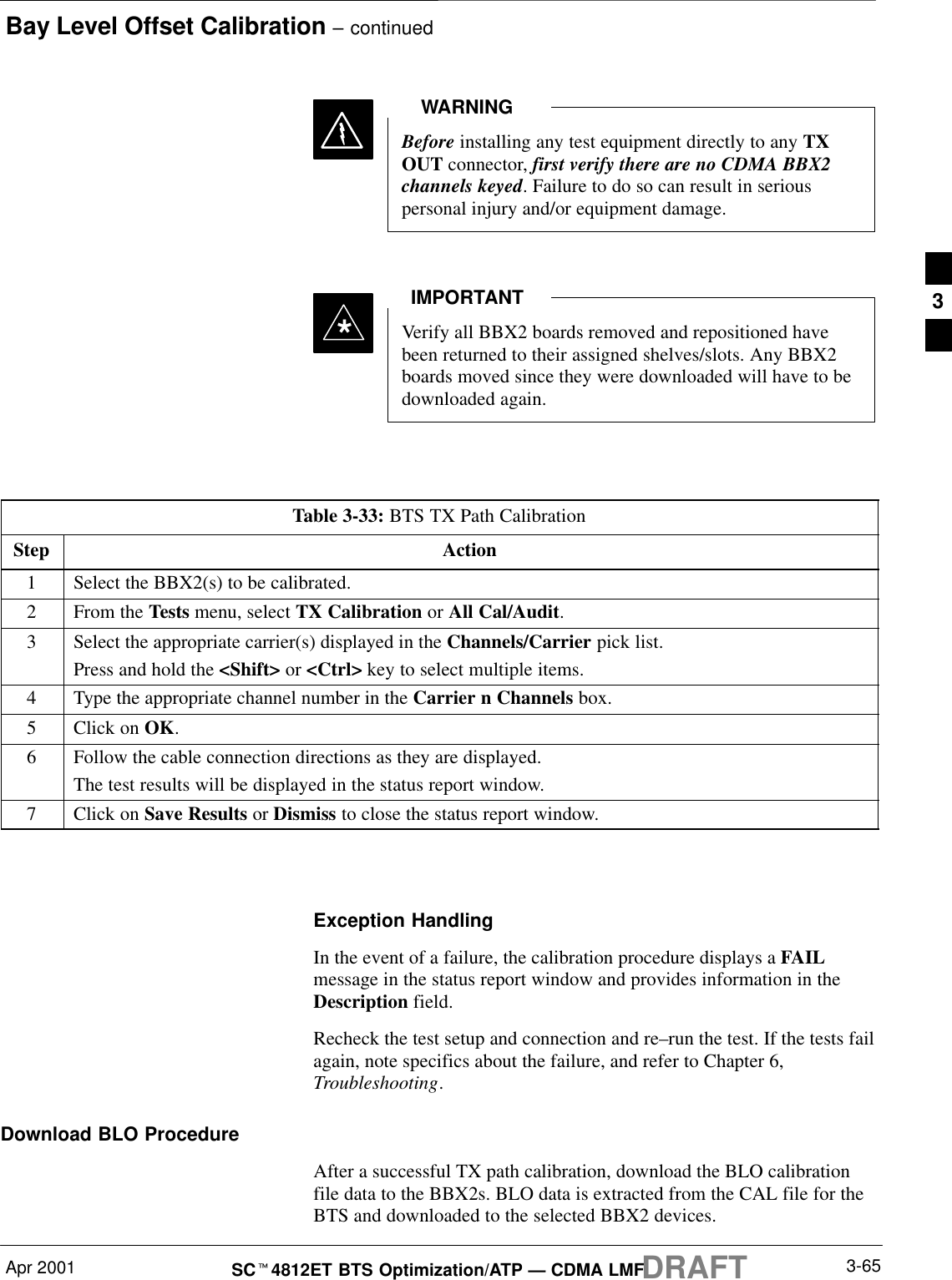
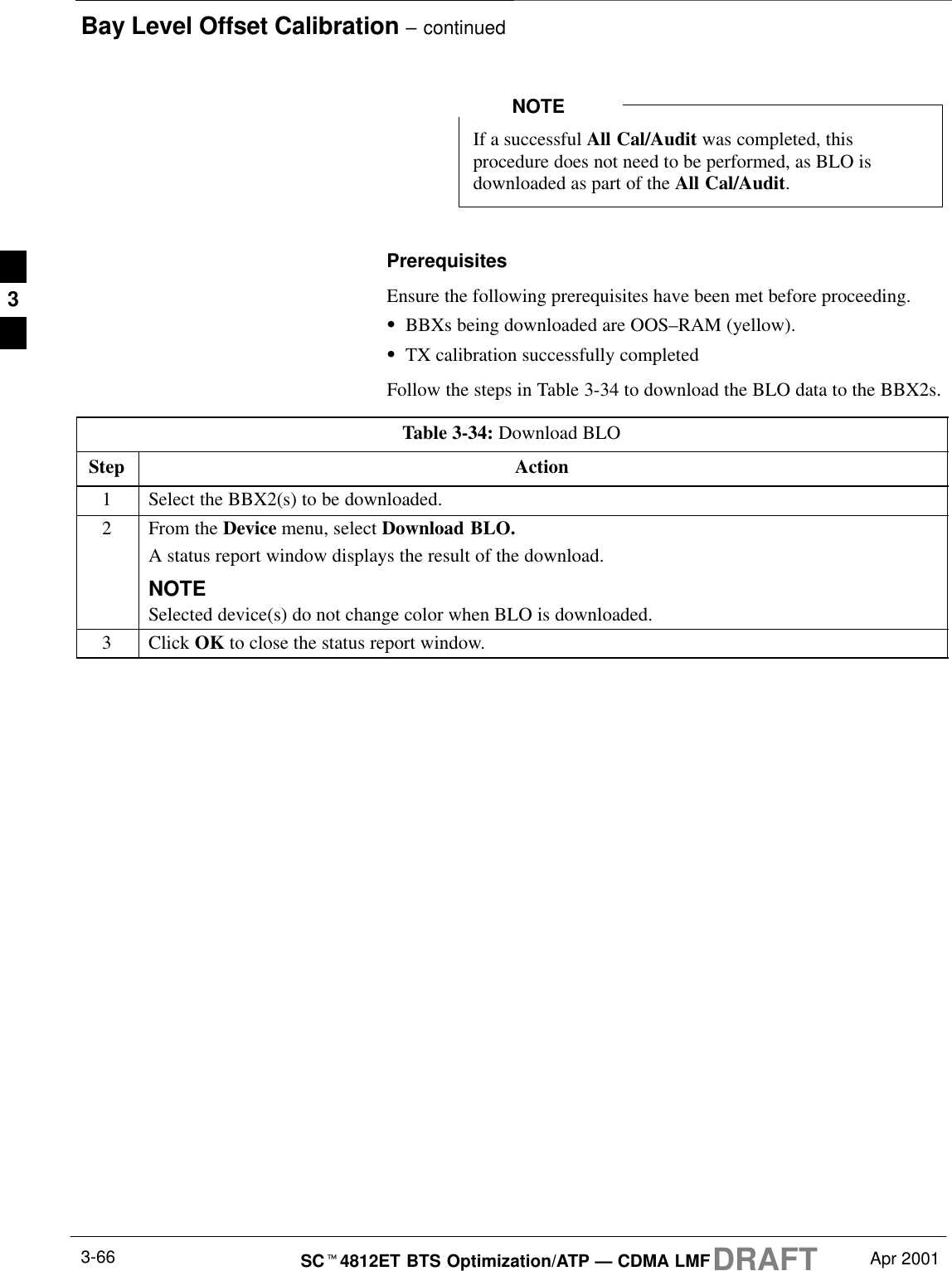
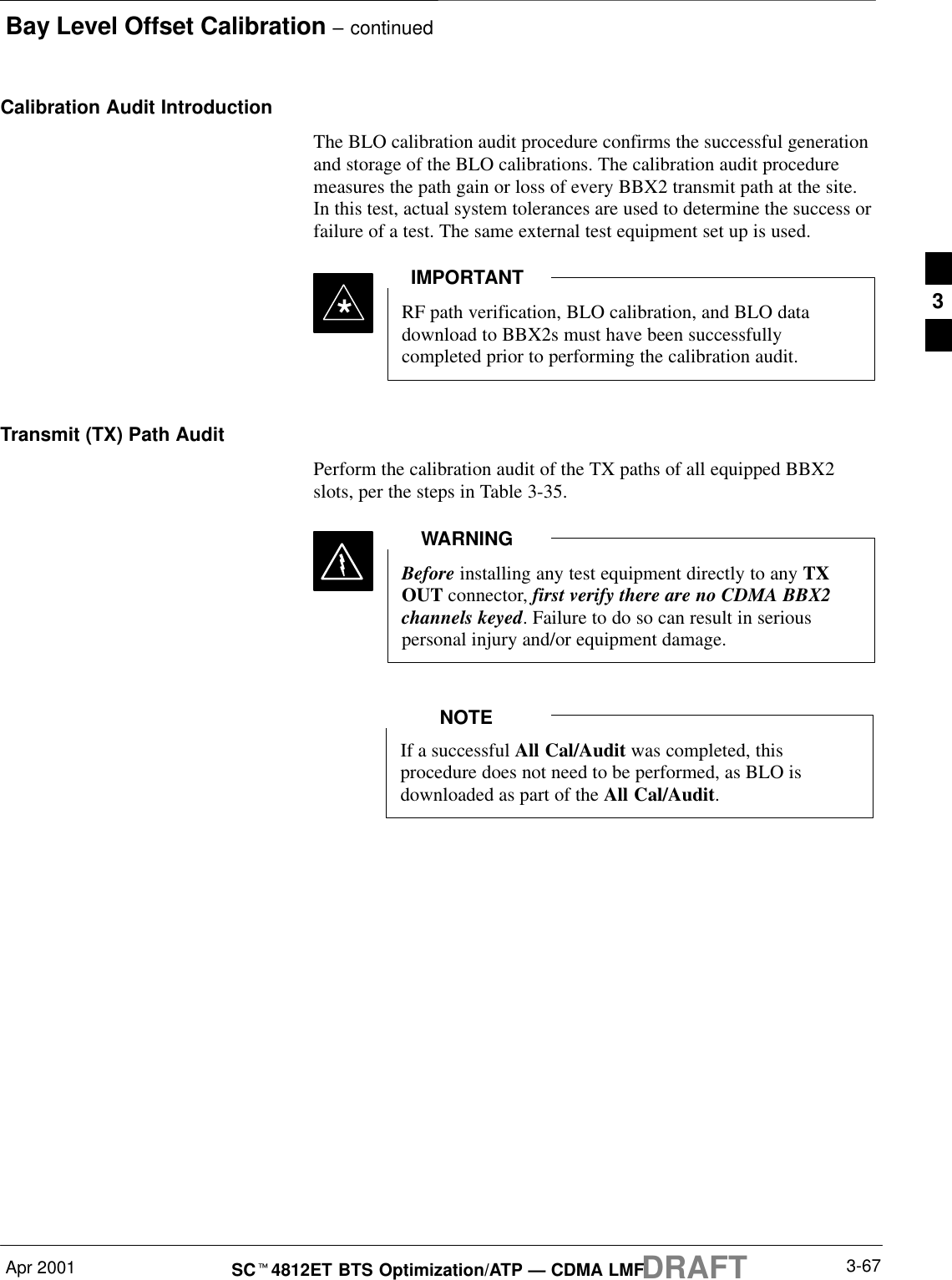
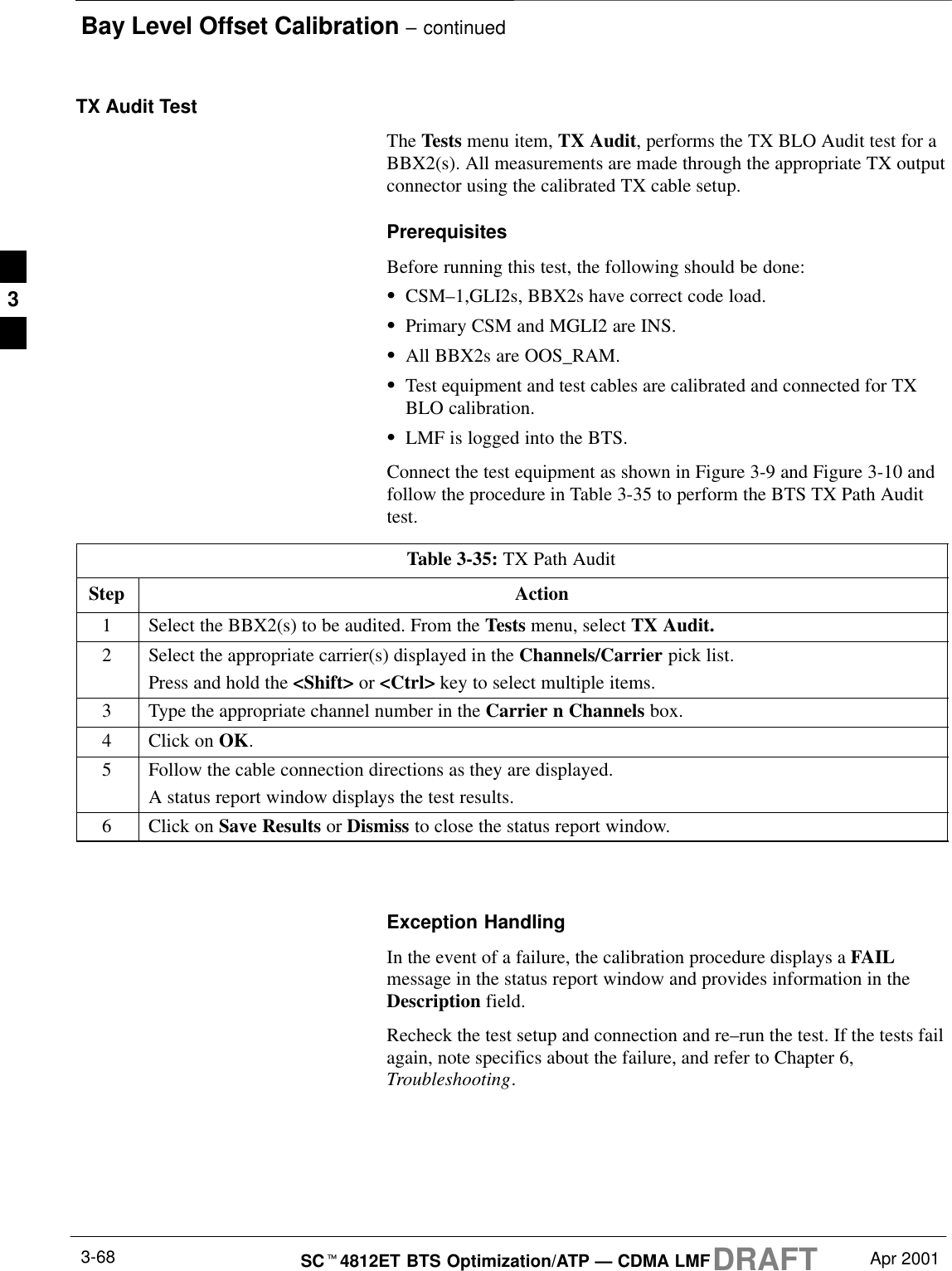
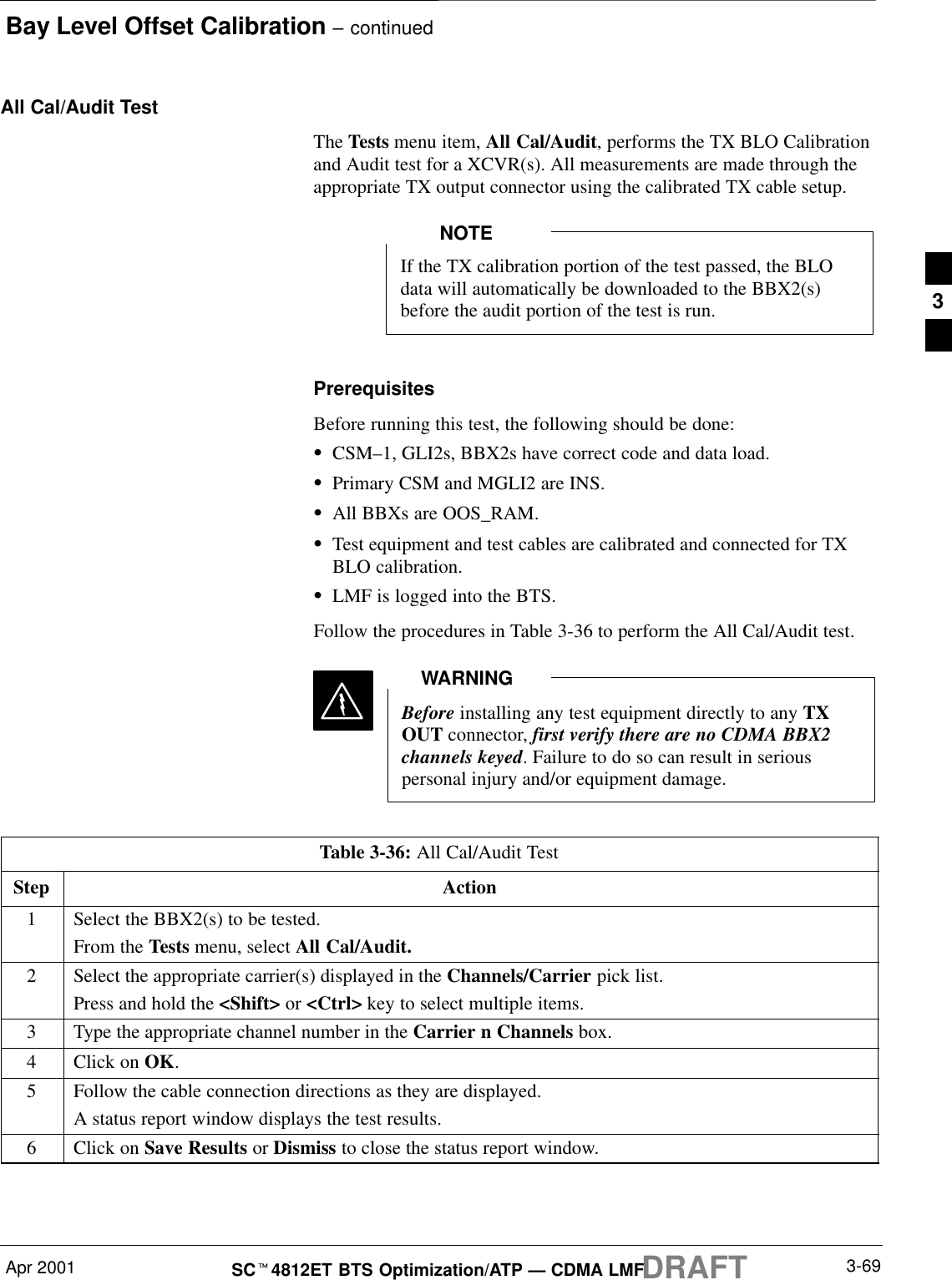
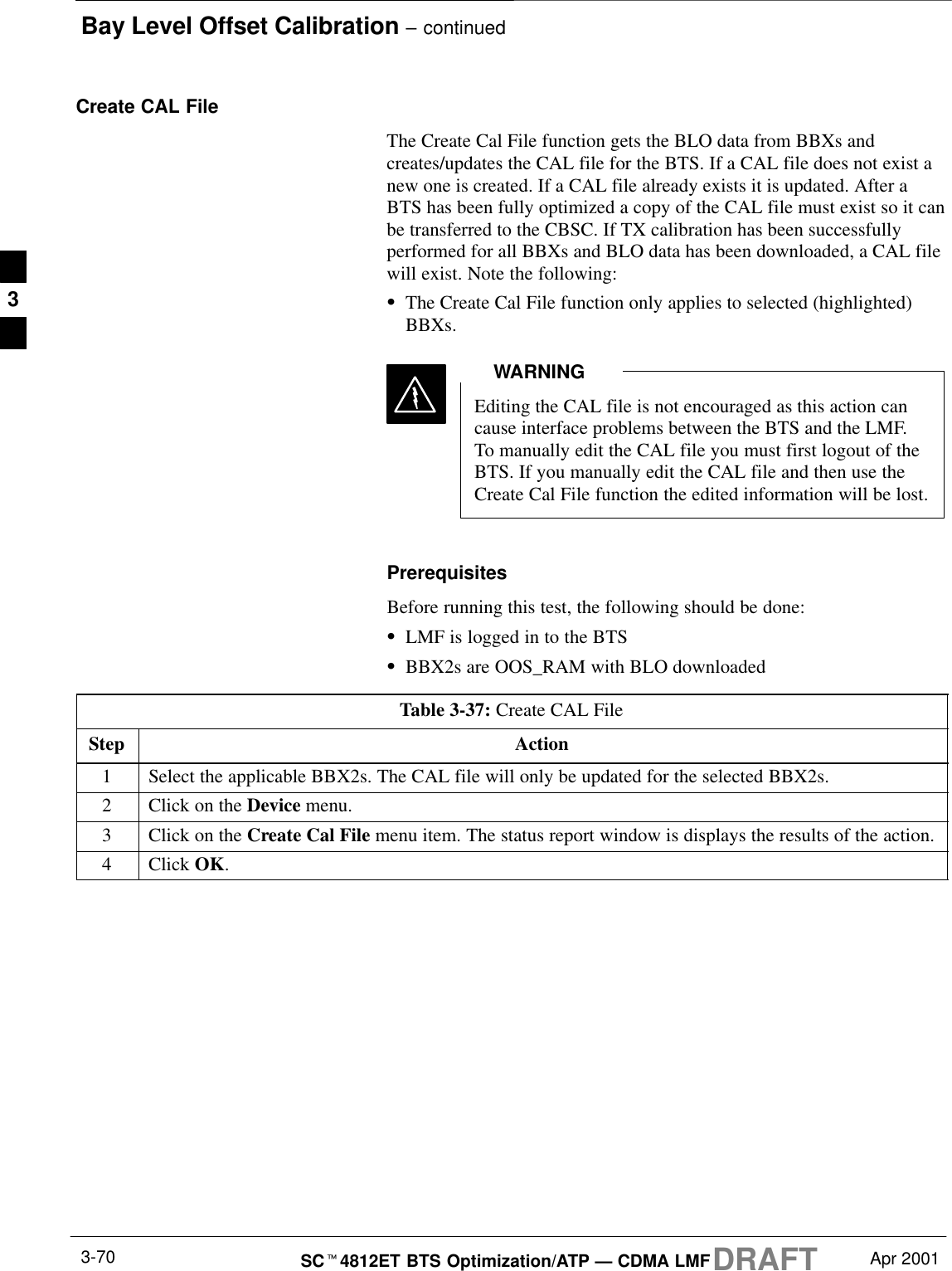